Designing a spacecraft or a piece of equipment in order to achieve its demise means enhancing its capability to destroy during the re-entry, so that fewer and smaller pieces are likely to reach the ground.

Among the various studies performed on this topic, some focused on the system level and others on the equipment level. The former tried to develop a method that would increase the demise of the overall satellite, while the latter focused on specific critical elements.
During reentry, a satellite experiences high heat fluxes and mechanical loads that usually lead to its break-up at around 75 km up. Only from this altitude is all the internal equipment exposed to the heat flux to start demising as well. Having a higher break-up altitude would imply that the internal equipment would be exposed to the heat flux for a longer time, greatly enhancing its demise.
Accordingly, in recent years many studies were focused on achieving a satellite’s early break-up.
The outer structure of a spacecraft is usually made of metallic honeycomb panels. These panels are held together by joints. The early melting or break-up of such joints would lead to an early separation of the panels.
There have been many ideas about how to achieve an early break-up. The two identified by an OHB study to be the most promising are demisable joints and Shape Memory Alloys (SMA) cylinders for bolt fractures.
Making the joints demisable means finding a way to make them melt or destroy earlier and easier than would happen with traditional technologies. This was the aim of an investigation carried out by Thales Alenia Space Italy between 2019 and 2020. They had to tackle a tricky challenge: find a material reliable enough to resist launch stress and a long lifetime in space, but still be easily demisable in the reentry phase.
They took a joint inspired by the Copernicus Sentinel satellites, which was made of two cleats glued to the panels and kept together by a screw. Improving the demisability of the joint focused on the washer, a disk-shaped thin plate present between the screw and the cleat that distributes the load of the fastener on the cleat.
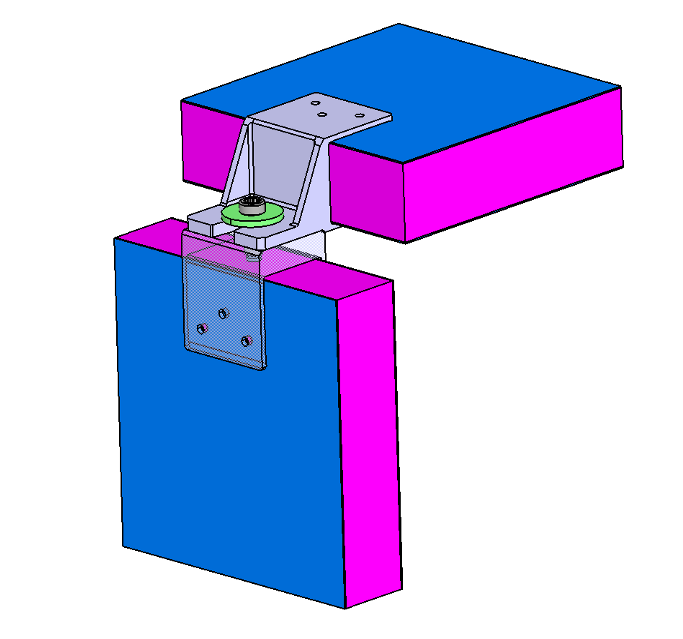
One of the cleats was modified to include a hole that would allow the panels to slide after the demise of the washer. First, many simulations were carried out to investigate the behavior of different materials and to discover if and how the position of the joint would impact its demise. The conclusion of this preliminary study was that the washer demises in an expected altitude range, relative to the other components of the spacecraft. After having chosen a few promising materials, they proceed to plan the test campaign, which would include tests in the L2K Plasma Wind Tunnel (PWT) of the German Aerospace Center (Germany) and in the static facility of ELEMENT (Italy).
In the L2K facility it was possible to replicate the strong heat flux that the satellite would experience during reentry, but not the mechanical loads. A clamp would hold one of the pieces of the panels, while the joint would be exposed to the flux. It is extremely important to ensure that heat conduction between the test breadboard and the supporting mechanism is kept as low as possible, otherwise this could compromise the validity of the test. That is why an insulation layer was placed between the clamp and the panel.
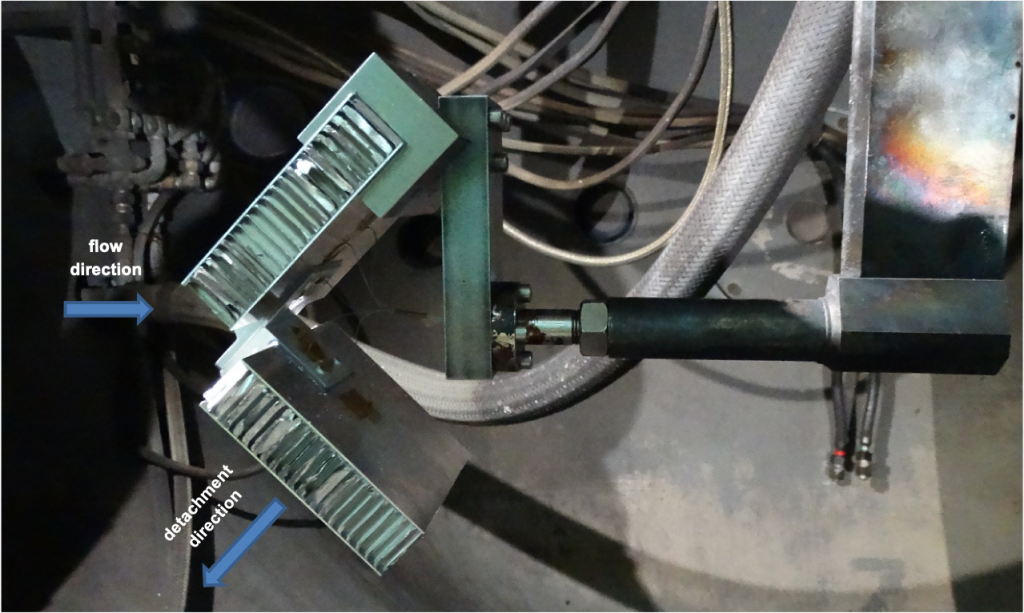
These tests demonstrated that the heat would make the washer melt and the flux would even remove the melted material from the joint, if the viscosity of the material was low enough. However, it was noticed during that the melting of the washer was not always enough to guarantee separation: the forces acting on the panels and the configuration of the demisable joint were also driving factors in the separation.

The purpose of testing the demisable joint in a static facility is to assess the effect of the limited mechanical loads that are expected to act on it during the first phases of reentry. Indeed, they could avail the joint separation, which could happen even before the melting temperature of the washer is reached. In this case, the test breadboard was composed of the joint only, without pieces of the panels. A machine was used to reproduce the mechanical stress on the breadboard. At the same time, the washer would be heated thanks to a retro-activated induction system capable of replicating the baseline temperature profile.
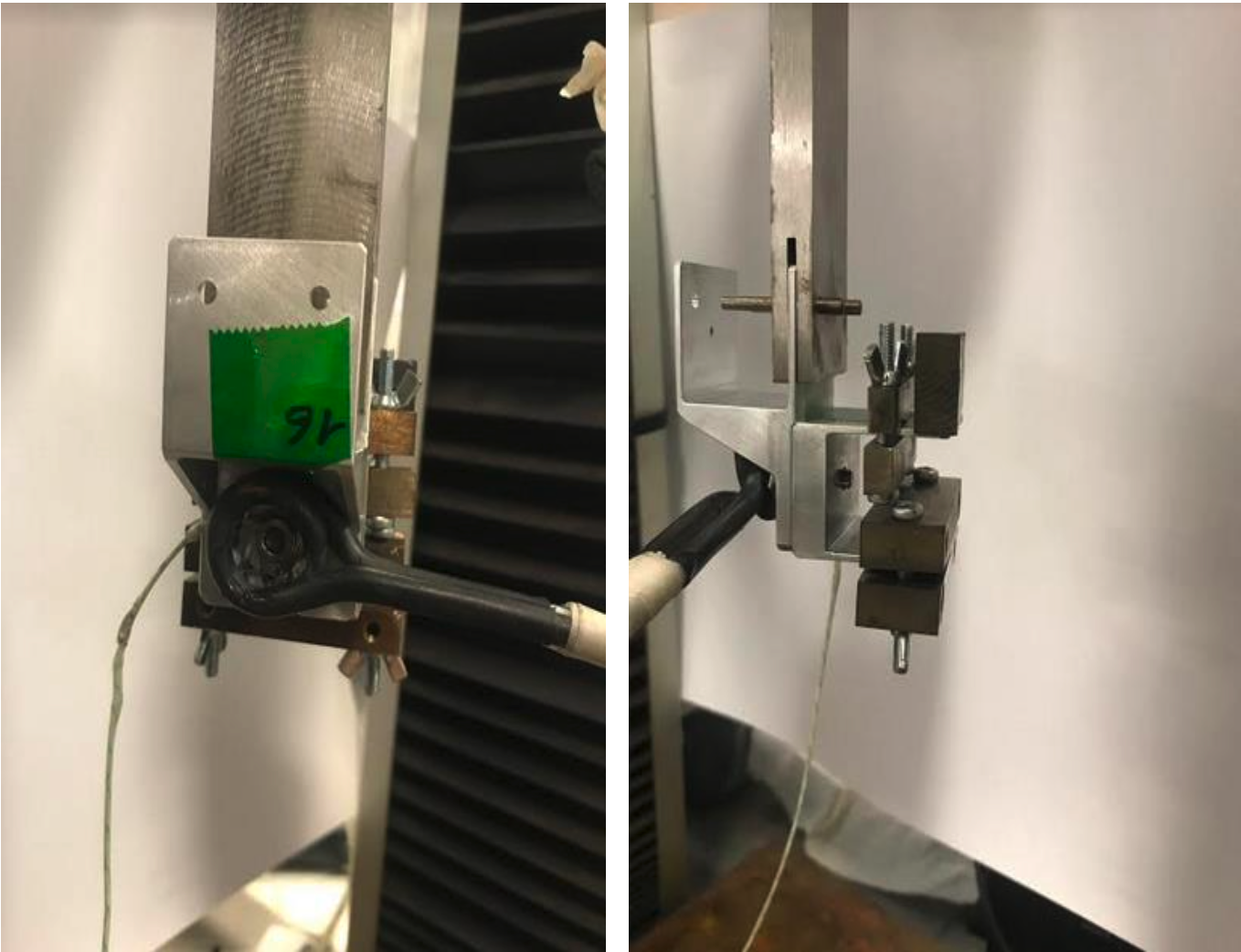
Testing in the static facility was challenging because it is particularly hard to correctly measure the temperature of the washer and to replicate the very small mechanical loads. Despite these difficulties, some tests clearly showed that it was possible to obtain an early separation of the joint, as shown in Figure 6.
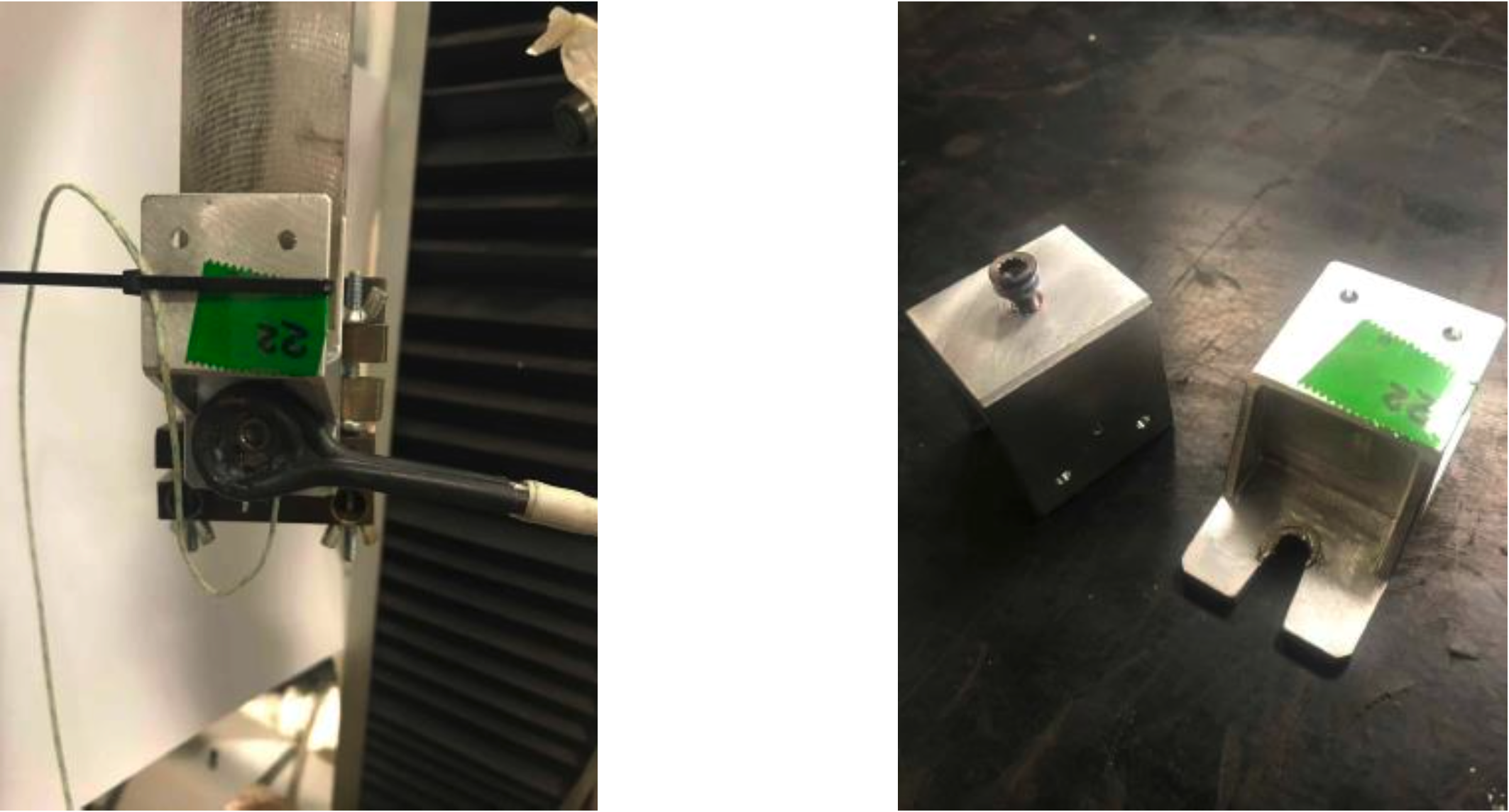
Thales Alenia Space Italy concluded successfully this study, having proven through breadboard development and testing that the proposed solution to achieve early break-up is feasible.
However, this does not mean that the washer is already ready to fly, because further investigations are still needed.
For example, a topic that causing some concern relates to the Multi-layer Insulation (MLI). The MLI is composed of various layers of sheets which ensure the thermal insulation of the spacecraft during its operational lifetime in space. The MLI also covers many external components of satellites, including the joints. Usually, during the re-entry, the MLI is destroyed at current break-up altitudes by the high mechanical loads or by the interaction with atomic oxygen in the atmosphere. Only after the MLI is teared away are the external components directly exposed to the heat. However, at higher altitudes, the MLI might still be in place and prevent the heating of demisable joints or SMA actuators. Therefore, the foreseen early break-up would not happen. To better understand the effect of the MLI presence during the re-entry, first it is necessary to improve knowledge aboutits condition after the mission and orbital decay. Subsequently, tests should be carried out to assess its influence on the break-up of the mission.
Avoiding the creation of new space debris by reentering them in the atmosphere should become the norm and making sure that the reentry is as safe as possible is for sure a priority for all space companies and agencies. That is why various other studies are still on-going, involving different technologies that could make future spacecraft more demisable. It is likely that further new approaches will also be investigated in the future.
This post has been prepared by Benedetta Cattani, currently performing her internship within the ESA Clean Space team
Discussion: 3 comments
many thanks for all the details, both ideas sound cool! a standardization of the possible solutions could help all the space-industries, for a susteinable business we need to work on the end of life too. Environmental tests related to Materials & Processes are needed but they are only the first step for the development of next generation technical requirements!
So now you have 2 pieces of space junk instead of one? Is that an improvement?
Dear Gene,
This is an improvement as the smaller the piece, the faster it burns. This means that instead of having one large piece of spacecraft re-entering the atmosphere, and eventually landing on Earth, we will have two smaller pieces, which will partially or entirely burn during re-entry.
This way, you decrease the casualty risk.
I hope this reply to your question.
Have a lovely day,
Jessica