With a background in mechanical engineering, Swiss trainee Timon Schild manages projects within the Spaceship EAC team at ESA’s European Astronaut Centre in Cologne, Germany. Here, young researchers are investigating additive manufacturing and the use of microwaves for in-situ resource utilisation (ISRU).
ISRU involves using local resources to avoid transporting materials from Earth and lunar regolith, or Moon dust, is showing strong potential for construction far from home.
From kitchen utensil to space tool
But why microwaves and what can be made from lunar dust?
Microwave radiation is a fast and efficient way to heat regolith to sintering or even melting temperatures, explains Timon. This enables the sand-like material to bind together and solidify for use in building things like habitats, landing pads or mechanical parts directly on the lunar surface.
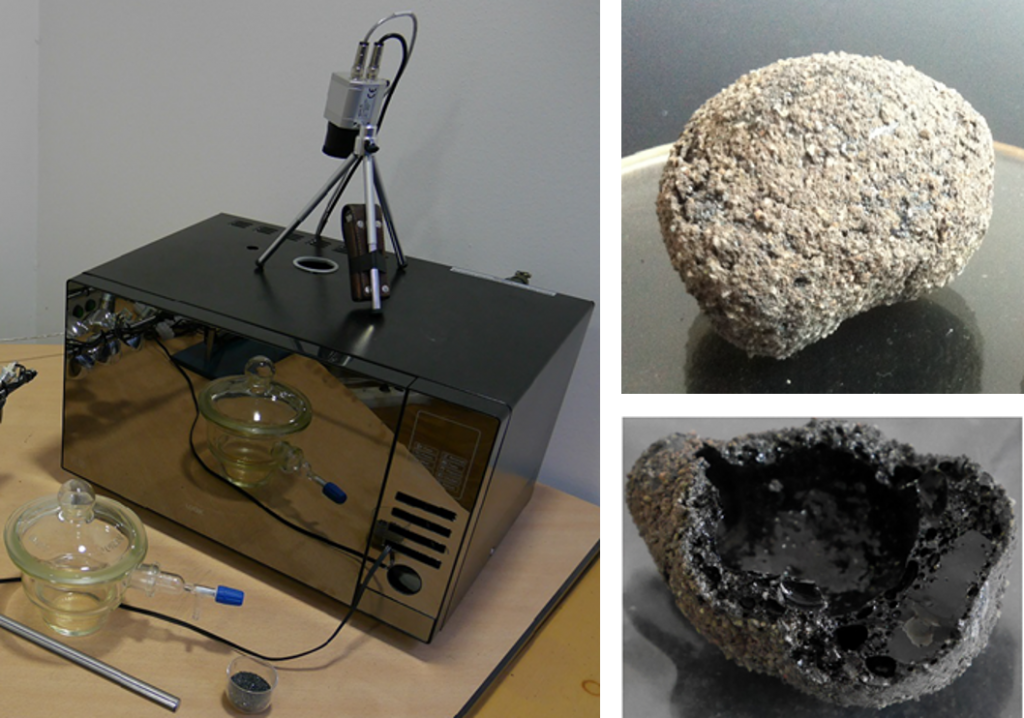
Modified kitchen microwave to heat up regolith simultant DNA-1 (left) and result of regolith simulant DNA-1 melted in modified microwave oven (right). ESA-T. Schild.
Heating regolith in a vacuum environment can also be used to produce oxygen, by decomposing oxides through vapour phase pyrolysis. This could be helpful in lunar life-support systems or to refuel rockets.
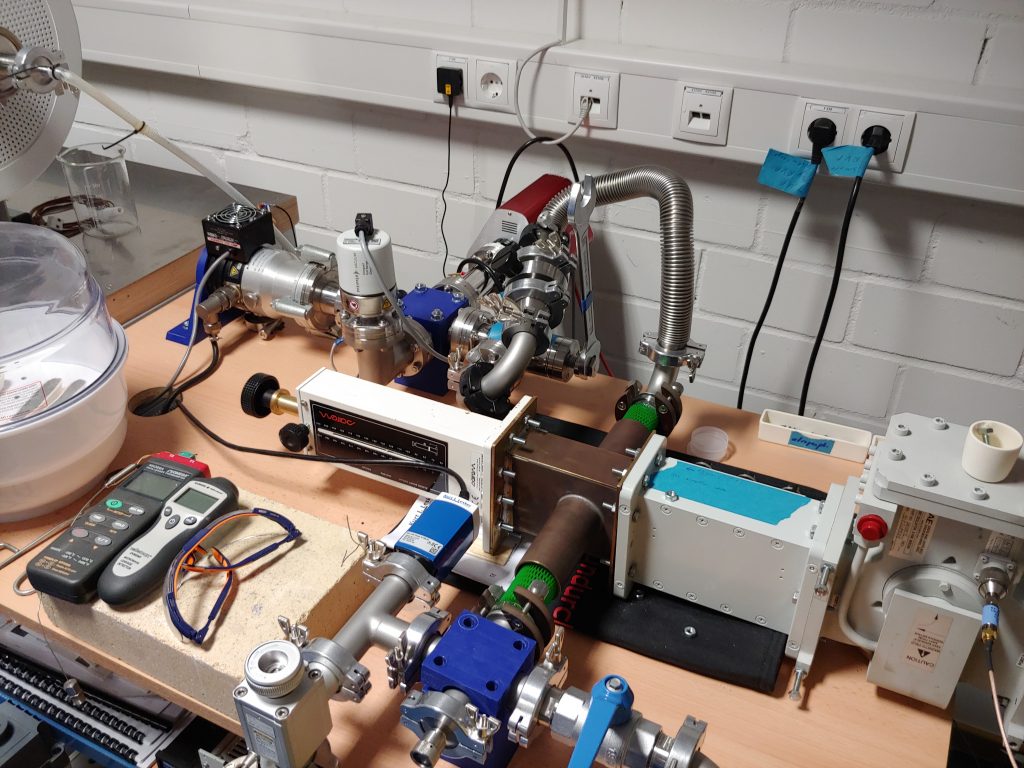
Semi-open microwave cavity system for heating of EAC-1 lunar regolith simulant under vacuum conditions. ESA-T. Schild
“One approach we’re investigating uses a semi-open microwave cavity system, like a microwave oven in a kitchen, where microwaves bounce around a closed cavity and heat up the material inside,” says Timon. “This allows us to understand the bulk heating behaviour of our regolith simulant EAC-1 under microwave radiation and demonstrate oxygen production by microwave heating under vacuum conditions.”
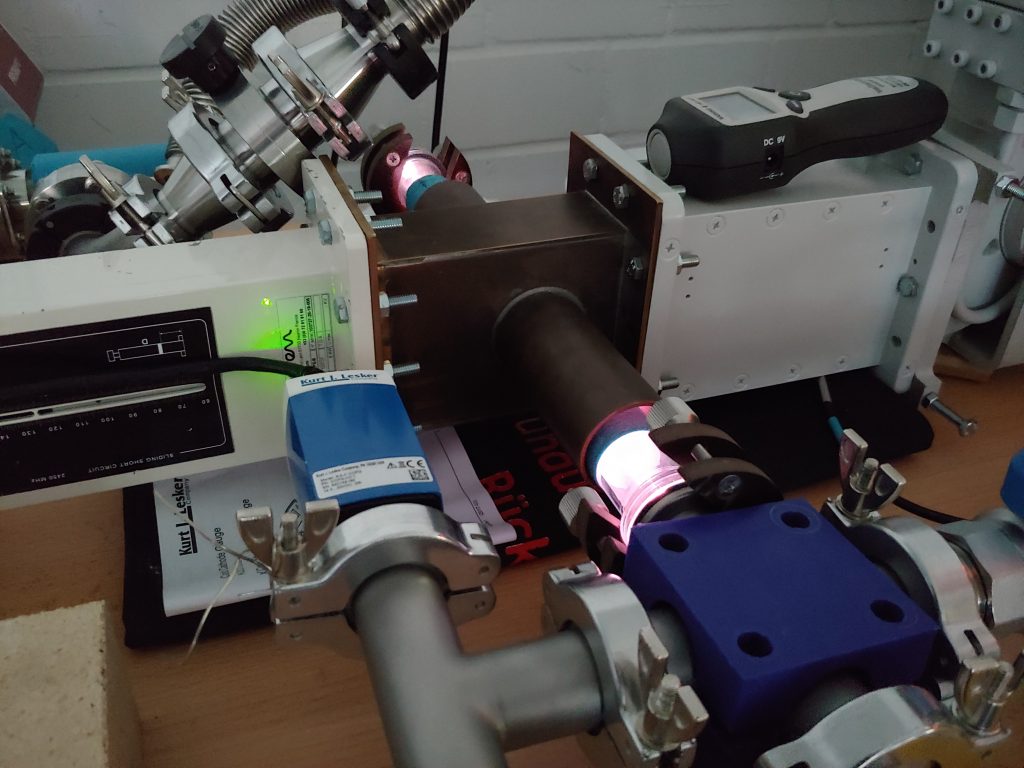
Plasma formation during microwave cavity heating of EAC-1 regolith simulant under vacuum conditions. ESA-T. Schild
To make this method more precise for space, Timon is now working on a direct microwave application system to heat regolith on the lunar surface. Using an antenna-like applicator, the system applies microwaves to a bed of regolith simulant for localised sintering and melting of the material.
“This is a first step towards applications such as 3D printing, which would allow astronauts to build structures on the lunar surface, using only regolith as feedstock,” he explains.
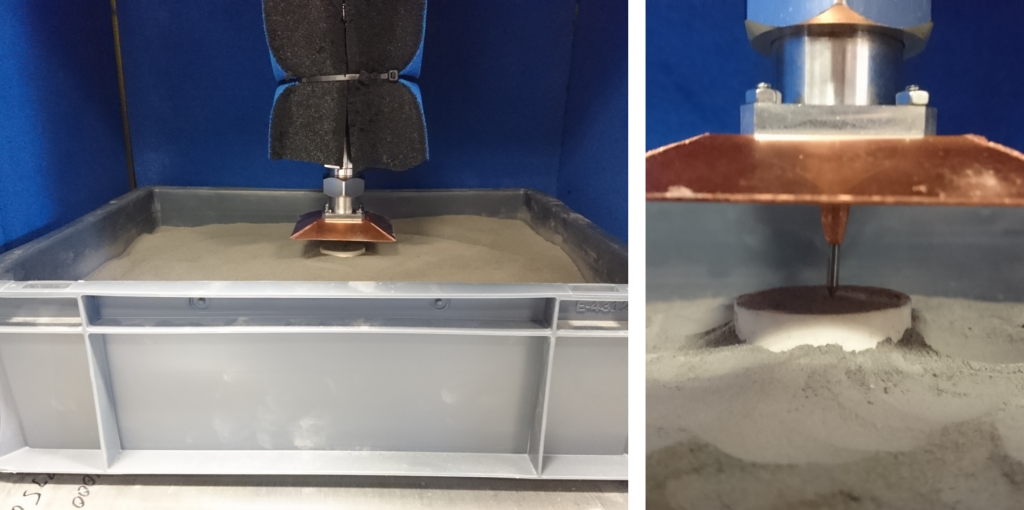
Direct microwave application system using an antenna-like applicator for localised sintering and melting of regolith on the lunar surface. ESA-T. Schild
To prevent any risks from the antennas radiating microwaves at high power, Timon also developed a faraday cage with microwave-absorbing walls. This acts as a shield to protect the operator from stray emissions while simulating the open environment of the Moon.
Microwaves as an integral element of ISRU technologies
The microwave cavity approach allowed the team to produce a continuous line of molten regolith for the first time, paving the way for 3D printing applications and the production of oxygen under vacuum conditions. The new localised application approach is already showing potential. Timon has been able to produce spots of molten regolith simulant and hopes he’ll soon be able to demonstrate the printing of a first line or 2D shape.
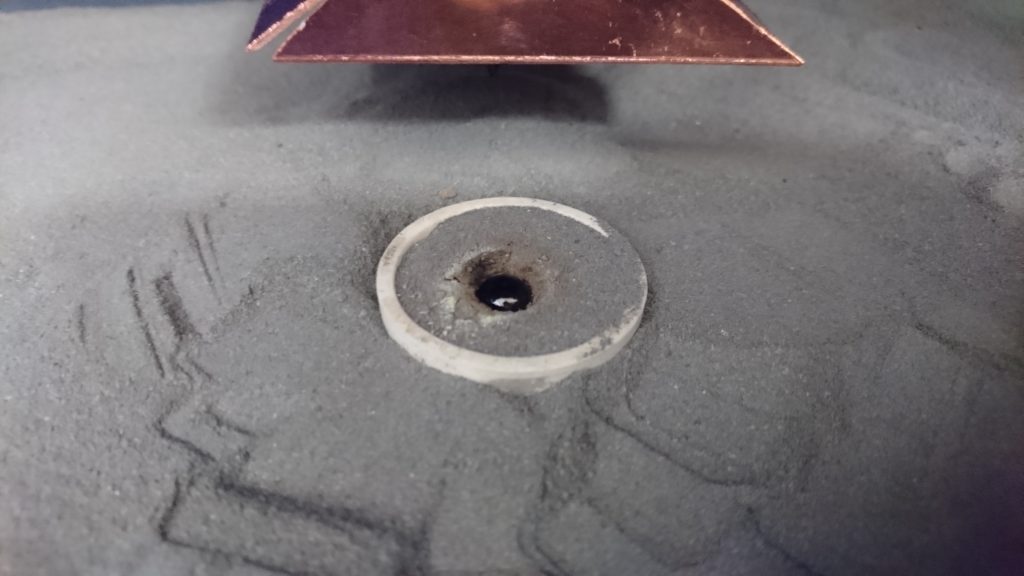
Spots of molten regolith simulant EAC-1 after application of local microwave radiation to a regolith simulant test bed. ESA-T. Schild
Looking ahead, microwave processing of regolith is seen as a promising technology for in-situ thermal processing of lunar regolith. Timon is confident that once this technology moves beyond its current low Technology Readiness Level (TRL) and technology demonstration stage, it will be part of the many technologies used for lunar ISRU to establish a long-term human presence on the Moon.
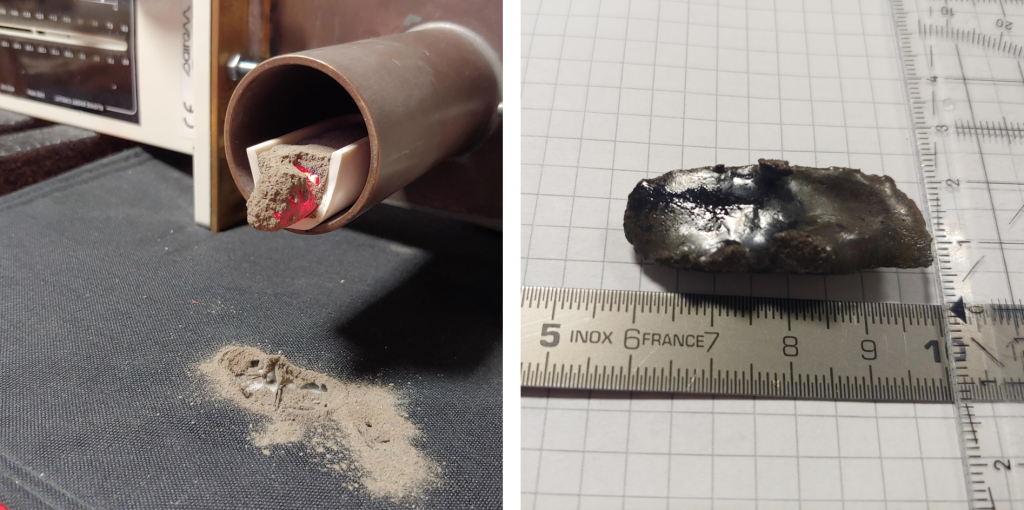
Line of molten regolith simulant just after microwave cavity heating (left) and solidified (right). ESA-T. Schild
“What inspires me a lot about this topic is how it could impact the future of crewed space exploration, while also revealing opportunities for more efficient and sustainable use of resources on Earth,” says Timon. “High-power microwave radiation could be used in the mining industry or for 3D printing ceramic parts on Earth. Regolith is basically a mineral, so the proposed 3D printing process could also be used with various ceramic powders on Earth”, he adds.
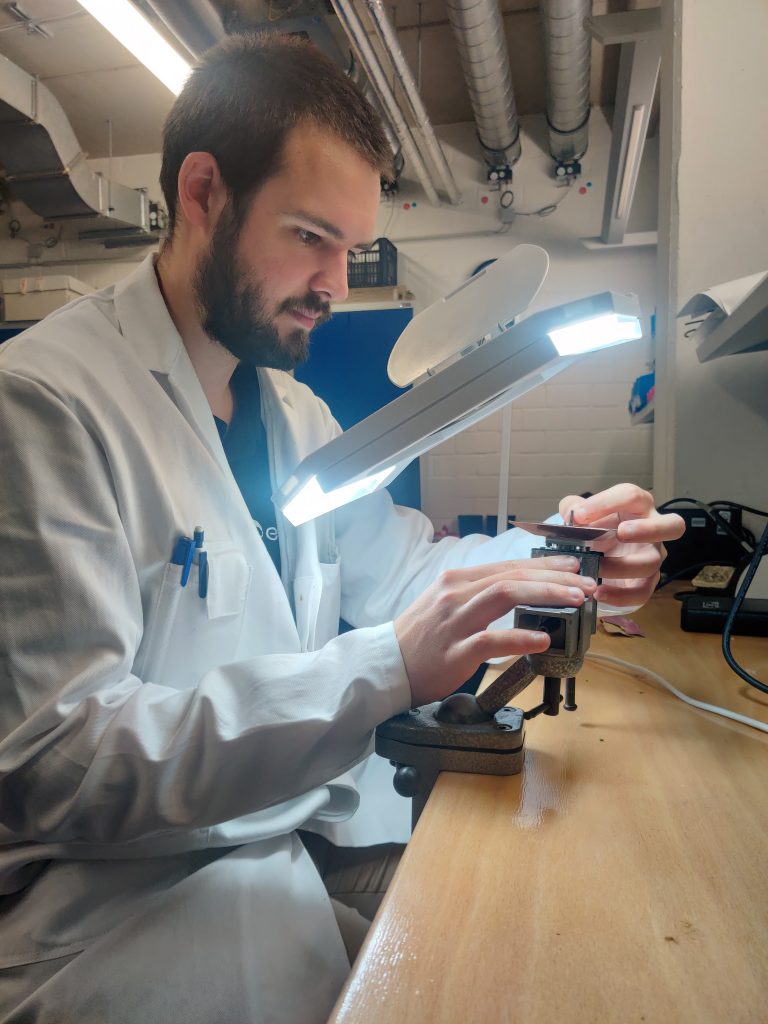
Spaceship EAC trainee Timon Schild working on the antenna for application of local microwave radiation to a regolith simulant test bed. ESA-E. Tuohy
“Working in the Spaceship EAC team is an amazing experience, with the opportunity to work with a team of very talented young professionals from all over Europe. We are given a lot of freedom to carry out our work, which allowed me to massively improve my project management and collaboration skills, which will be very helpful for my further work in this field, for example as part of a PhD.”
Learn more about the Spaceship EAC programme here
Meet more students and Spaceship EAC interns here