This summer marks the ten-year anniversary of the electromagnetic levitation facility on the International Space Station.
Helping to reveal the core physics at play in materials science, the Electromagnetic Levitator (EML) is a furnace in ESA’s Columbus laboratory that can melt metals by induction heating them up to 2200 °C. Scientists can then observe the samples in a molten state, or while solidifying in weightlessness as they cool rapidly. On Earth, this process is influenced by gravity and the sample’s contact with the walls of the furnace.
The fifth and last Automated Transfer Vehicle brought EML to the International Space Station in the summer of 2014. ESA astronaut Alexander Gerst installed the facility during his Blue Dot mission and EML has been hosting science experiments ever since.
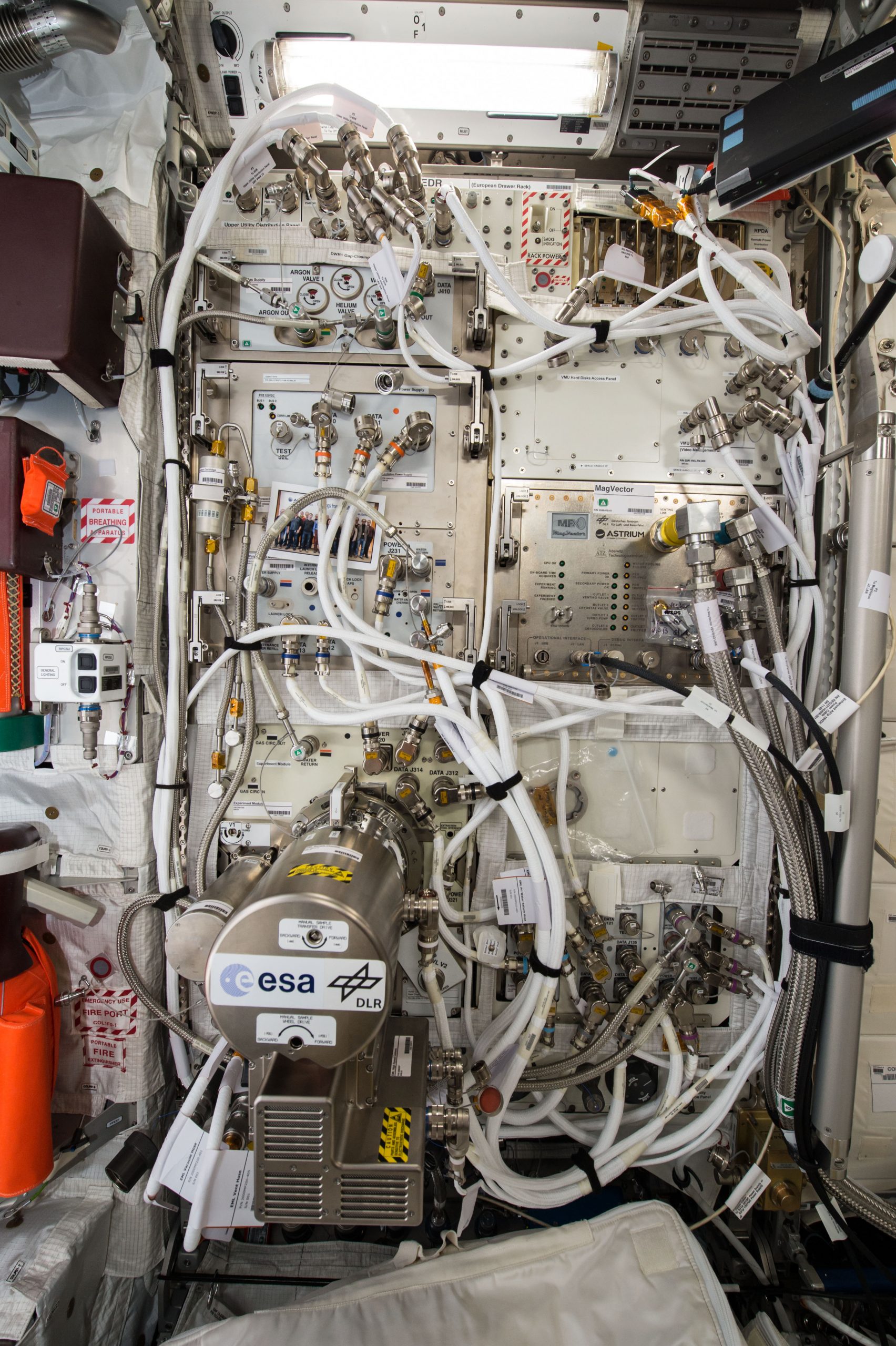
EML in ESA’s Columbus module on the International Space Station.
Credit: ESA/NASA
A brief history
The electromagnetic levitation technology has been tested using low gravity platforms since the 1980s, first on parabolic flights and sounding rockets and then on Spacelab, Europe’s laboratory on the Space Shuttle. These platforms offered increasing amounts of time in reduced gravity to material scientists and the International Space Station was the next logical step.
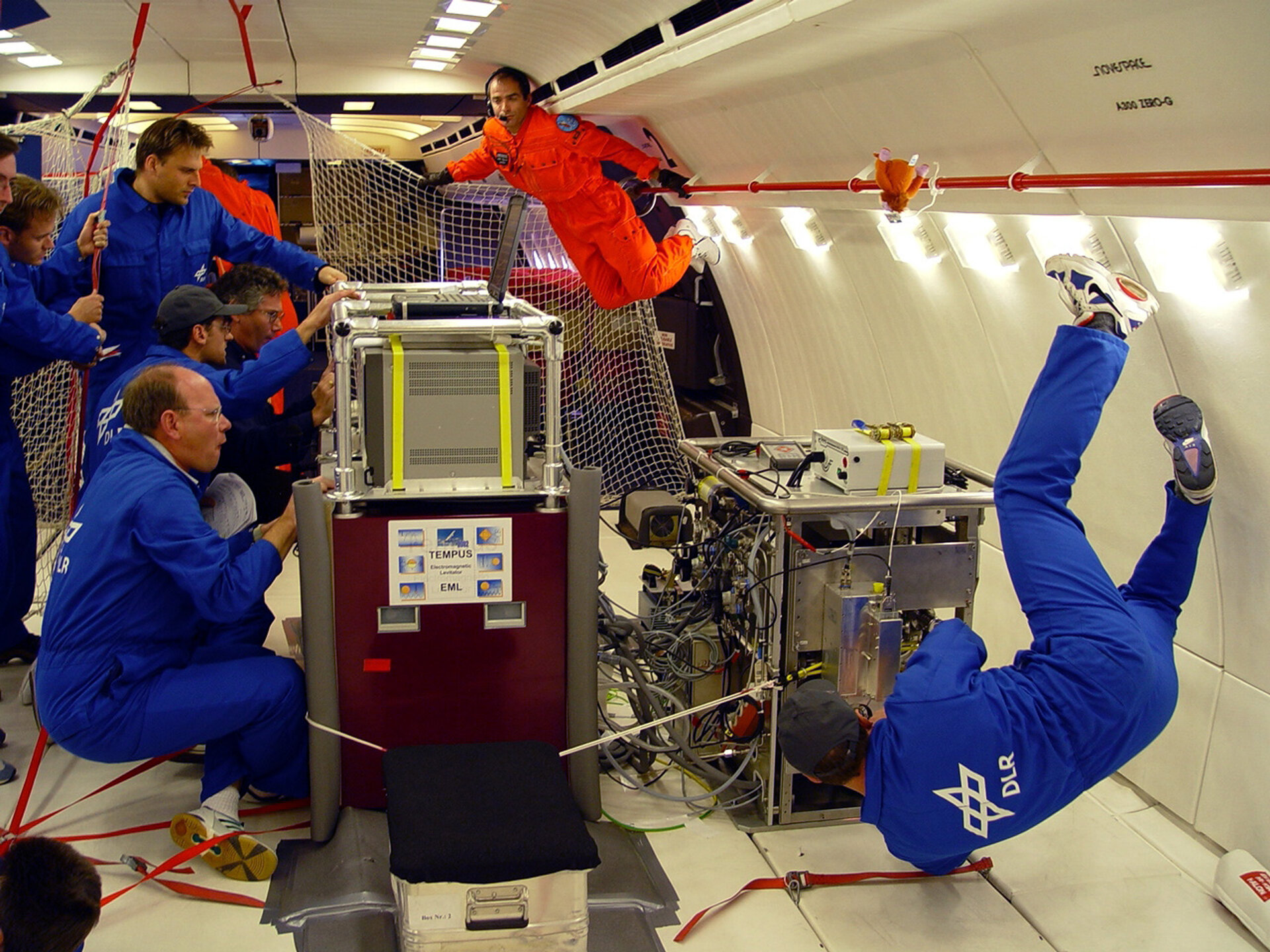
TEMPUS, an electromagnetic levitator used on Space Shuttle flights, and parabolic flights to this day.
Credit: Airbus Defence and Space
After years of development, EML was sent to the International Space Station in 2014. Usually, a facility is fully assembled before being sent, however EML’s size meant it had to be separated into modules, some of them the size of washing machines, prior to launch. Alexander Gerst had to assemble the module inside the Columbus module. During this procedure, a bolt became lodged; swiftly, he improvised by sawing through the screw, cleverly using shaving foam to contain any metal debris within the microgravity environment.
Installing the Electromagnetic Levitator presented certain challenges, but with great teamwork between space and ground teams, a little ‘McGyver-ing’ and a rather unusual tool we overcame them all. Switching it on was a big moment for me. It’s great to see this facility still going strong, exploring metal alloys for the technologies of tomorrow,” says ESA astronaut Alexander Gerst.
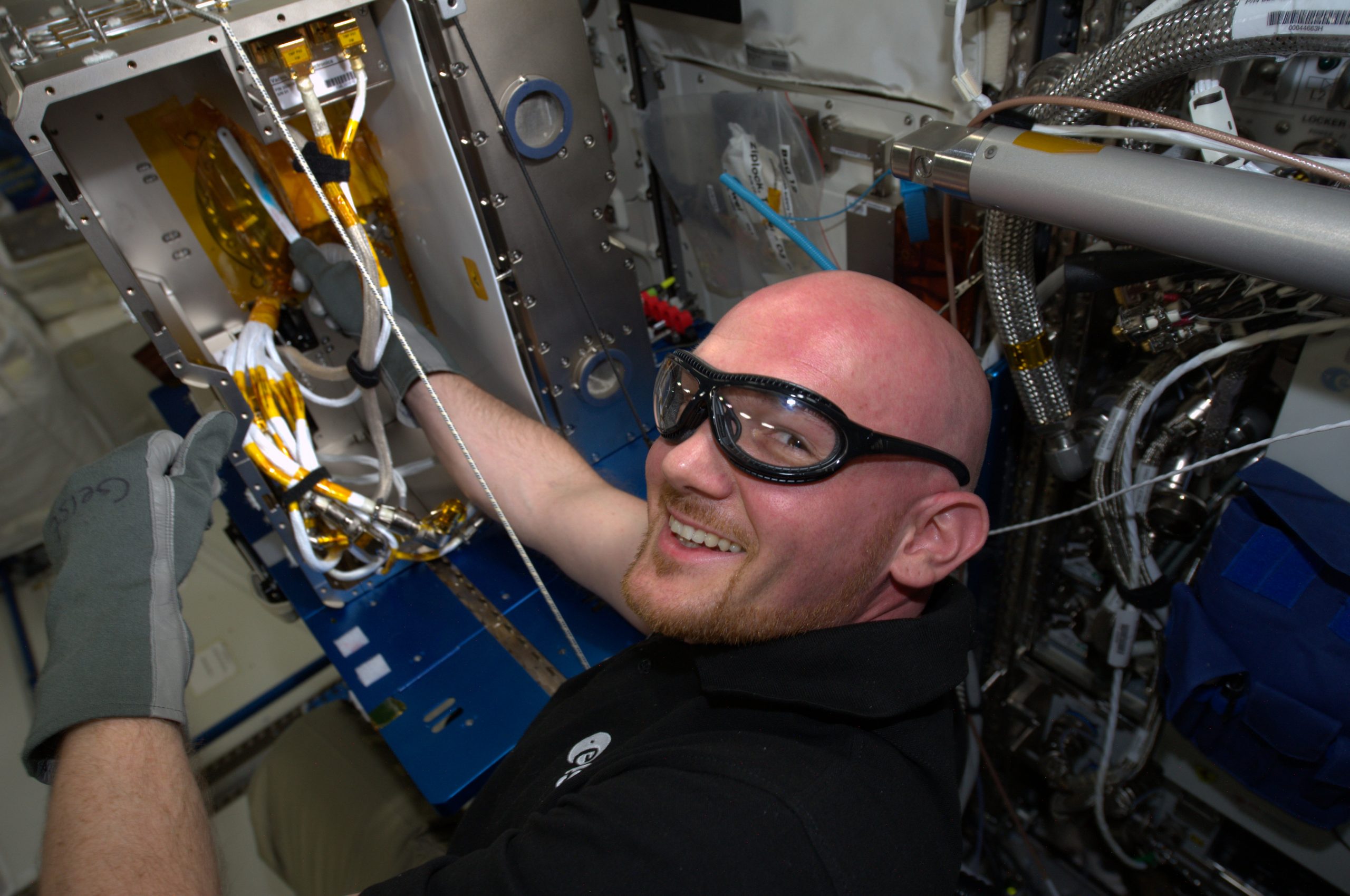
Alexander Gerst installs EML on the International Space Station
Credit: ESA/NASA
Co-developed by ESA and the German Space Agency (DLR), designed, assembled and tested by European industry led by Airbus Defence and Space, EML has now been in operation for a decade, commanded from the Microgravity User Support Center (MUSC) in Cologne, Germany.
Science time
The research aims to better understand the properties of materials on the very small scale to construct precise models of how these materials behave on the larger scale.
EML helps scientists study the solidification processes of materials such as alloys, blends of materials selected to offer the best attributes of their parts. This improved understanding of materials could lead to optimisations within the manufacturing industry. This includes the creation of materials, refining casting and related processes such as 3D printing that could lead to more efficient and high-quality materials or reducing energy consumption. These benefits are particularly useful in the automotive, aviation and space industries.
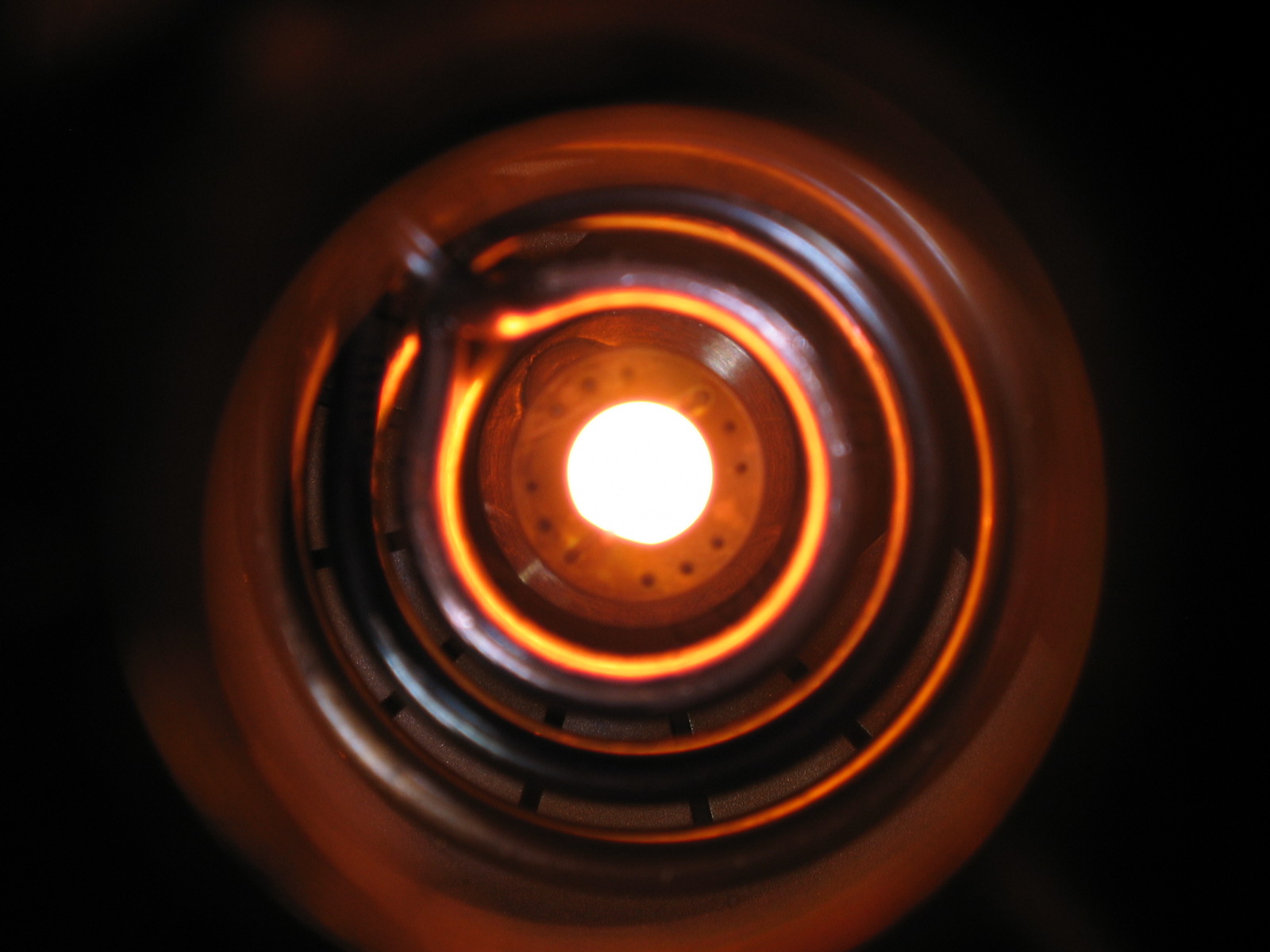
Tungsten sample in an electromagnetic levitation experiment on a parabolic flight.
Credit: Airbus/DLR/ESA-K. Kullack
These materials science studies can be performed on Earth, but EML is particularly useful as it allows scientists to study samples with the least possible interference, from either gravity or the material’s contact with its surroundings. In the experiment, the sample material is levitating in vacuum, or in a non-reactive gas such as helium and argon; this means the experimental conditions are less disturbed than they would have on Earth.
Scientists from all over the world can benefit from these special conditions. Every few years, a batch of 18 samples is selected to fly to the Station, where an astronaut loads them into EML on a revolver-like carousel. The microgravity furnace processes each sample and records the material and fluid behaviour with a high-speed camera and various sensors, before sending the data to MUSC and science teams.
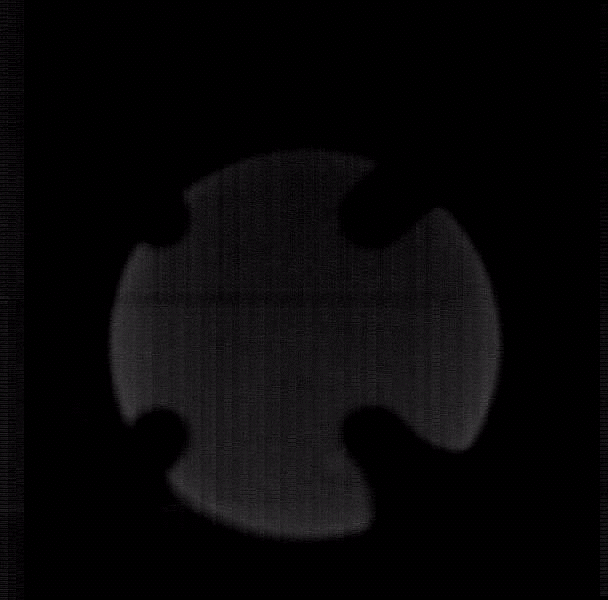
A sped-up video of an aluminium and nickel alloy solidifying in EML
Credit: ESA/DLR
Being a materials scientist myself, the wonderful Electromagnetic Levitator was very close to my heart. When a gas circulation pump needed to be replaced during my Cosmic Kiss mission, I happily took on the task to keep this excellent facility running,” shares ESA astronaut Matthias Maurer.
Results are in
EML has already been in use for a decade and was designed to work for several more years. In the last decades, over 700 publications have resulted from the experiment and its heritage, with a large majority appearing in top materials science journals. Below are three examples showing how materials science research from EML benefits our society.
One: structural materials
Aluminium and steel are examples of structural materials used in construction. Metal production and manufacturing are large industries, with almost a hundred million tonnes of aluminium and a billion tonnes of steel produced every year.
Research conducted using EML, for example the Thermoprop project, has helped scientists better understand how these materials solidify as well as their behaviour at high temperatures and the impact this has on casting processes, leading to more efficient manufacturing processes.
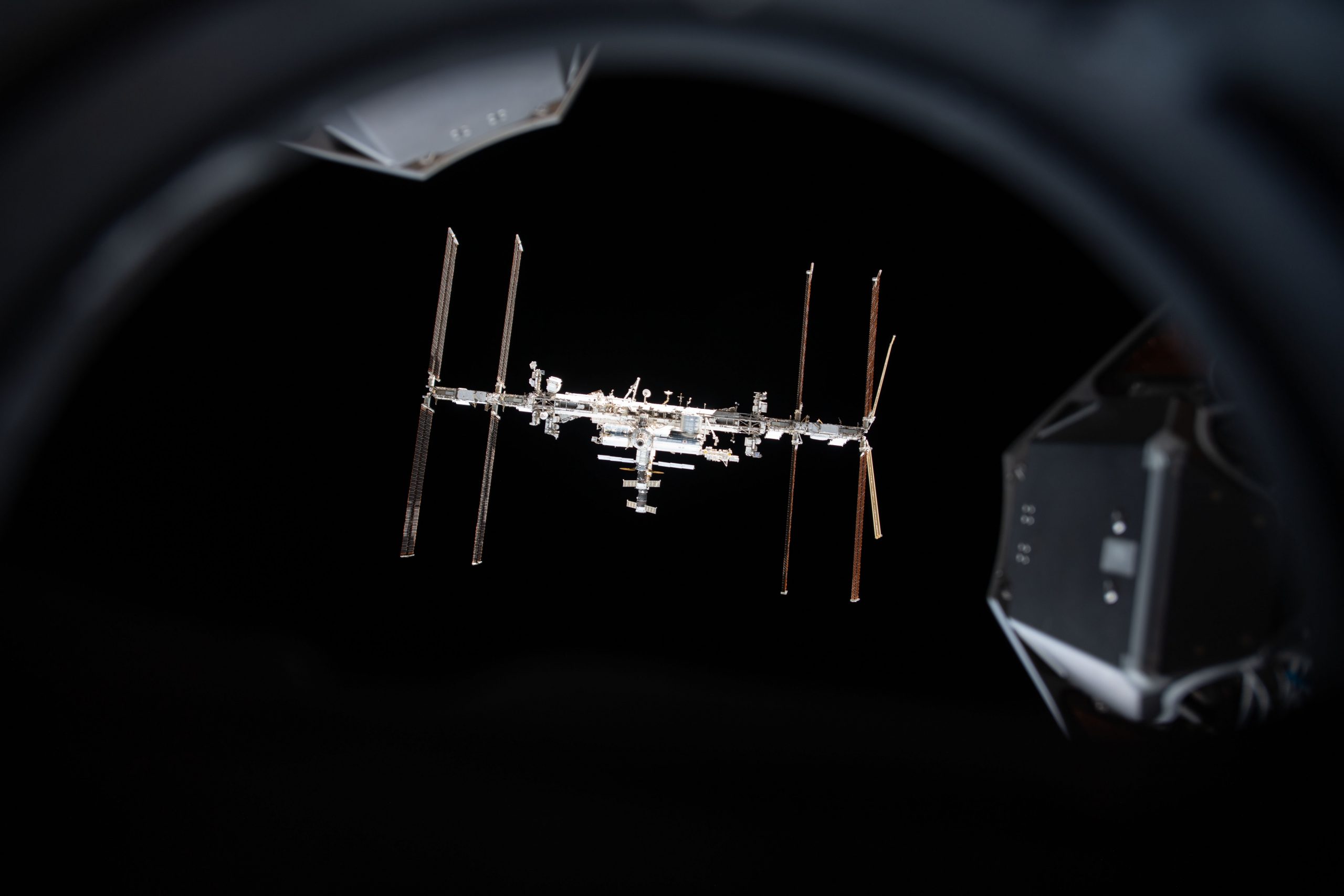
The International Space Station is partially made of steel and aluminium
Credit: ESA/NASA-T. Pesquet
Two: functional materials
Functional materials are characterised for having intrinsic physical properties, such as magnetism. Scientists can alter these materials to significantly change their properties – this is how semiconductors are made. Semiconductors are materials that have been altered to conduct electricity selectively, acting like an electronic switch.
Semiconductors are essential for our modern world. They are the basis of almost all of today’s electronics, from routers to laptops to your mobile phone. However, any imperfections or impurities can have a drastic effect on how the semiconductor materials behave.
Research conducted using EML, such as the ESA SEMITHERM project, helps researchers to better understand the materials used to form semiconductors, notably silicon and germanium, and how to control defects.
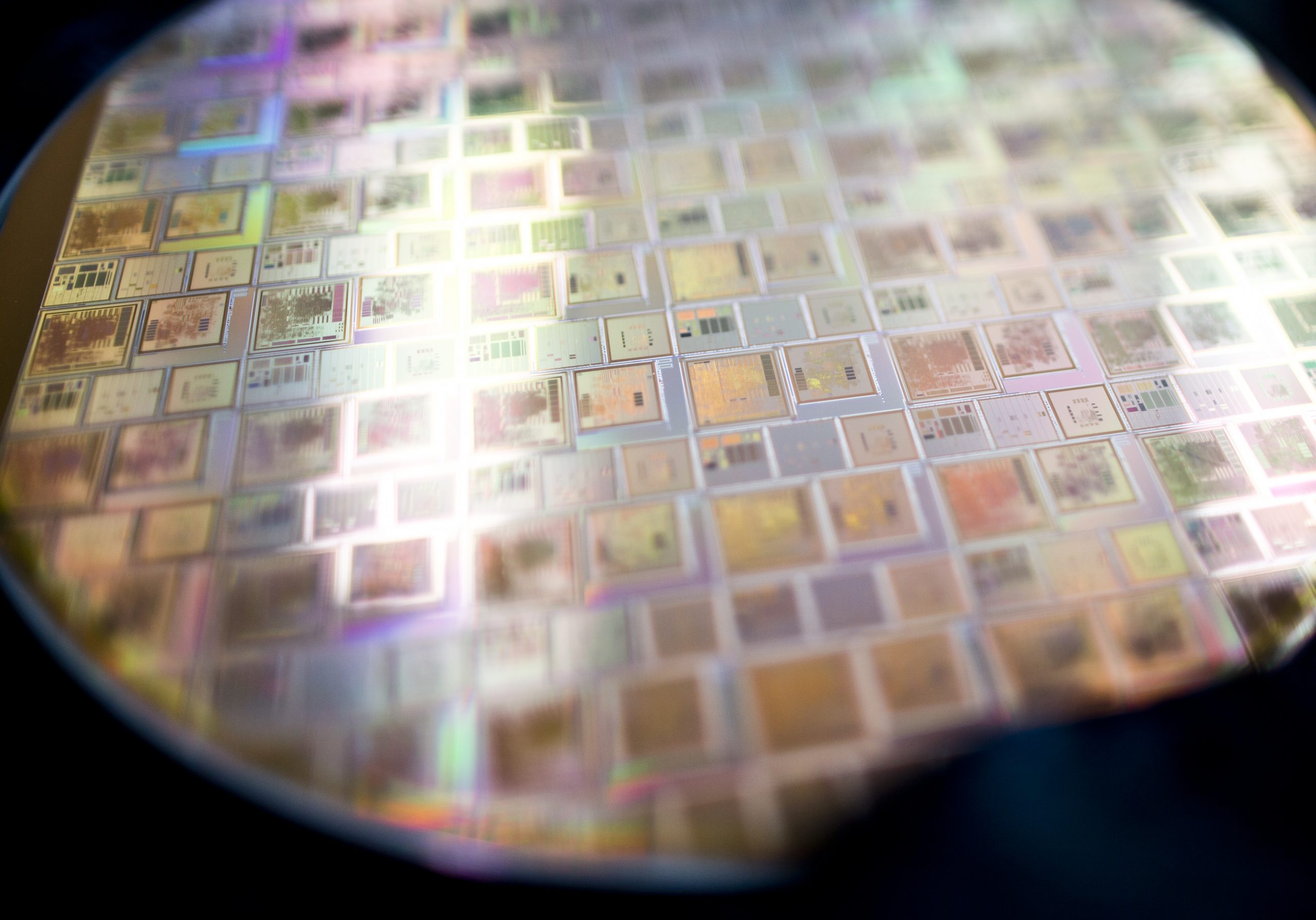
Integrated circuits on silicon
Credit: ESA-G. Schoonewille
Three: high-performance materials
High-performance materials, such as superalloys, are engineered materials designed to withstand and operate under extreme conditions, for example at very high temperatures close to their melting points. These materials have various applications, the most common to build turbine engines for energy and aerospace industries. However, these turbines can suffer from deformation over years of being subjected to high temperatures and pressures. Research conducted using EML can help scientists to better understand these materials and their thermophysical properties to improve manufacturing processes. High-performance materials are also important for biomedical purposes, such as hip replacement implants which are made of titanium alloys.
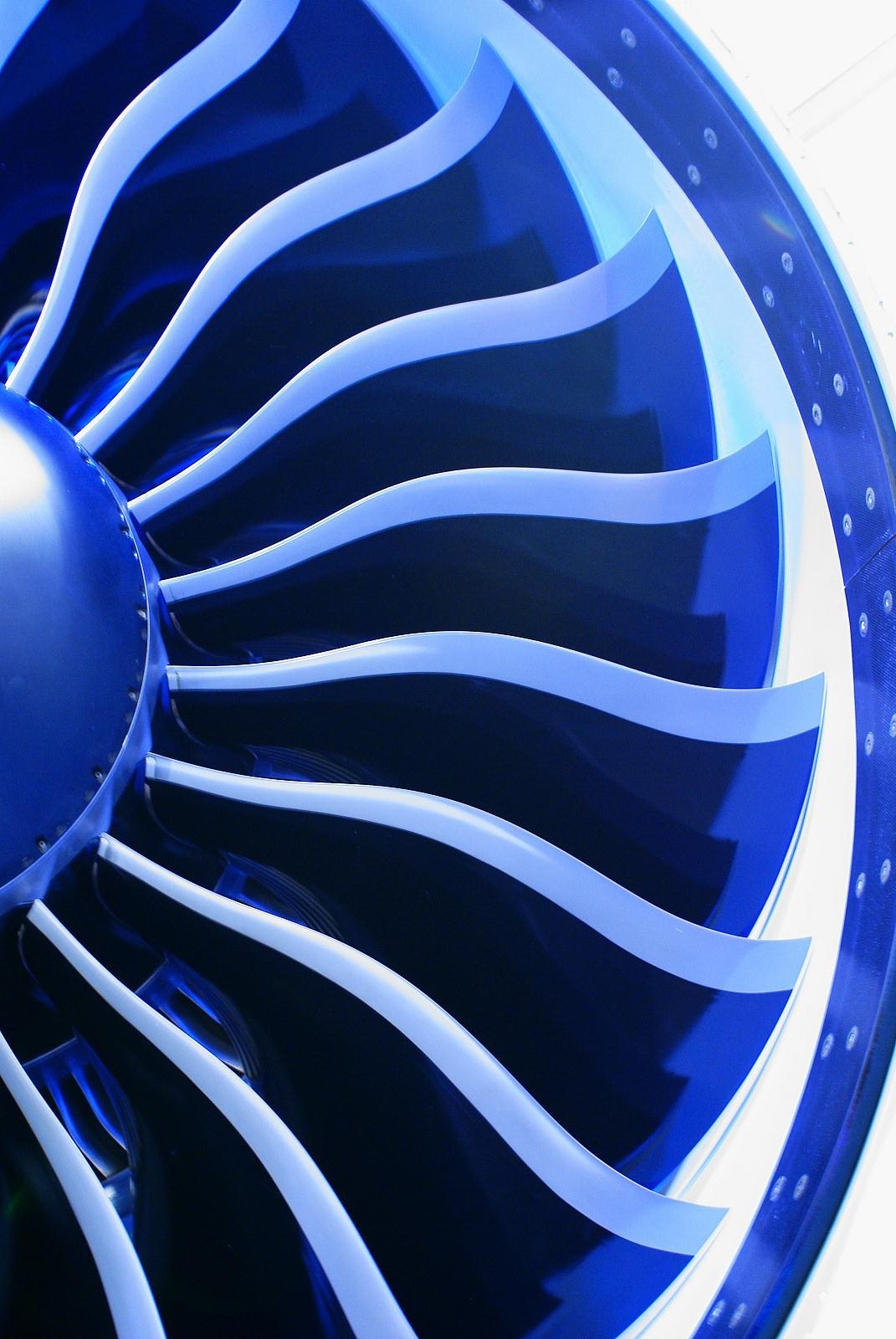
ESA research has helped to develop an aircraft-grade alloy that is twice as light as conventional nickel superalloys while offering equally good properties.
Creative Commons-Bleuchoi
The journey continues
EML is currently working with its third batch of samples, with a fourth batch ready to be sent to the Station and a fifth batch being prepared by scientists. A new module containing an oxygen control system for the instrument will be launched and installed by a crewmember next year, allowing scientists to precisely measure and control the oxygen content of the EML process environment.
ESA will host an event on 22 May to celebrate the ten-year anniversary of EML with DLR and the scientific community using the facility.