In-situ resource utilisation (ISRU) will be vital in establishing a sustainable human presence on the Moon, as it involves using local resources rather than having to transport all the supplies from Earth.
The challenge is to find circular solutions and reuse and recycle as much as possible of what is already available. This includes Moon dust, known as lunar regolith.
Aurélie is investigating how this dust could be used to 3D print parts directly on the lunar surface. If successful, the technology would enable astronauts to manufacture or repair custom-made objects or tools by themselves with little material waste and low energy consumption.
In her project, Aurélie uses a process called Fused Deposition Modelling (FDM). Here, an object is built by selectively depositing a melted thermoplastic filament through a temperature-controlled nozzle in a pre-determined path layer-by-layer.
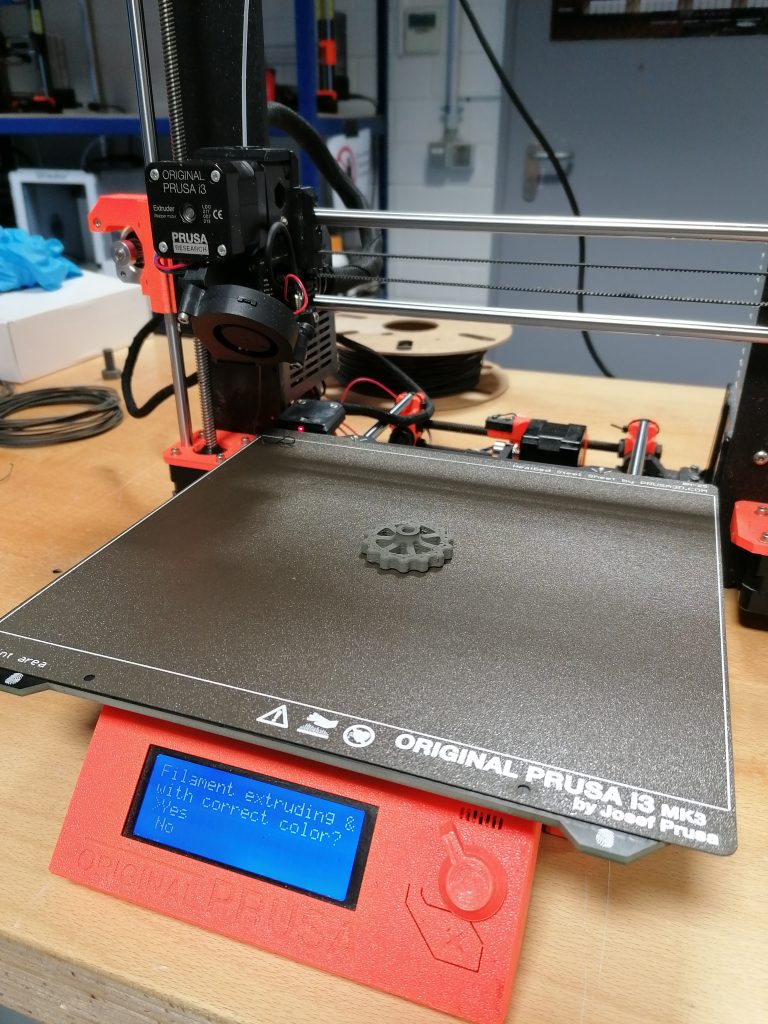
3D printed gear on the bed of FDM printer. ESA-A.Hand
While this method is already widely used in 3D printing on Earth, the combination of FDM printing with lunar resources, like regolith, for use in space is leading the way for researchers worldwide.
Prior to Aurélie’s project, former Spaceship EAC intern Benoît André created a composite material made of biodegradable PLA plastic (polylactic acid) and ESA’s homemade lunar regolith simulant EAC-1, allowing the production of highly concentrated filaments and 3D printed parts.
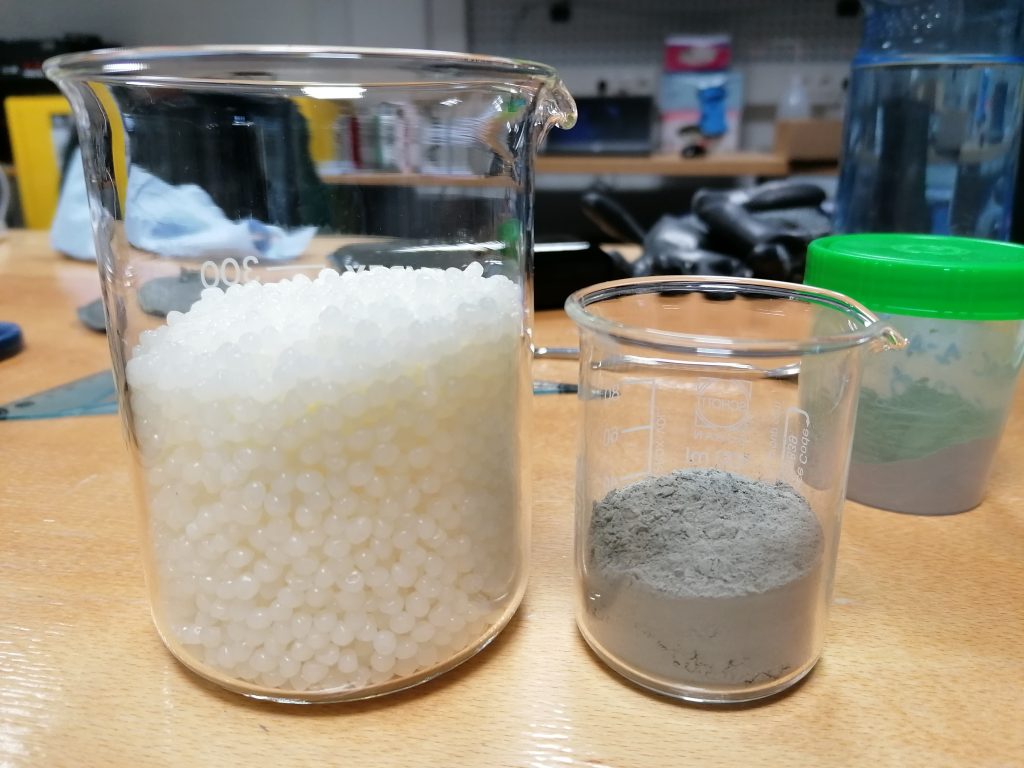
PLA pellets and lunar regolith simulant EAC-1. ESA-A.Hand
Aurélie’s goal is to optimise the manufacturing process and find a compromise between a simple manufacturing process with high printability, and one with good mechanical properties suitable for a range of applications on the lunar surface.
The long-term aim is to create sustainable manufacturing cycles using the highest possible concentration of regolith (currently up to 80% in tests at EAC) in the biodegradable plastic compound, enabling highly stable but also filigree constructions, as needed for missions on the Moon.
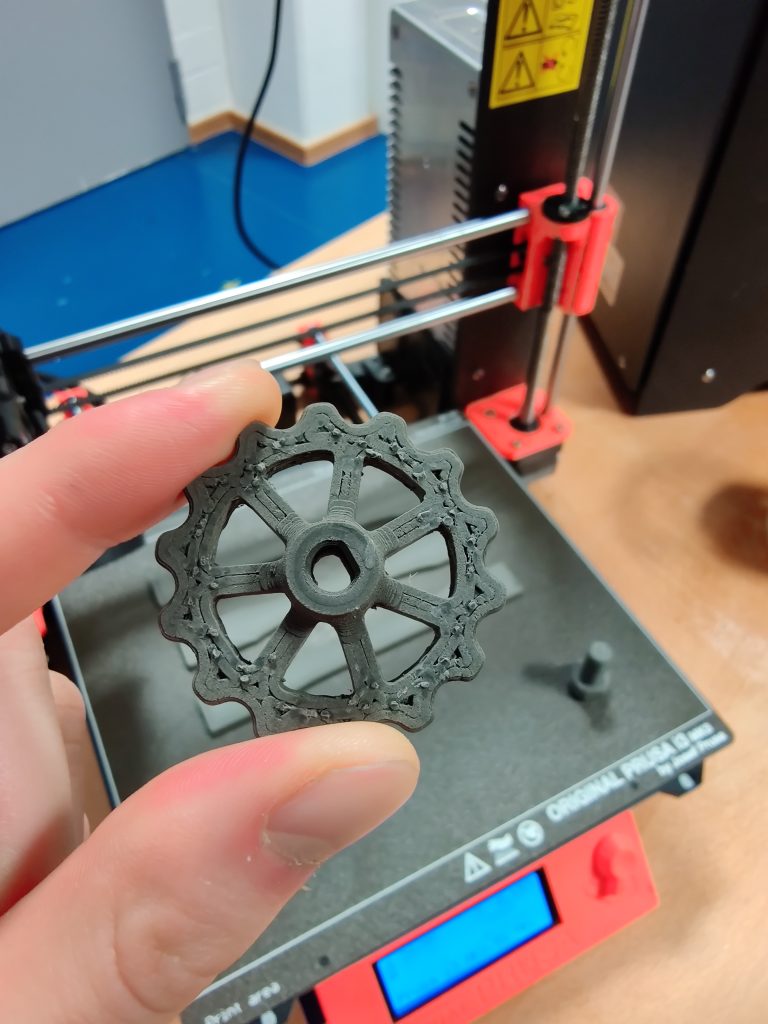
FDM printed gear made from 70% lunar regolith simulant EAC-1. ESA-A.Hand
Finding the right recipe for success
“I first tried sieving the EAC-1 to obtain finer regolith to increase concentration and to prevent the 3D printer nozzle from being clogged by larger grains during manufacturing,” Aurélie explains. “But at the same time, the parts were very brittle. To increase flexibility, I added additives such as liquid plasticisers.”
Aurélie is also experimenting with new plastic materials, different additives and the modelling process itself. For example, she created a slurry by dissolving the plastic in a solvent first and then adding the other components. Once this composite mixture dries, it is crushed into pellets suitable for the extruder to create the filament and enable 3D printing.
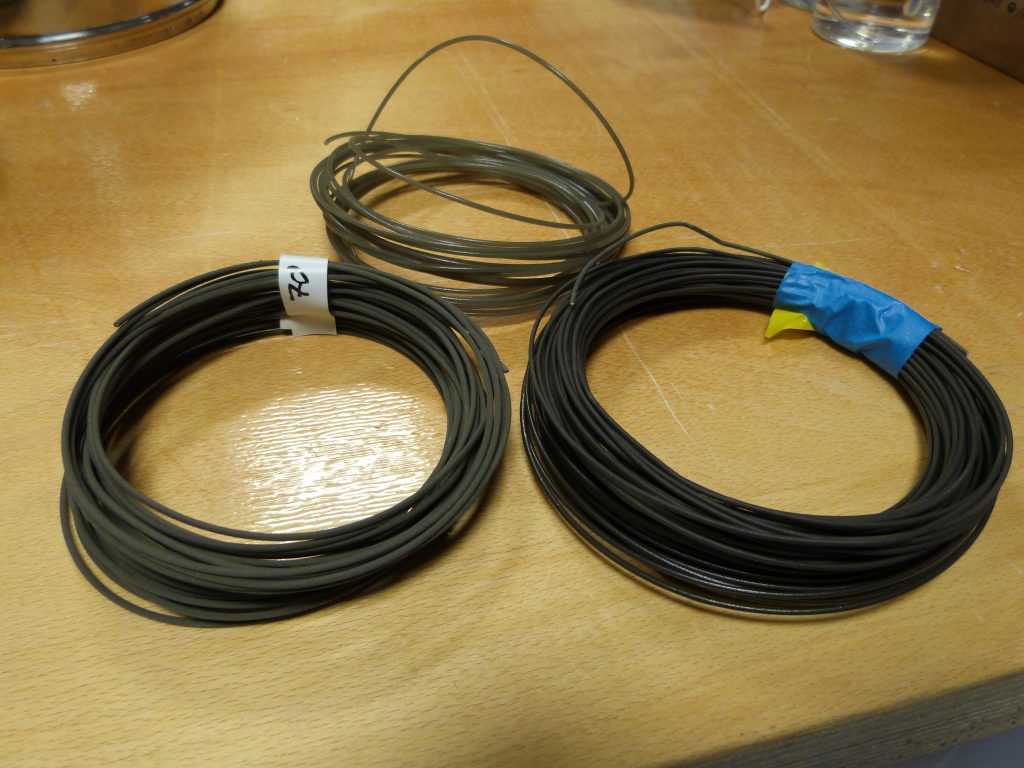
Different filaments used for printing 3D parts with the FDM printer. ESA-A.Hand
“To see if the mechanical properties have really improved, the final parts must be analysed in a laboratory in cooperation with colleagues at ESA’s European Space Research and Technology Centre (ESTEC) in the Netherlands and ESA’s Advanced Manufacturing Lab in the UK,” Aurélie adds.
The next step for this project is to advance with other polymers in the printing process. “This technique works with other common polymers and is a baseline for many advancements. For example, with a new binder solution, we are investigating the sintering of printed composite parts to see how we could create complex shapes from sintered regolith,” Aurélie explains.
After an object is printed, but before it is sintered in a furnace where it hardens into a solid workpiece, it is called a “green body” and remains flexible without crumbling. During the sintering process, the polymers that bind the regolith, are degraded and the regolith grains fuse together to form robust, ceramic-like sintered parts.
While conventional powder sintering without polymers rather allows for the production of simpler green body shapes, adding polymers to the FDM process allows for the production of the more complex green body shapes, that Aurélie and the team are looking for.
In this way, astronauts could print the more flexible polymer and regolith green body parts to use them directly on the Moon. However, if they need stronger, more ceramic-like regolith parts, they can still perform a sintering by placing the printed parts in a furnace.

FDM printed parts from lunar regolith simulant EAC-1, screw (50%) and gear (70%). ESA-A.Hand
A bright future for Fused Deposition Modelling
FDM has been identified as one of the most feasible on-site manufacturing methods for long-duration missions to the moon and has already successfully been tested to work in microgravity on board the International Space Station (ISS). Thanks to this printing technology, not only tools, but also bricks or landing pads could be created. All these ideas are being expanded upon by the Spaceship team and other ESA experts.
“Because FDM can be used with a wide range of materials, this technique could also be used on Mars with martian dust in the future,” Aurélie explains. She is excited by the potential of 3D printed parts in future astronaut missions to the lunar surface how her findings can help this.
“Within the Spaceship EAC team, we are all working on very fascinating topics. I particularly appreciate the ability to connect with experts from all over ESA. It is very inspiring to work on something that could one day be used by astronauts on the Moon. I am excited to see how far my project can go and I definitely want to keep in touch with the next interns working on 3D printing parts from lunar regolith.”
Learn more about the Spaceship EAC programme here
Meet more students and Spaceship EAC interns here