On console at the European Service Module mission evaluation room, the thermal team has their fingers on all the components that make up the Orion Moon spacecraft, keeping it cool or heating things up as needed. We talked to Arianegroup’s Thomas Guerreiro-Mancinho and Thales Alenia Space’s Lorenzo Andrioli. Here’s how they flew Orion for Artemis I:
The main goal of the thermal team is to keep each component operating at the right temperature. To do this well you need to know the temperature of the component, as well as its minimum and maximum limits and the preferred operating temperature. Here thermal has their work cut out for them as there are several hundreds of temperature sensors (thermistors) dotted around the Orion spacecraft, all sending back their data to be processed.
Almost all the hardware on Orion has a temperature sensor, aside from the frame structure. Think engines, valves, the solar array drive mechanisms, the pressure chain, propellant tanks and the consumable storage systems. Cross-referenced to the specifications of each component, the thermal team must keep each item within operating temperatures.
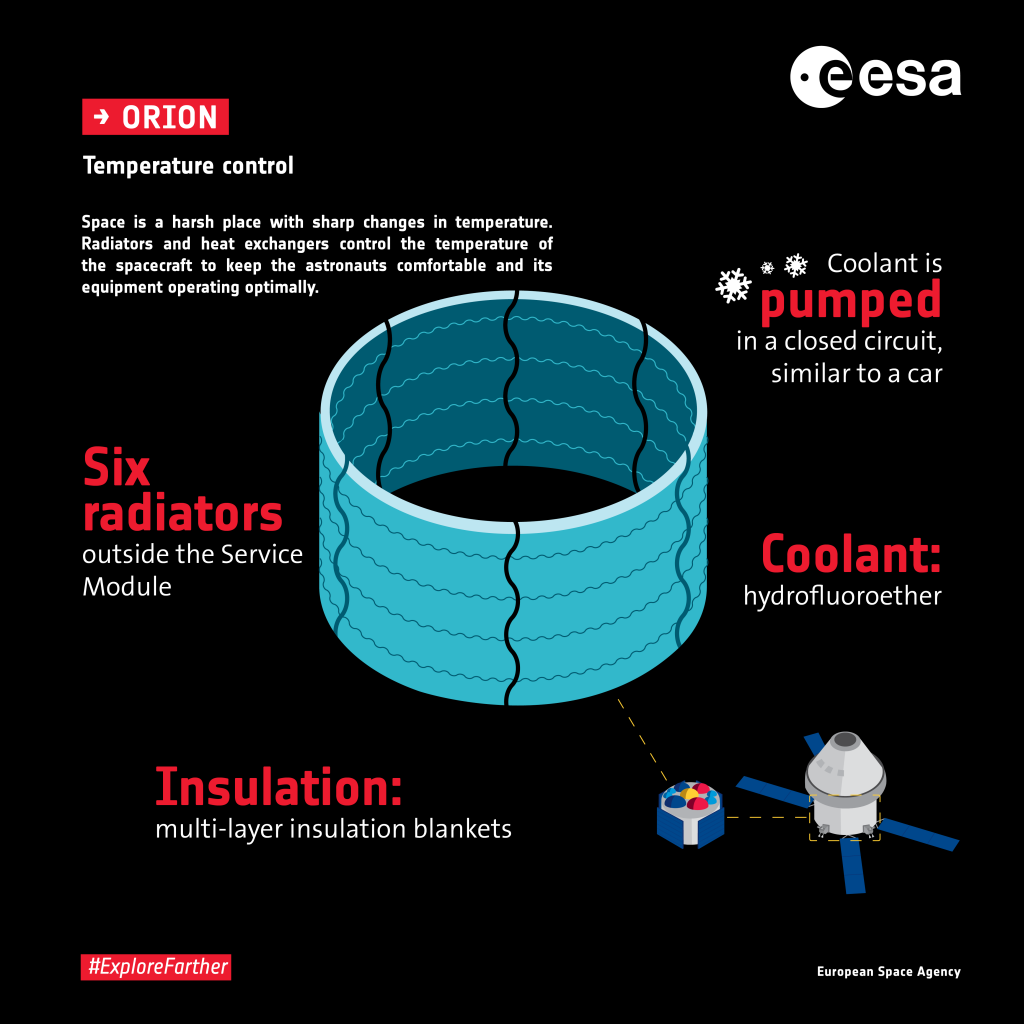
Keeping the cool
There are three ways to keep things cool or heat them up. But first we must mention Orion’s temperature brain: there are two Thermal Control Units that have a very descriptive name. These computers work in unison and are each other’s backup to control the temperatures, like an advanced thermostat as you have at home.
The Thermal Control Units control the heater lines that work on the same principle as an electric oven, or a toaster: pass electrical current through a wire and through the magic of electrical resistance the wire will start to warm up. The heater wires on the European Service Module are made of copper and the wires are glued to each component – reaching throughout the module’s internals like a vast network of nerves to bring the heat where it is needed.
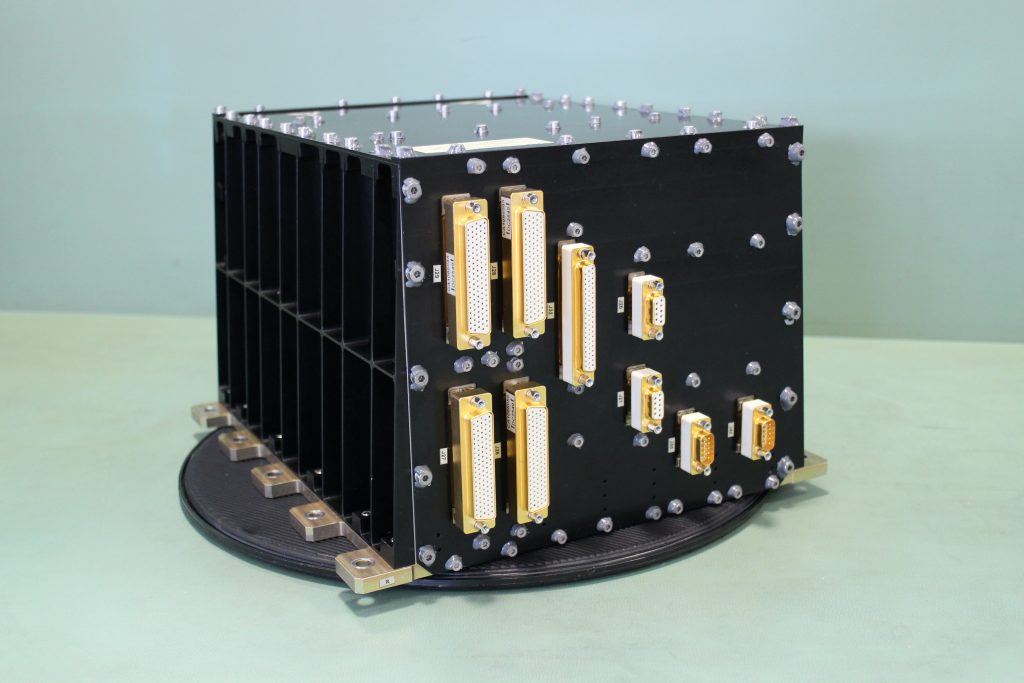
Sometimes you need to cool things down though, and this is where the coolant loops come in. They pump liquid past computers and around the European Service Module’s exterior. Whisking away heat from the electronics and then, by letting the liquid flow through the radiators to the coldness of space, the system cools things down in a closed, never-ending circuit, much like a liquid-cooled gaming pc or the coolant system in a combustion-engine car.
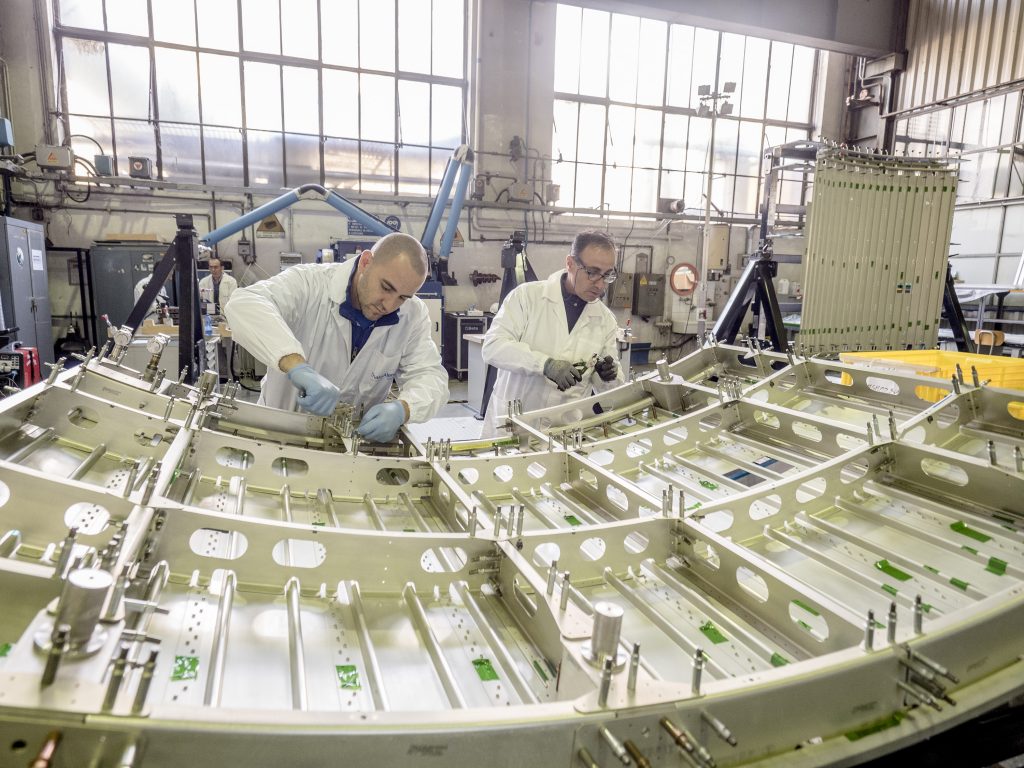
Lastly, to help the processes above, the European Service Module is insulated using multiple-layer insulation blankets or other materials and much thought was put into the design and layout of the module. Components that heat up are isolated from each other or placed near components that cool down, to even out thermal differences out as much as possible.
“Space inside the European Service Module is really tight, when you see the European Service Modules during integration you can really see how much thought has gone into each component and where it is placed,” says Thomas. “We are really efficient” adds Lorenzo.
In human spaceflight where lives are at stake safety is paramount so each component has a backup and often the backups have backups too. Each heater and thermal control unit has a backup, but there are also stand-alone systems in the Orion crew capsule to be used for reentry operations from separation with the European Service Module to crew capsule splashdown.
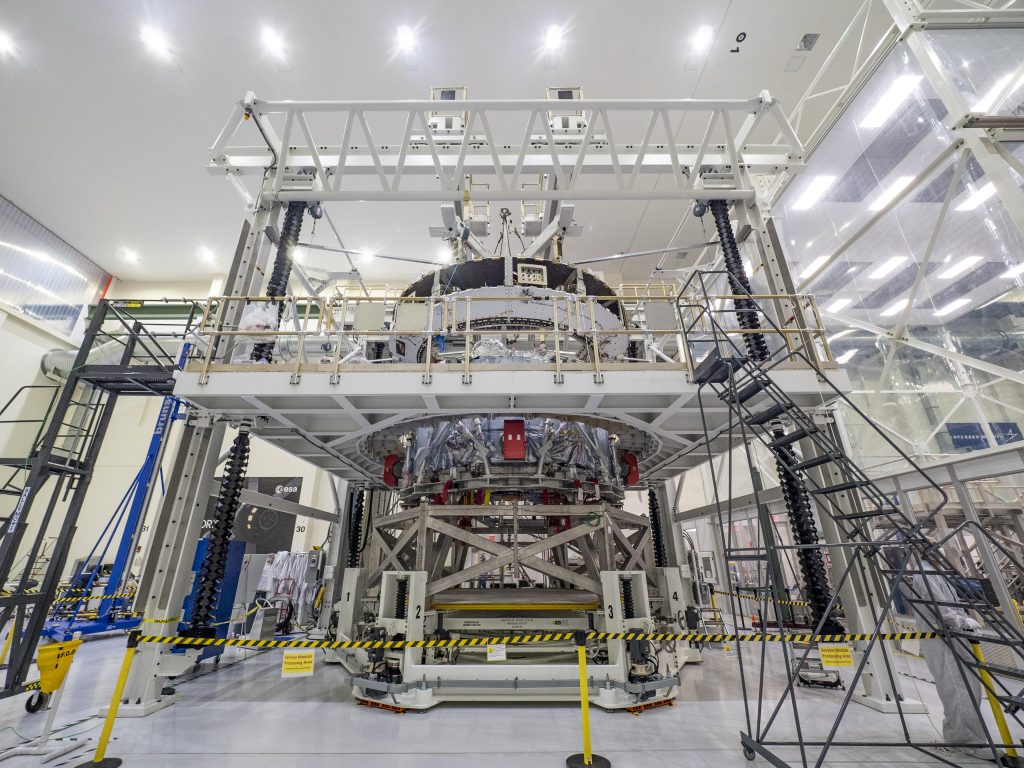
Go with the flow
With the knowledge of how warm the European Service Module’s components are and how to heat or cool them, the last piece of the puzzle is maintaining a nice temperature.
“We are involved in all the spaceflight disciplines as we have to monitor them all, keeping an overview of all the components.” says Thomas.
Each component in the European Service Module has its own inertia, some things change temperature quickly and some things take longer to heat up or cool, the several tons propellant tanks keep their temperature much better than an engine thruster that heats up very quickly when firing for example. The inertia has been characterised thanks to simulations and extensive test campaigns at NASA’s Plum Brook station in Ohio, USA, where Orion spent six weeks in a thermal-vacuum chamber so engineers could record how the spacecraft absorbs and radiates heat in spacelike conditions.
Lorenzo says, “We are used to know how things work on Earth, but nevertheless, in space everything is different because of the microgravity environment and the dynamics of the mission.”
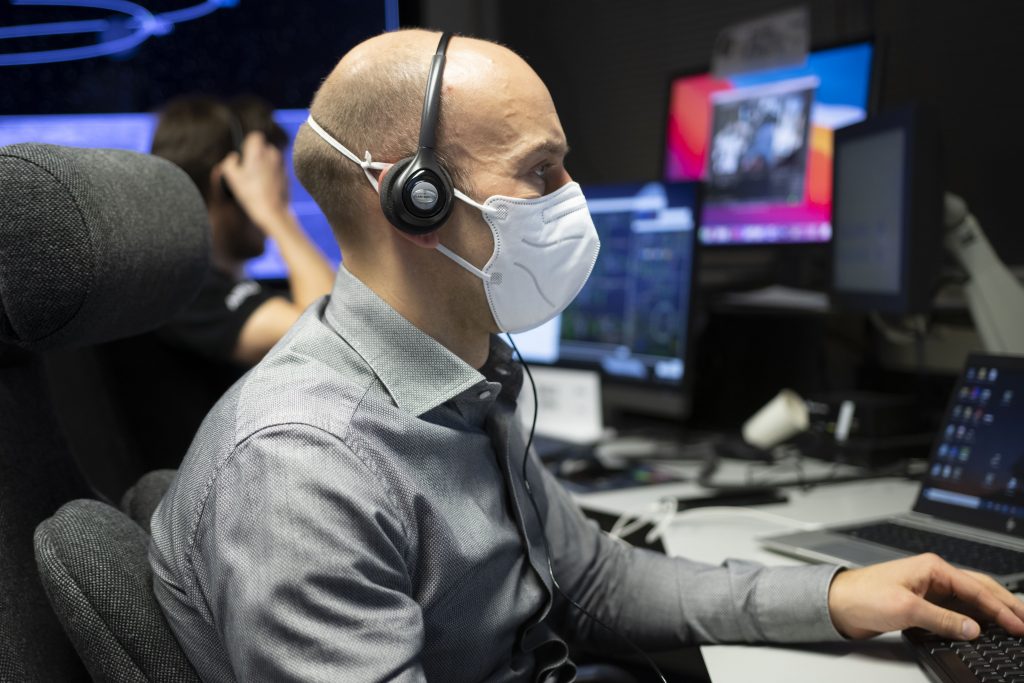
Keeping equilibrium
“Every single watt of energy added to the system has repercussions and we need to consider how we will expel the excess heat before operating hardware,’ says Thomas, “the heat equilibrium of the spacecraft is very delicate as we balance between the heat of the Sun versus the coldness of space.”
“Having no air radically changes how the heat is rejected, and when Orion flew behind the Moon and was out of sunlight we saw a marked drop in temperatures on the systems – as predicted of course,” continues Thomas, “in general we try to avoid losing heat as it takes energy to heat everything up.”
Lorenzo adds “Flying behind the Moon we have to trust the design and the spacecraft, but we felt very much in the hot-seat as we knew Orion was flying through the cold shadow of the Moon.”
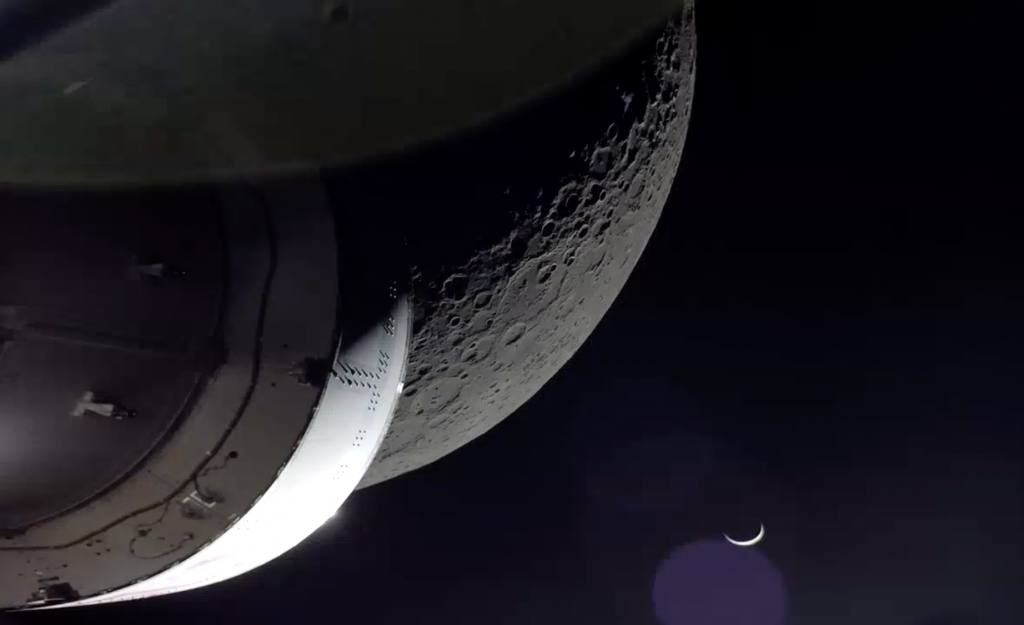
Thomas adds: “We designed the European Service Module, and provide the manual for the spacecraft, and then NASA uses it integrated with the Orion. We are kept on standby for the intricate knowledge we have of the hardware, monitoring what is going on and ready to react in case of troubles or to validate some specific operations. Nobody knows European Service Module like us at the mission evaluation room.”
The Artemis missions are special for spaceflight engineers, “As engineers we are lucky to have the livestream and high-quality photos, as they are rare, most satellites don’t take selfies,” says Lorenzo “To see those images of Orion flying by the Moon and to think you have touched those components is a very special feeling.”
Propulsion peculiarities
The propulsion system is a special case for thermal, it has tight tolerances for operation and — obviously — creates a lot of heat. But before the fire starts, the propellant flows from the tanks to the engines, passing through multiple valves and through pipes… and the propellant itself acts as a coolant.
Before a thruster burn, some heaters might be turned on to pre-heat the engines but after firing the temperatures they rise by tens of degrees.
“Propulsion is… complicated, there’s a reason the saying ‘it’s rocket science’ exists,” says Lorenzo. The thermal team also monitors the cooling effect of the propellant as it is sent from the tanks to the engines.
From the beginning to the end and on to more voyages
Flying a new spacecraft on the Artemis I mission is a rare and exciting experience. Thomas recounts: “It was a bit like watching a football penalty shootout, so nervous! The first days were so intense that after a shift we just crawled to bed where we were staying near ESTEC. But the next day we couldn’t wait to get back on console!”
Thomas ends: “We spent many years designing the vehicle and it has flown like a charm. All the companies and nationalities working on the machine worked in harmony, and after all these years we are no longer colleagues, but friends.”
Lorenzo concludes: “The European Service Module was destroyed – as by our design – on reentry, but we know it has done a good job. This is not the end but the start of the journey.”
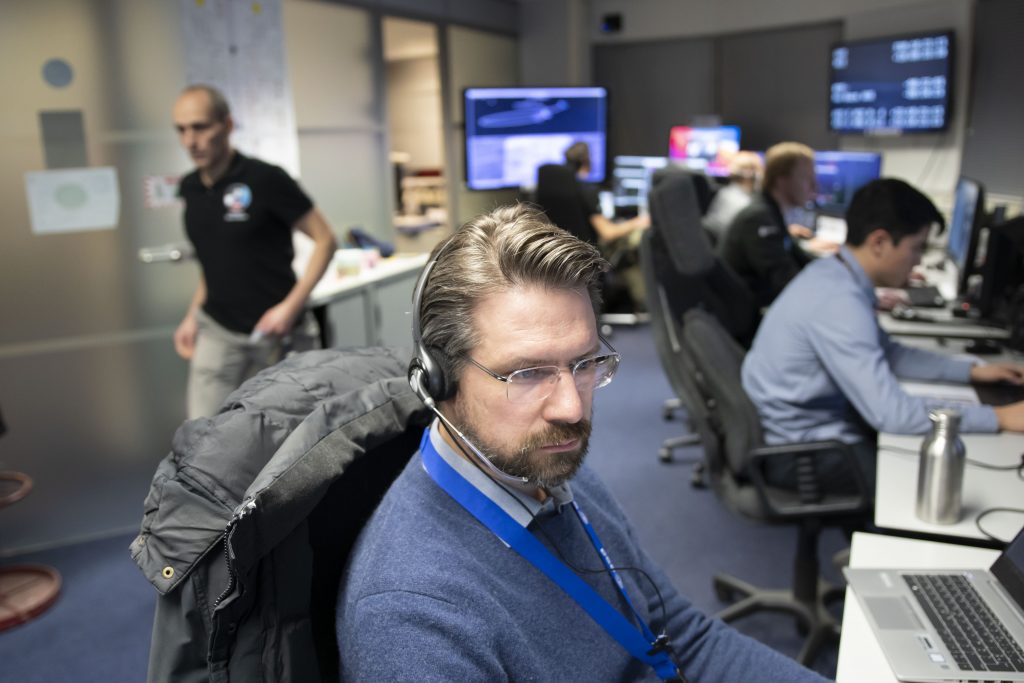
Discussion: no comments