The structural model of the communications system that ESA is supplying for NASA’s Habitation and Logistics Outpost (HALO) on the Gateway recently completed a vibrations test to check it will withstand the intense shaking during the launch.
The HALO Lunar Communication System (HLCS) is an advanced piece of technology that will enable communication between the upcoming lunar space station, the Gateway, and satellites and rovers around and on the Moon.
After a successful design review earlier this year that gave the green light for final manufacturing, industry partners are working to make sure the system will be ready for its launch to lunar orbit on top of the HALO module.
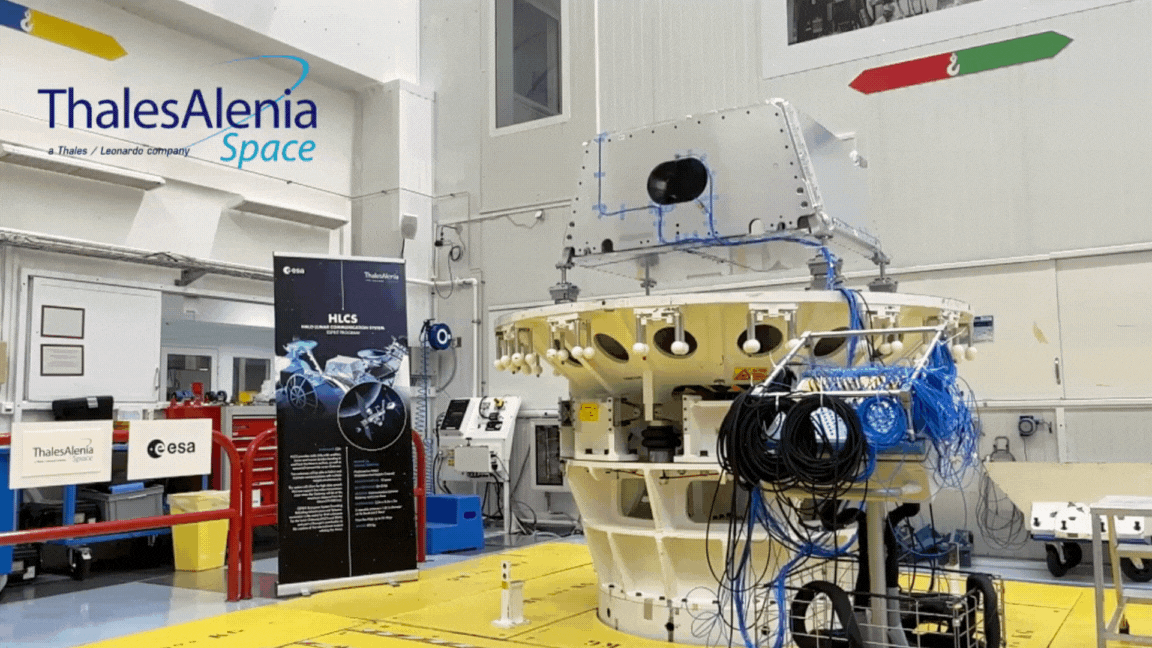
During the vibration test, the HLCS structural model was subjected to intense vibration levels to simulate the entire launch.
Credit: TAS
The launch presents significant challenges, as the powerful vibrations during liftoff can potentially damage space systems. To mitigate this risk, designers go through multiple steps and simulations to ensure the equipment can withstand these vibrations. Each component must not only be strong enough to endure the vibrations but also as lightweight as possible to reduce as much as possible the amount of fuel needed to reach the Moon.
A crucial phase in confirming the accuracy of calculations and simulations involves constructing a structural model, essentially an exact copy of the unit intended for flight. The model replicates the construction and materials of the actual unit, with the internal equipment substituted by dummies of equal weight. Ahead of the test, several accelerometers are strategically placed within the structure. These accelerometers help engineers to monitor the structure’s real-time response and verify that the results seen during computer simulations match what is actually happening.
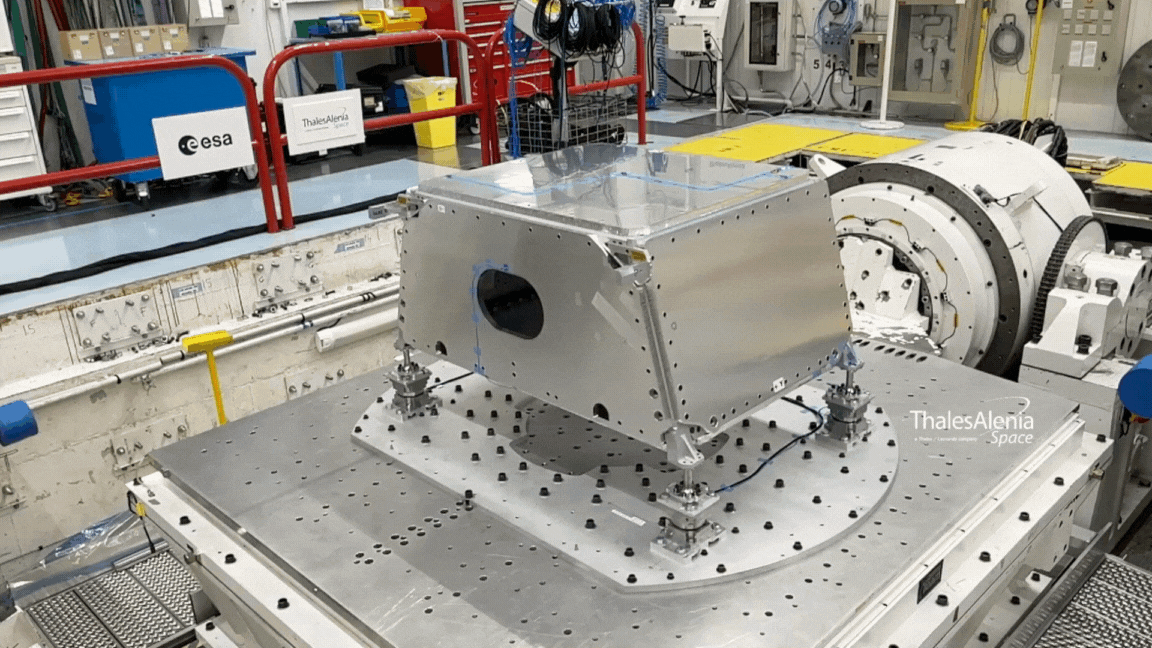
The vibration test includes three different axes to simulate shaking in all directions.
Credit: TAS
In October, the structural model of the main box of HLCS completed a critical mechanical qualification test. This included a vibration test, which checks that the system can endure vibration levels exceeding those expected during launch; this ensures an additional safety margin beyond the anticipated flight conditions. The qualification test was a success, as it aligned with the engineers’ predictions. After passing the test campaign, the manufacturing of the final flight units can begin.
This comprehensive testing and manufacturing process aims to ensure the HLCS is not only functional but also durable and reliable for its mission in lunar communication, navigating the challenges of space travel with resilience and precision.
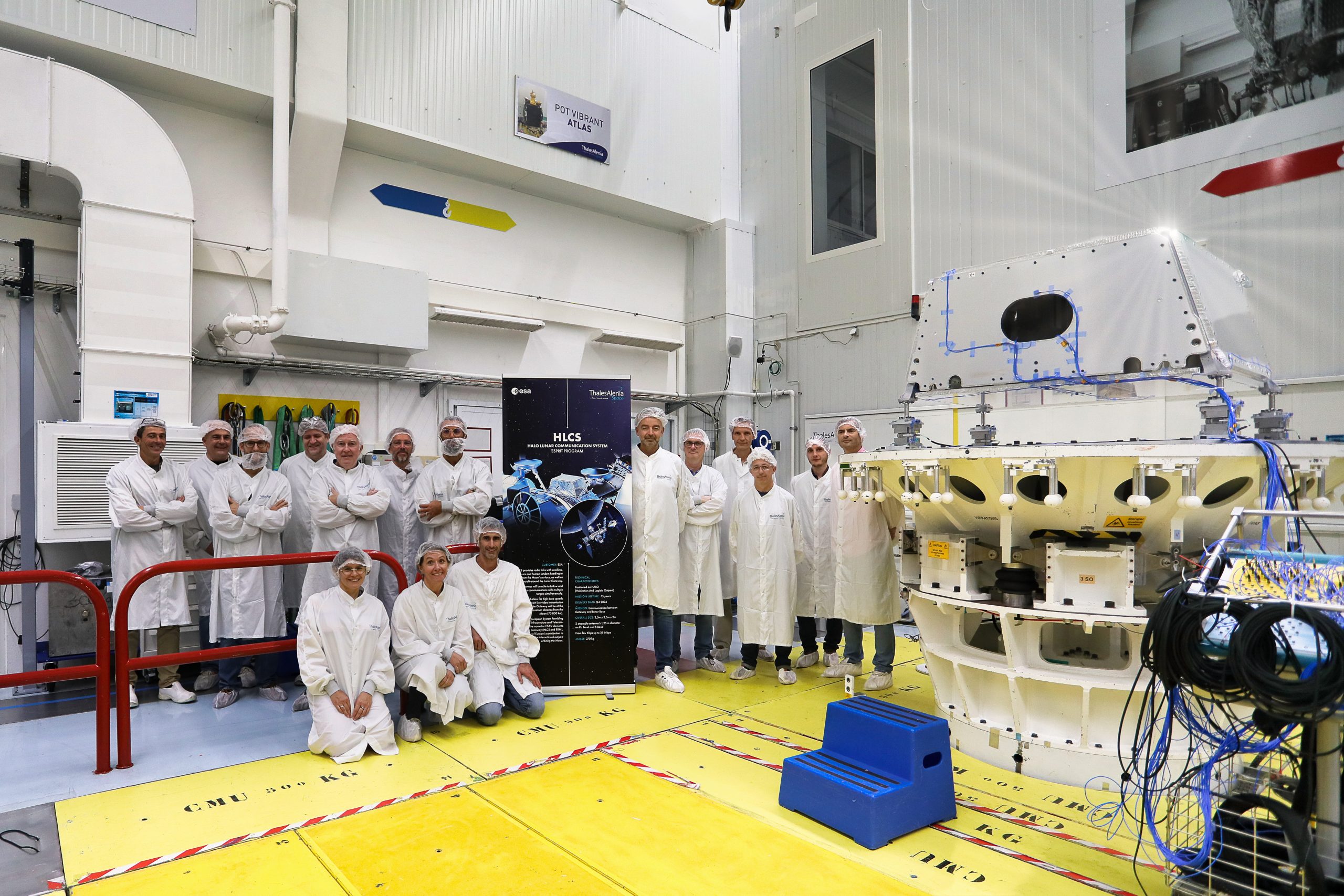
The team building and testing HLCS at Thales Alenia Space in Cannes, France.
Credit: TAS
ESA’s contributions to the Gateway, such as HLCS, are part of the Terrae Novae exploration programme leading Europe’s human journey into the Solar System.