In this series of blog posts we will look at each operator of subsystems of the European Service Module for Orion, talking to the people that are on console during a mission who know the lunar spacecraft better than anybody.
In this entry of how to fly the Orion spacecraft with European Service Modules we look at propulsion. Propulsion is a three-syllable word for firing engines to make something move and so it is maybe unsurprising that the European Service Module propulsion engineer that monitors flight, considers it the “most complex and biggest” task of them all.
Tobias Langener, the ESM Propulsion lead says: “Being on console for propulsion is as close as you can get to flying a spacecraft without being an astronaut, and even if we don’t say it literally, but just send the command, we obviously think it’s the coolest part of the whole of Orion.
“Once the engines are burning, I am imagining the acceleration the astronauts will experience, it’s probably going to be like in sitting in a drag racer.”
Tanks
There are four propellant tanks, two with fuel and two with oxidiser that when mixed explode for a controlled expel out of the European Service Module’s 33 thrusters, controlling its attitude, correcting its path, and propelling it into a lunar orbit, or back to Earth of course. All the thrusters do not fire at the same time, and so this is where the Propulsion console comes in.
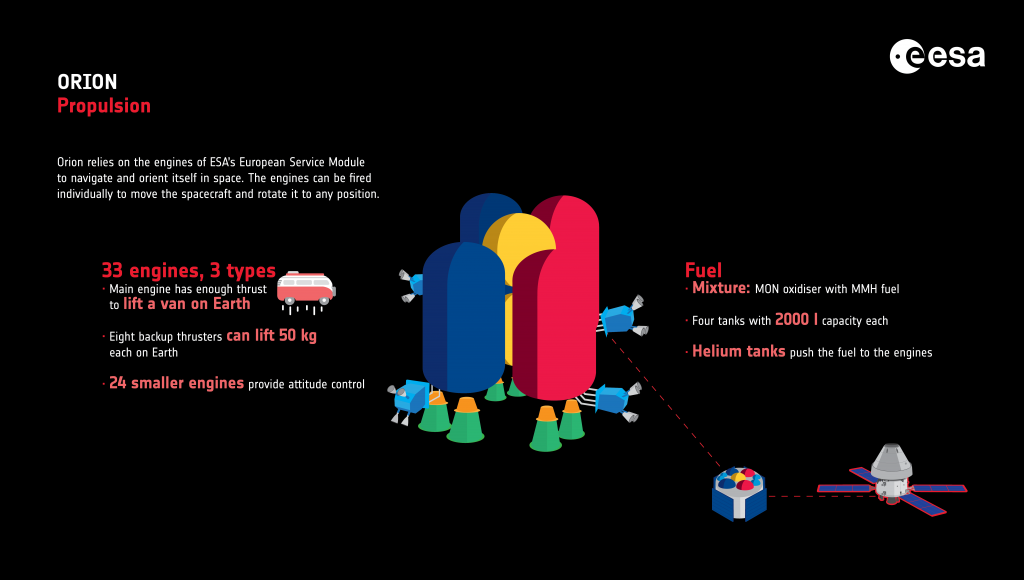
In space nothing is easy, so to mix the fuel and oxidiser two more tanks are required that have not been mentioned: filled with helium, this gas pushes the propellant out of the propellant tank to the various thrusters to ignite – there is no gravity or air pressure that would mix fuel and air like on Earth.
Valves and more valves
As propellant can go bang by design, the engine system for the European Service Module is intricate and has multiple fail-safes. There are three valves that control the flow of fuel to each engine, and there are 33 engines, each valve being monitored on Earth by the personnel on propulsion – that is a lot of valves!
It is all about pressure and temperature for the propulsion engineer on console. Each segment between all the valves and all thrusters are monitored. Does the pressure increase or drop? Is the temperature okay in the cold space or after a hot thruster firing? Are the valves open or closed? How much fuel is left in the tanks? Is sufficient pressure left to push propellants out? All these are constant considerations for propulsion.
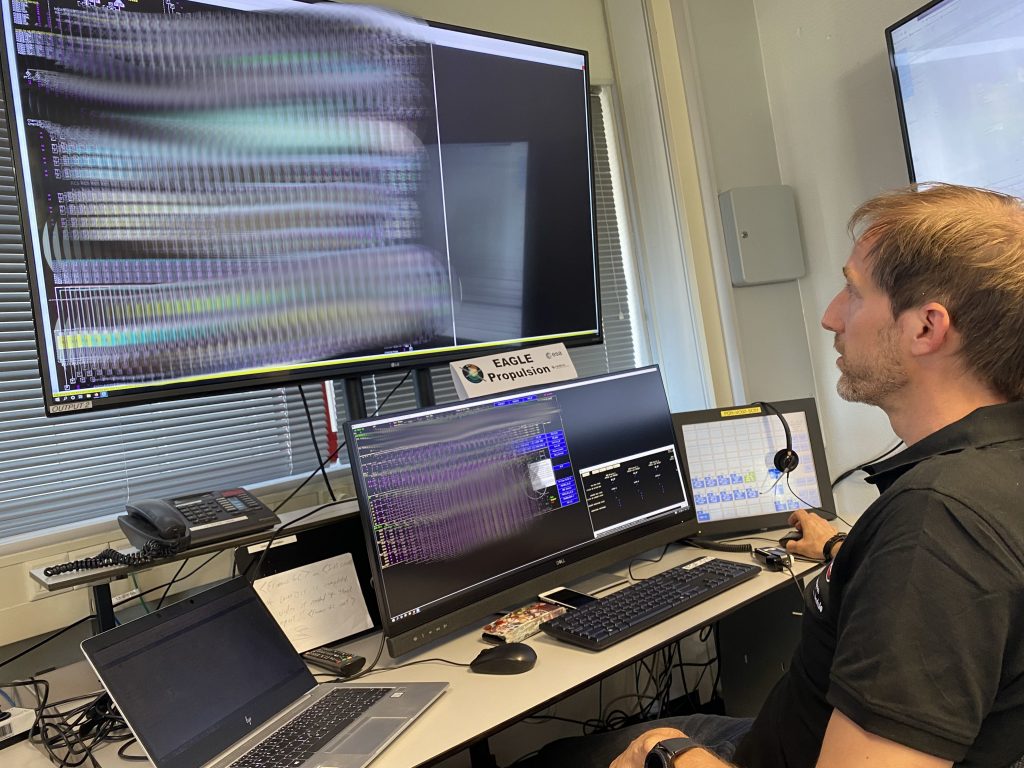
Bang bang, never underestimate the boring
The European Service Module uses a so-called bang-bang pressure regulations system. The helium tanks provide the push to get the fuel where it needs to be, but they are constantly oscillating between extremes, from too much to too little. By quickly opening and closing the valves – with full tanks, it is only for milliseconds – and thus regulating the flow the European Service Module can ensure the correct level of pressure allowed for each of its three types of engines, from the 24 small Reaction Control System (RCS) thrusters used for controlling the Spacecraft’s orientation in space, to the single main engine (OMS-E) giving the big push, which flew already on NASA’s Space Shuttle.
Jan-Hendrik Meiss, one of the European Service Module Propulsion engineers working for Airbus, tells “we never underestimate the boring, boring is fine, we hope to be bored that means that everything is going as planned!”
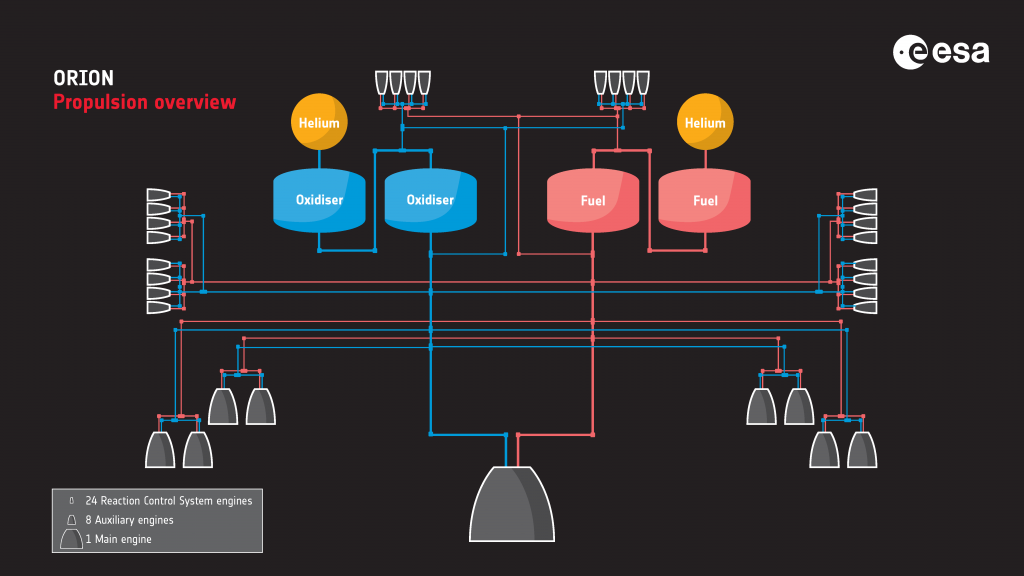
This simplified representation of the propulsion screen shows how intricate the system is. Centre and large are the four tanks with the oxidiser MON and the fuel MMH. The Reaction Control System (RCS) thrusters are positioned on the actual display on the right and left in their pods of four. At the bottom of the screen are the “AUX” Rocketdyne engines to the left and right and in the centre is the large OMS-E engine. The helium tanks are located further on top of the display.
“We are constantly monitoring three things: pressure, temperature and whether a valve is open or closed”
Things start to get more complicated when you consider that the pressure at the source will be different from the end of the lines, “different downstream values” need to be taken into account. As the Artemis mission progresses pressure levels will fall, from a fully loaded helium tank to running on empty and this too has to be taken into account as well as the fact that helium gets pretty cold when it expands into the propellant tanks, similar to the ice sprays used by sports professionals when they hurt themselves.
An “O” on the console screen indicates “open” and refers to an individual valve. The thrusters are isolated and the three-valve system ensures that each thruster or a subset of thrusters is independent and can operate on its own if ever one would fail.
Tit for tat
But we are not finished. The console screen for propulsion is set up to show the same information above in a more condensed form. It shows the “TAT” or Thruster Availability Table. In spaceflight it is not as simple as firing up a thruster on command. Each thruster needs to be available, depending on where it is in space, heaters need to be turned on to warm the thruster, and the temperature outside decides how long the heaters need to warm, somewhat like starting up a diesel engine in the cold.
Discussion: 8 comments
During Artemis 2, will the crew be in charge, for the whole thing? I mean I guess they will get advice from earth when they have to initiate/terminate xtra burns, but the control of the pressure in the system will still be a job for the propulsion engineers on earth.
If the crew is in charge of propulsion at one point, will that be after the separation with the 2nd stage?
Most of the burns are sequenced, so if everything goes well, there is little need for crew interaction. A few propulsion functions are automatic regardless of manual control, such as attitude and pressure control for the propellant.
Thanks. Will there be a phase, during Artemis 2, where the crew will try if they can interact with the ESM properly (so they know how it goes, if it’s needed and the actually need to take over, in case of emmergency)?
Thanks
Artemis II has a proximity demonstration phase that is planned to have the astronauts take control of Orion. The spacecraft is designed as fly-by-wire though, like modern aircraft there will always be computers translating commands to the engines. See the freshly published Artemis II mission overview: https://www.youtube.com/watch?v=tt0qV-qFIG8
Absolutely, before departing Earth orbit to the Moon, the mission plan will see Orion give a full demonstration of the European Service Module’s thrusters in a proximity operations demonstration sequence. The demonstration of the spacecraft’s capabilities involved separating from the Interim Cryogenic Propulsion Stage, rotating to face the cryogenic stage, flying back towards it and then departing again. The operations will also use and test a docking camera, a new addition to the spacecraft since the Artemis I mission. More here: https://www.esa.int/Science_Exploration/Human_and_Robotic_Exploration/Orion/Artemis_II
Thanks! I feel I come back to my childhood, when I was lying on the floor close to our TV, awaiting for Ariane to launch and dreaming of the future….
Thank you very much to your team for this excellent blog!
How may kg of MON and MMH is used when one of the reaction control system thrusters is fired? Half a kg? Less? I ask because I wonder how much the astronauts can maneuver Orion during a mission.
Each of the 24 Reaction Control System (RCS) thrusters on our European Service Module (ESM) consumes 78 grams per second of the propellant, a blend of mixed oxides of nitrogen (MON) as an oxidiser and monomethyl hydrazine (MMH) as fuel. These thrusters are primarily used for attitude control, requiring only brief thrust pulses and minimal propellant; for bigger manoeuvres the larger auxiliary engines, or even the main engine, are used. The ESM carries enough propellant to support the Orion spacecraft’s attitude control for all planned Artemis missions.