Flexibility is key
When designing components for a future lunar habitat, the more functions a single facility can support the better. Reducing the number and weight of items required for a Moon base will help reduce launch costs – a significant expense in transporting items to space.
Though teams cannot recreate Moon conditions exactly on Earth, there are a number of natural Moon-like environments already being used to test designs and technology. These are often referred to as analogues.
Luna, a new analogue lunar research and training facility and a joint project by ESA and DLR, the German Aerospace Centre, is in the final planning stages. It will combine a 1000 m2 area of simulated lunar soil with a Moon habitat, powered by an innovative energy system, representative of what could be used for a lunar base.
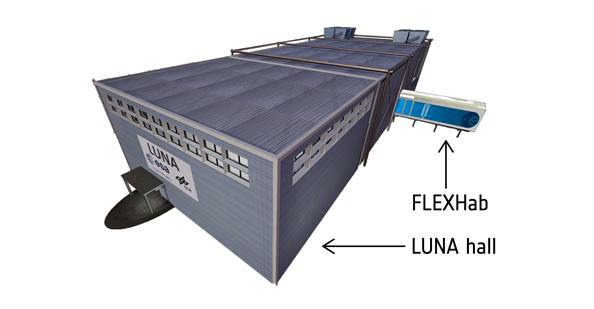
Luna hall and FLEXHab facilities connection. ESA-A. Drepper, L. Ferra, E. Rosselli Del Turco, C. Scott, P. Turrión San Pedro
The habitation module developed for Luna is known as the Future Lunar Exploration Habitat, FLEXHab. Emilia’s challenge was to build on designs for an integrated and flexible rack system, called FLEXRack, that will sit inside this module to support and test payloads such as life support equipment or plant growth experiments that could one day travel to the Moon.
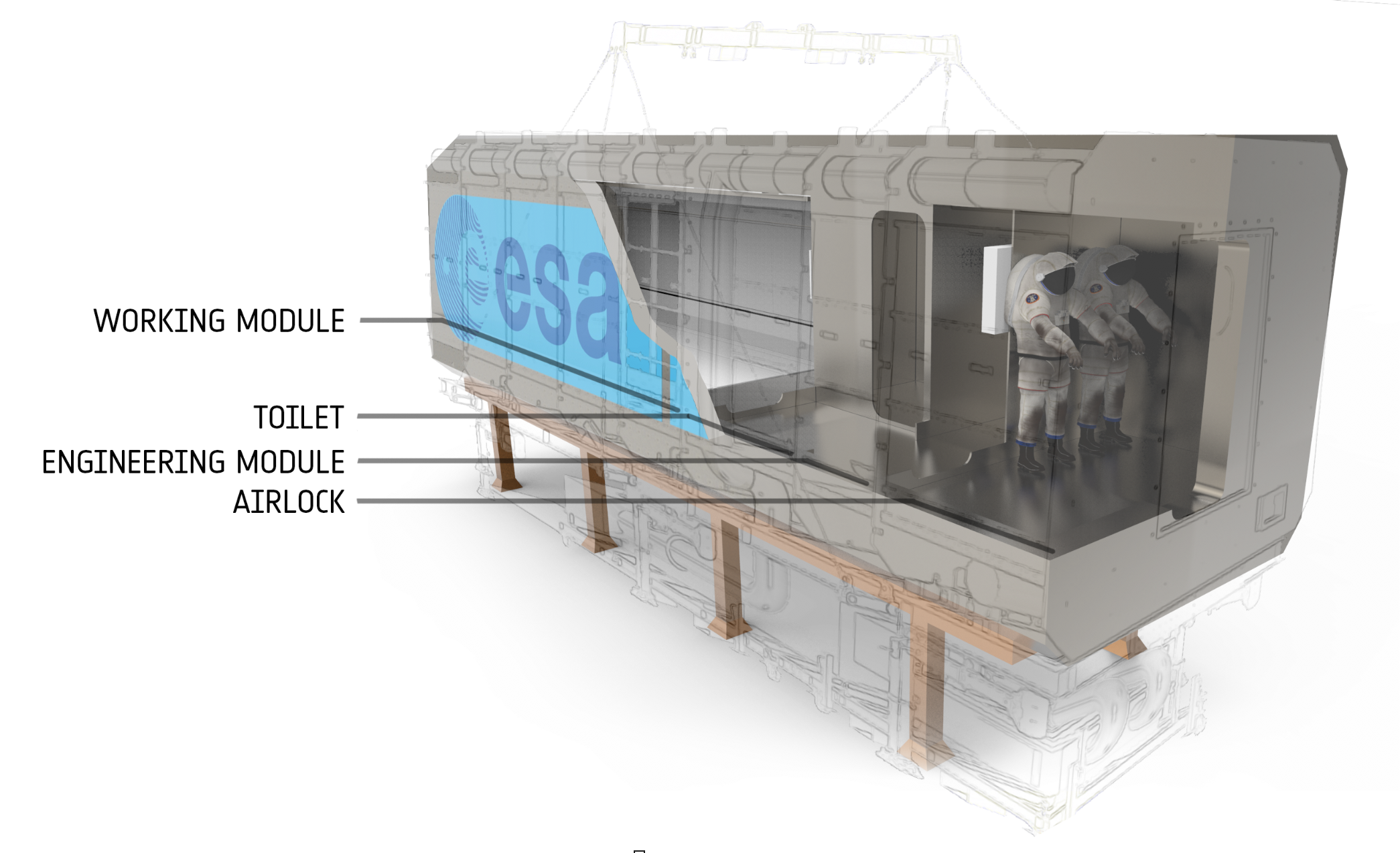
Section model of FLEXHab. ESA-E. Rosselli Del Turco
Finding a user-centric solution
To maximise the number of experiments and equipment FLEXhab can support in a limited operating environment, Emilia needed to think carefully about FLEXRack’s design.
At the same time, she needed to consider the human factor – for an easy-to-use convertible workstation that many different people could learn to operate.
To improve interactivity between the rack, its different users and their activities, Emilia started by creating and evaluating a series of usage scenarios. Building on this and an initial concept developed by former interns, she decided to create adaptable user interfaces and build the FLEXRack from modular components that can be moved and reused.
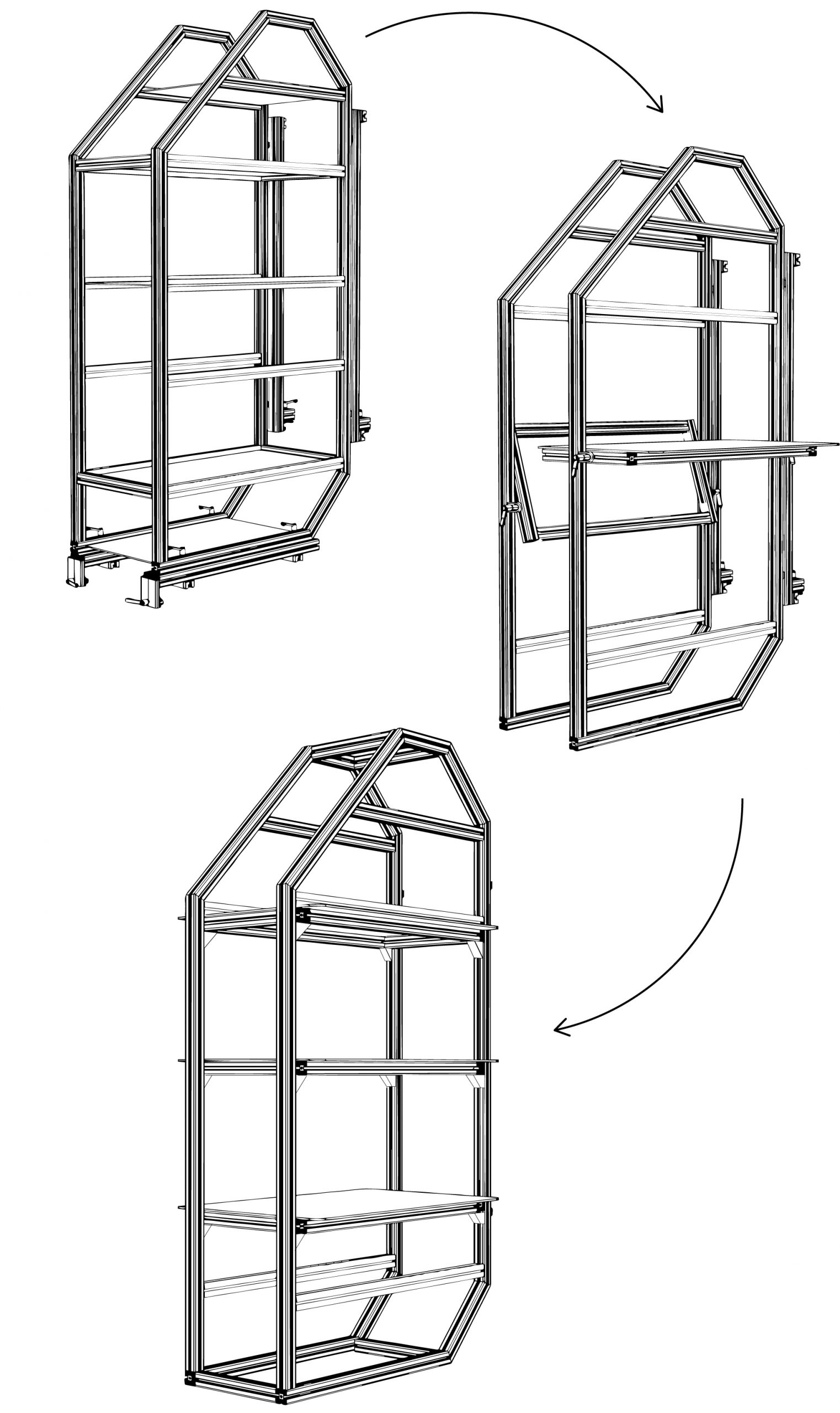
Evolution of adaptable FLEXRack design. ESA-E. Rosselli Del Turco
“In a nutshell, I tried to make assembly, disassembly, storage, and operative adjustment as easy and effortless as possible so that the user is in full in control of its configuration to best support the tasks performed”, Emilia explains.
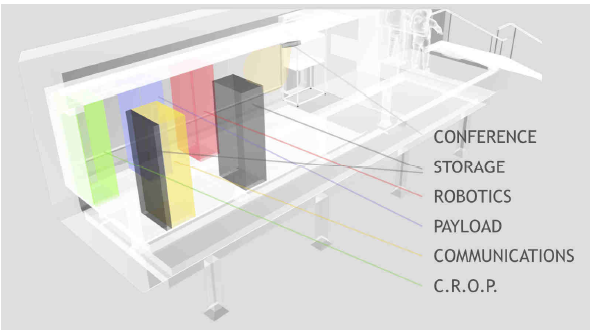
Example of usage scenario for FLEXHab. ESA-E. Rosselli Del Turco
Her design showed so much promise, it has now been outsourced to an external manufacturer for final adaptation. Once finalised and installed in the FLEXHab facility, it will support analogue missions by hosting different scenarios in one facility, opening the way for geological spacewalk simulations, as well as operational and technological tests and training.
Where space meets design
Emilia is optimistic that the multifunctional design of the FLEXRack offers a suitable solution for use in lunar habitats or analogues and hopes that her product design ideas will be part of this development.
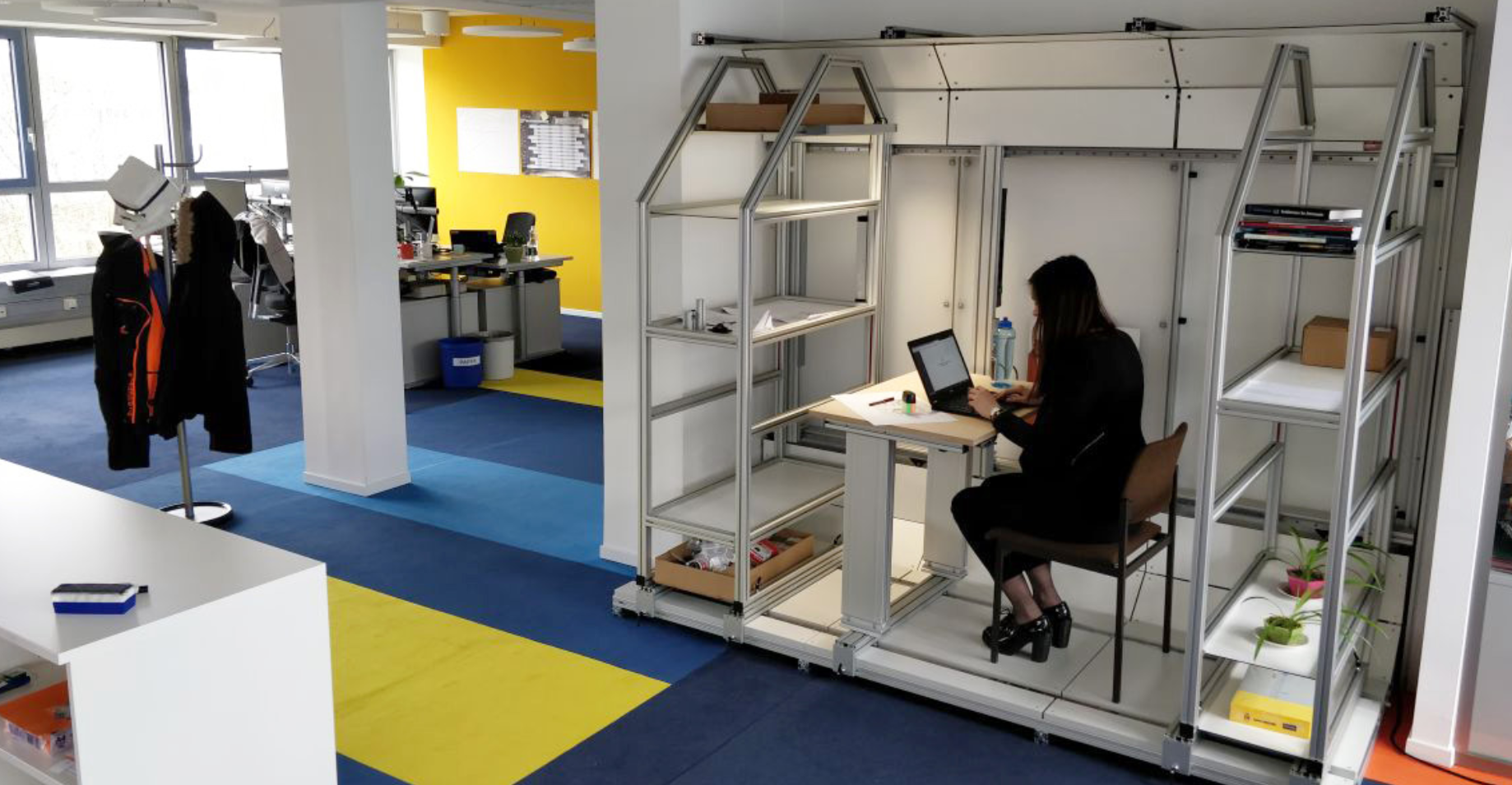
FLEXRack prototype built by Spaceship EAC interns at EAC. ESA-M.Thallner
“I think it provides interesting inputs for the design of reconfigurable, modular and flexible appliances, that can host most kinds of payloads and workstations in the same standard structure. I hope that some of my ideas will actually travel across the process and maybe impact the design of future shelf systems, if not on the Moon, at least in analogue habitats,” she says.
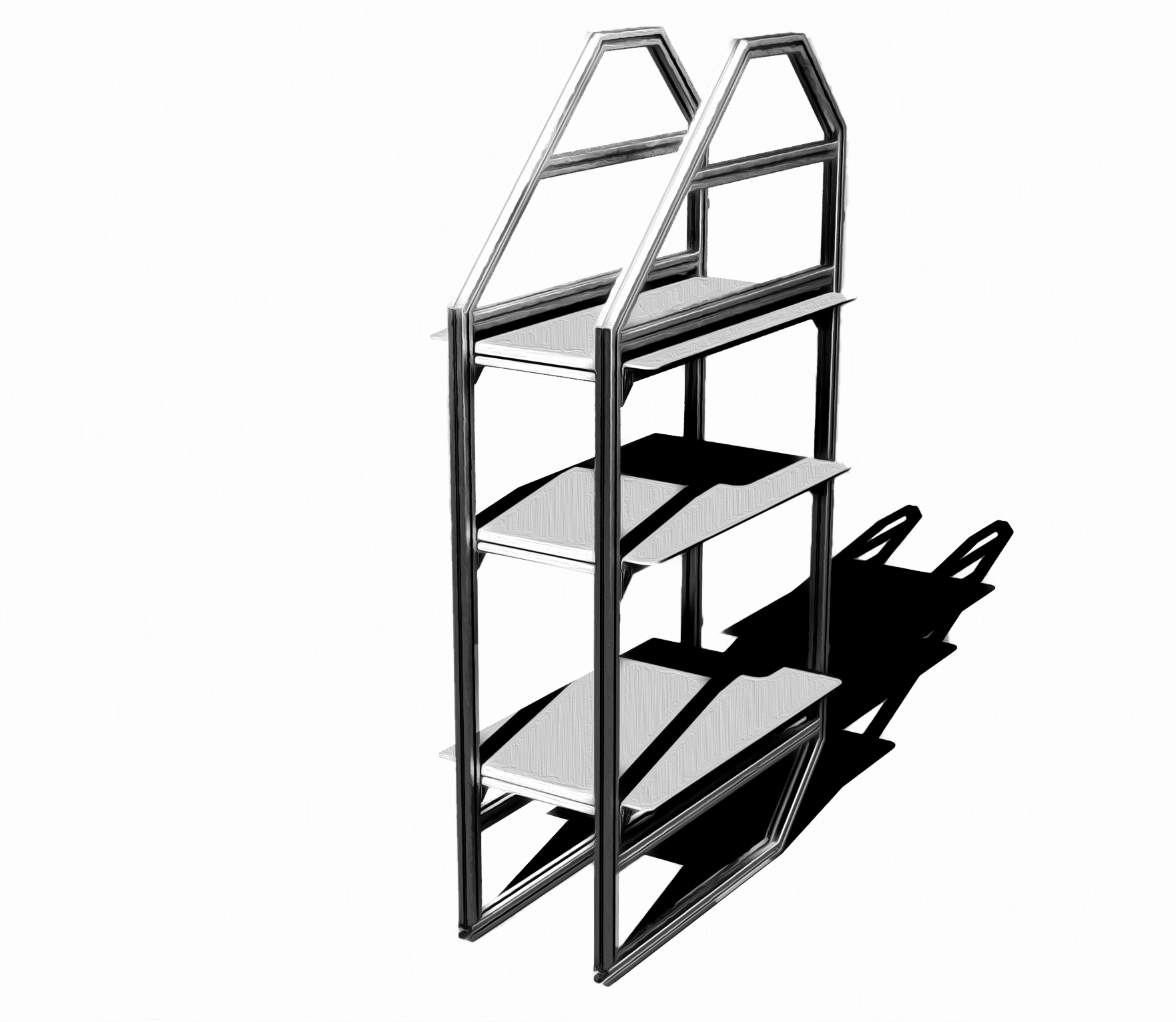
3D model of final FLEXRack design. ESA-E. Rosselli Del Turco
Emilia also sees her internship as allowing the design world to take another small step into the space industry, showing that design offers valuable ideas for integration, especially in interdisciplinary teams like Spaceship EAC.
“To understand how I, as a designer, could best blend in such a technical environment and contribute to the collective work was actually one of my biggest questions. But thanks to great collaboration within the team, joining people from many different backgrounds, we could always enrich each other with our ideas and generate solutions together. This was extremely valuable to me.”
Interns previously involved in the development of FLEXRack:
- Manfred Thallner (FLEXHab Working Module – Architectural Requirements and Prototyping for a Lunar Base Analogue)
- Orla Punch
- Thomas Dijkshoorn
Find out more about Spaceship here.