Engineers are born problem-solvers, and before ESA sends a 2.5-metre-long robot to Mars to load the sample tubes for delivery to Earth, they have devised a mechanism to avoid jams, misalignments and even damage during tube pick-up and transfer.
European teams are working together to consolidate the design of the Sample Transfer Arm (STA) for the Mars Sample Return campaign. “We are in the middle of a heated test campaign of prototypes to prove several key functions for the Sample Transfer Arm,” says Davide Nicolis, STA robotics engineer.
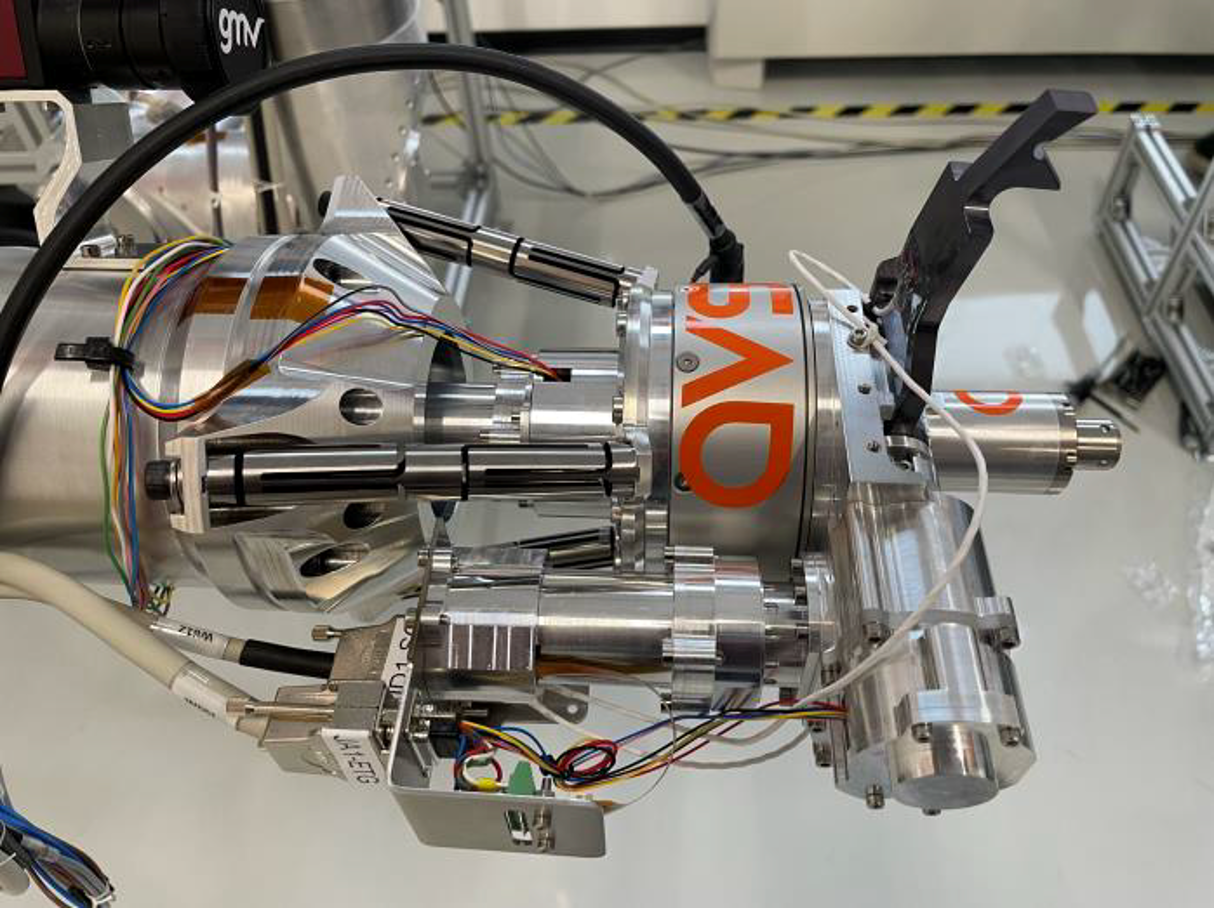
The Remote Centre of Compliance Mechanism connects the robotic arm and its ‘hand’, or end-effector. Credits: Leonardo/AVS
One of these units is the Remote Centre of Compliance Mechanism, which acts as an interface between the gripper and the rest of the robotic arm and plays a vital role in the Mars Sample Return campaign.
“This Remote Centre of Compliance Mechanism is essentially a large spring that will limit forces when needed. It ensures that the gripper can adjust its position in case of misalignment during the critical operations of collection and insertion into a rocket for the trip back home,” adds Phillip Brefka, systems engineer for Mars robotics at ESA.
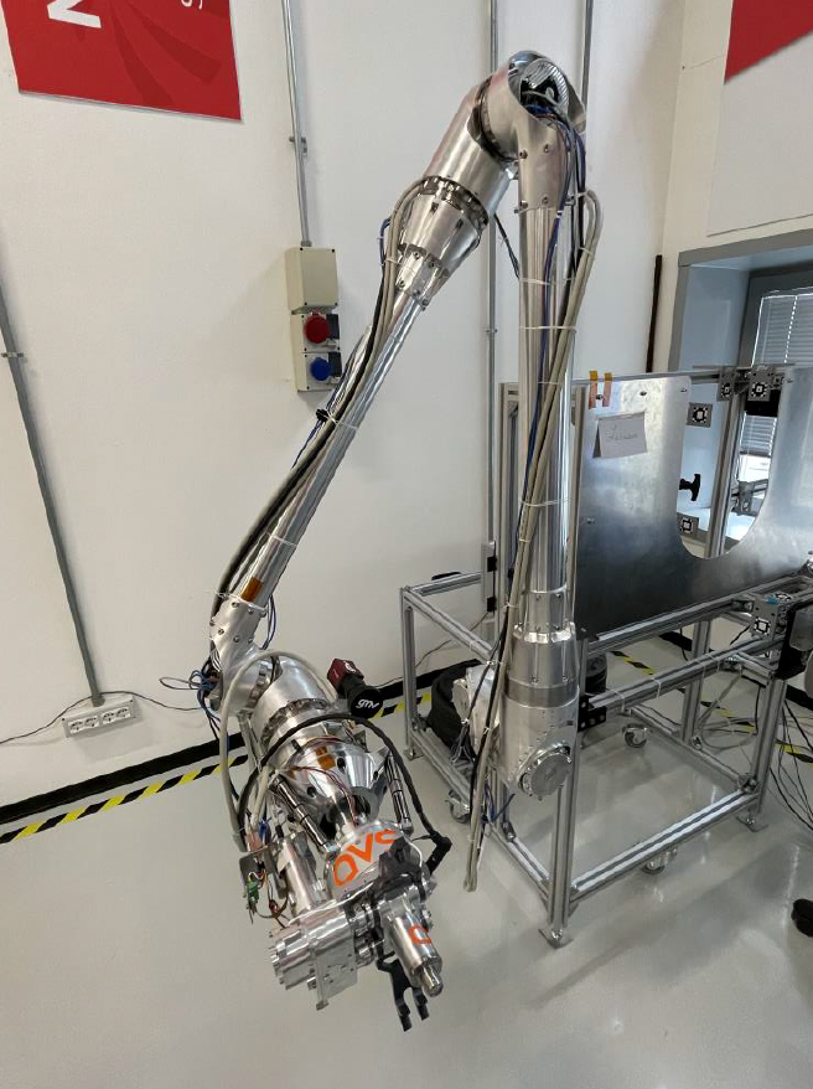
Sample Transfer Arm during testing at Leonardo Space facilities. Credits: Leonardo/AVS/Maxon Motors/OHB-I.
This mechanical device responds to a fundamental need in robotics, particularly in the context of manipulators such as Europe’s robotic arm. The technical-sounding mechanism connects the last joint of the arm with the end-effector, or ‘hand’.
The robotic arm must be able to insert the sample tubes into small rigid sheaths very precisely and without exerting excessive forces – all autonomously.
Stress-free insertion
The remote centre of compliance refers to the point where the robot can exert force while allowing for some degree of movement in other directions. This is particularly important when the robot needs to interact with surfaces or objects while avoiding excessive force, which could damage the objects or the robotic arm itself.
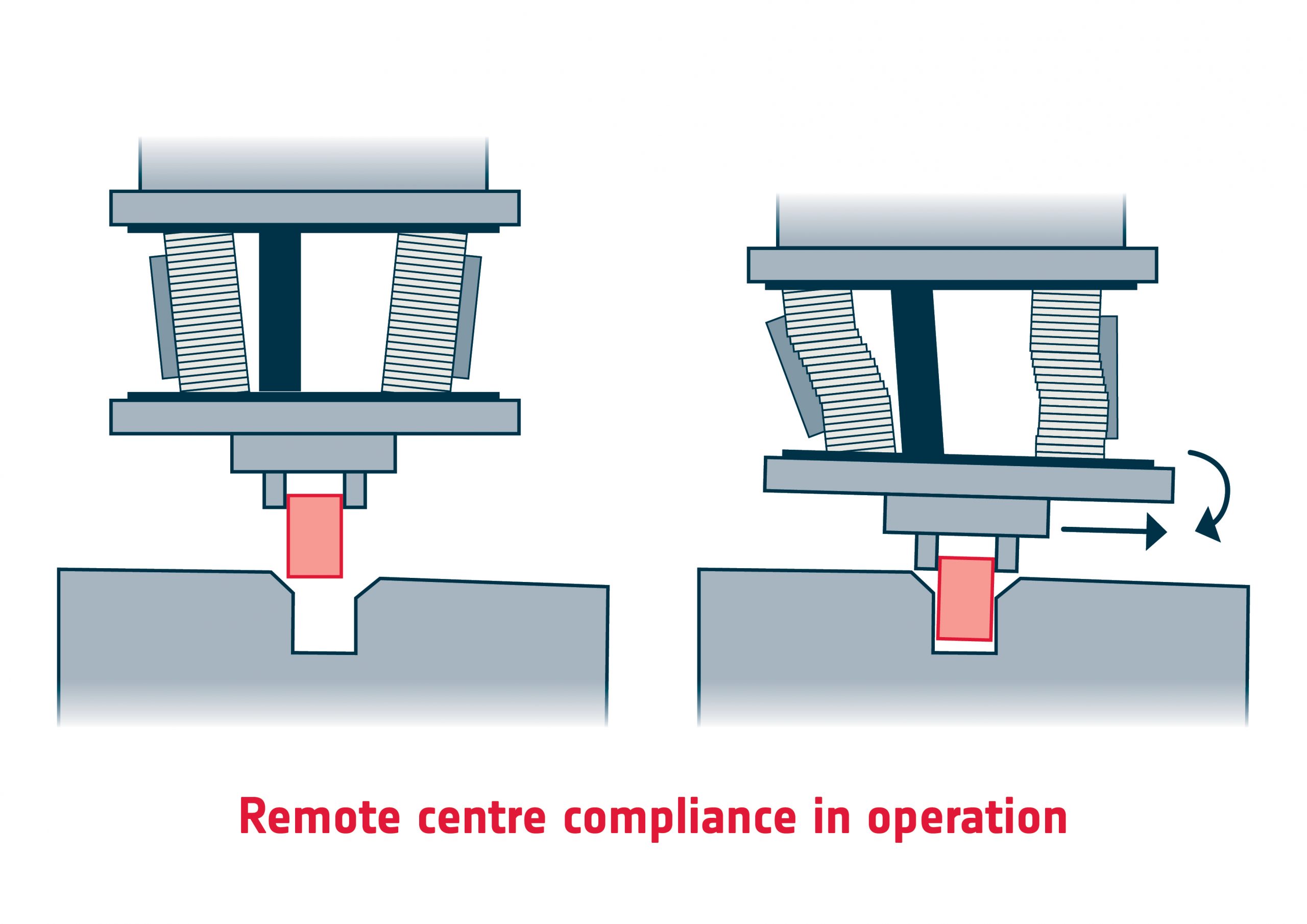
Conceptual drawing of remote centre of compliance operations. Credits: ESA/Arne Nordmann (CC BY-SA 3.0)
If the gripper of the Sample Transfer Arm is slightly off-target during the pick-up of the sample tube, it might experience unwanted lateral forces and rotations that further misalign the insertion, cause more rotation and result in a jam.
“If the arm were to execute complex motions and forces outside the allowed range, it could risk damaging itself, the tubes and, in the absolute worst-case, lead to the loss of the mission,” explains Davide.
The drastic temperature changes throughout the martian night could cause the expansion and contraction of the materials, leading to greater forces during operations. Thanks to this mechanism, the ‘hand’ of the robotic arm could adjust its position and ensure that forces and torques are kept within an acceptable range without risk of damage, particularly when the manipulator is in contact with NASA’s Perseverance rover or the Sample Retrieval Lander.
Stiffness to launch, testing times
The mechanism has another function up its sleeve. When the robotic arm is readied for launch, the mechanism will have the additional task of stiffening the assembly. A locking device at its centre will enable the arm to be stiff enough during the rough launch and landing events, avoiding the transfer of high mechanical loads to the delicate hardware attached to it, such as the gripper and the torque sensor.
The Italian aerospace company Leonardo designs, manufactures, integrates and tests the Remote Centre of Compliance Mechanism. European teams are working on the engineering models and have started manufacturing several units for further testing individually and as a whole system under conditions that are highly representative of the real mission.
Discussion: no comments