New regulations require future satellites to guarantee by design that risk for casualties on ground during re-entry is less than 1 in 10.000. This is already state-of-the-art for small satellites. However, for satellites bigger than 500kg, and in particular for the ones with large optical payloads (e.g. big mirrors), it is a difficult challenge to meet this requirement.
When you cook potatoes in boiling water, small potatoes will cook through quicker than bigger ones. The same principle applies for spacecraft during re-entry. A big spacecraft will absorb more heat than a small one before starting to melt and disintegrate in the atmosphere.
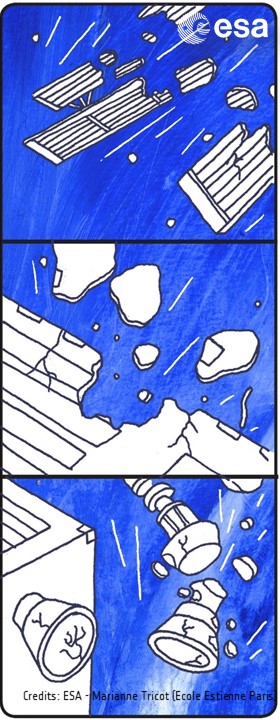
Pieces of satellites do not melt during atmospheric reentry
Credits: ESA – Marianne Tricot (Ecole Estienne Paris)
Typical satellite-parts that may survive re-entry include critical equipment (such as tanks, reaction wheels, magnetorquers and large mechanisms), elements of optical payloads and in some cases also parts of the satellite structure. Most of these parts burn completely during re-entry if exposed early enough to the atmospheric flow.
However, especially for larger spacecraft, direct exposure may happen too late and even equipment that could easily demise (i.e. burn completely) will not be exposed to the external hot flow for enough time. This means that there is an unacceptable chance that they impact on soil or in the oceans and lead to casualties. A way to mitigate that is to design satellites in a way that the structure opens up or breaks up as early as possible during the re-entry what will lead to a higher exposure of parts to the atmosphere and as a result a full demise of the satellite.
Within CleanSat, we are looking for the best techniques to improve the controlled break-up of satellites and thus, ensure that they will fully demise into the atmosphere. We already know that sooner or later the structure of a satellite will break up during the re-entry exposing the internal equipment (unless the spacecraft has been deliberately designed to survive re-entry).
To make sure that the internal equipment is exposed early it is therefore necessary to promote the break up process either by actively breaking up some of the mechanical links between the structure elements – i.e. by ground command with the satellite still active and in-orbit – or by weakening the structural joints to make sure these elements are breaking by themselves at high altitudes – i.e. with no needed activation from ground and well after the satellite’s end-of-operations.
If the satellite structure is opened actively, while the satellite is still operational and therefore in orbit, it must be guaranteed that no objects or fragments are released for the remaining years during which the satellite will still be in orbit. Panels can for example be opened in orbit e.g. at end of life, as long as they stay attached to the satellite, using pyro actuators or shape memory alloys in a controlled operation. This approach improves the predictability of the re-entry demise process.
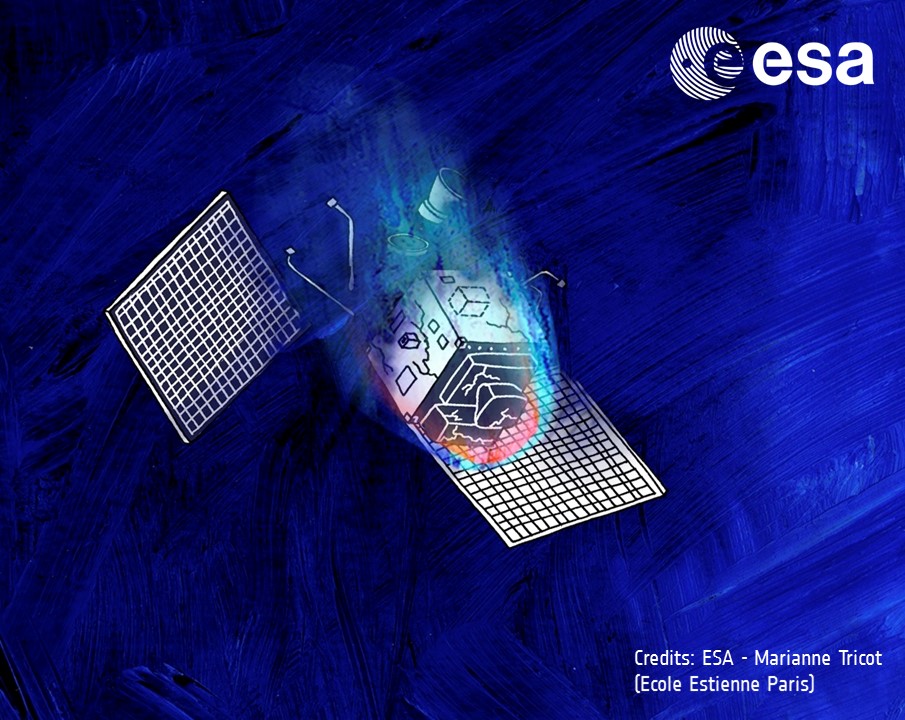
A satellite re-enters the atmosphere and starts melting
Credits: ESA – Marianne Tricot (Ecole Estienne Paris)
Alternatively, the break up can be achieved passively during re-entry itself. The weakened joints allowing for the early dismantlement of the satellite structure during re-entry must therefore survive the space environment and guarantee the structural integrity of the spacecraft. This must be achieved for very long periods of time even with the satellite uncontrolled. The current observation indicate that the satellite natural break-up starts around 80 km. Hence, for this technique to be effective, the break-up should happen above 85 km of altitude. At these altitudes the atmosphere density is very low and therefore the aerodynamic forces acting on the structure are extremely low. Hence the structure won’t be broken by mechanical forces. On the other hand the external structure of the satellite, which is exposed to the atmospheric flow, will heat up significantly even at high altitudes due to the friction. Hence thermal loads can be used to melt or break-up the structural joints. This is why we are now considering new structural joint designs using for example demisable washers or epoxy glues.
Within CleanSat we are promoting a number of studies and technology activities to define feasible and reliable designs of building blocks to achieve the active and/or passive break-up of the satellites’ structure. In parallel we are studying new approaches to allow the test of these functionality and improve the current simulation tools used to support design for demise.
All these developments aim at reducing impact risk on ground resulting from the re-entry of future satellites and at the same time minimize piling up of space debris.
Discussion: 3 comments
Please could someone consider the environment and instead of causing space junk to vapourise in the atmosphere, causing heavy metal pollution, direct said junk away from our planet, perhaps to the moon in anticipation of luna industrialisation which might include a recycling facility.
Unfortunately a higher orbit is only possible with huge propellant reserves.
After time every satellite in earth orbit (mainly in low earth orbit) comes down due to air drag and other effect.
Environmental save satellites is a big topic, but main risk here is propellants (mono-propellants like Hydrazine), which is still a topic of research and development.
The idea of “saving” Earth and polluting space and moon raises moral questions as well and Planetary protection requirements are in force.
Furthermore, as Michael says it is technically not evident at all because of propellant required.
The number of satellites to be burned down is extremely small but in order to have some quantitative numbers ESA has started to studies to evaluate them. Results in one year !