The completion of a “Deployable membrane” activity through ESA’s GSTP programme has helped advance a new type of European passive de-orbiting subsystem, undertaken through ESA’s Clean Space initiative.
The industrial team composed by HTS as prime with HPS and DLR Bremen as subcontractors presented the results at ESTEC at the start of this month, detailing the extensive test campaign performed for the project.
The main focus was the development of a lightweight, robust and reliable membrane to be used as a drag sail, to enable the passive de-orbiting of a satellite at its end of life in less than 25 years, ensuring compliance with international debris regulations.
Recent years have seen many demonstrations of sail deployment systems for de-orbiting by drag augmentation, but this is the first time such an intensive test campaign has been conducted to verify the mechanical and environmental loads involved.
With the “Deployable membrane” activity, the sail material (12.5μm Upilex S with 100nm VDA, coated by UBE) has been tested at material, sample and demonstrator level including, among other testing, atomic oxygen (AO) testing, UV testing, impact, thermal cycling and crack propagation.
The environmental tests were variously conducted at DLR in Bremen (UV tests), and at ESA/ ESTEC (AO tests).
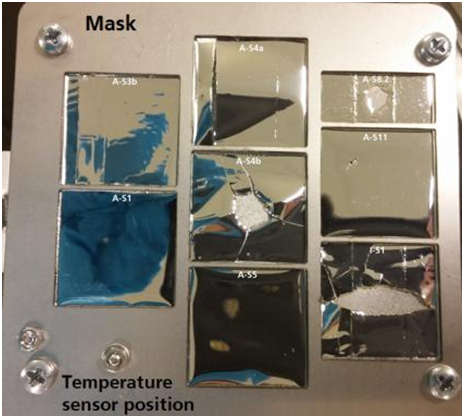
UV test sample holder
Credit: HTS
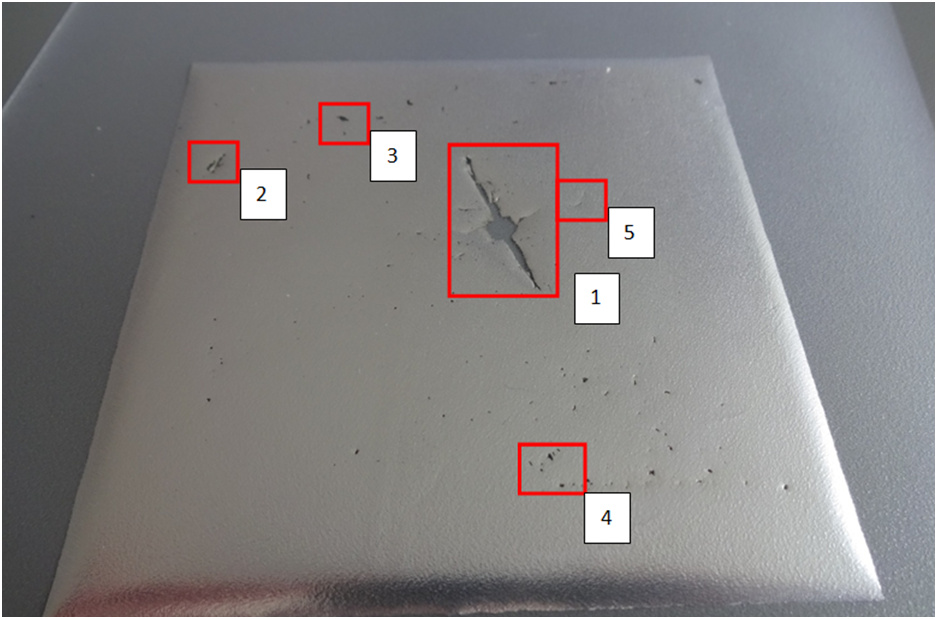
Impact test sample
Credit HTS
Crack propagation tests were also performed, both at room temperature and down to -80 centigrade.
The crack propagation tests performed in this project should be continued in future, taking into account testing at < -150 °C to acquire all data required to calculate the crack yield values. As a results crack propagation risk of the sail can be assessed down to very low temperatures.
The test flow chart is as follows:
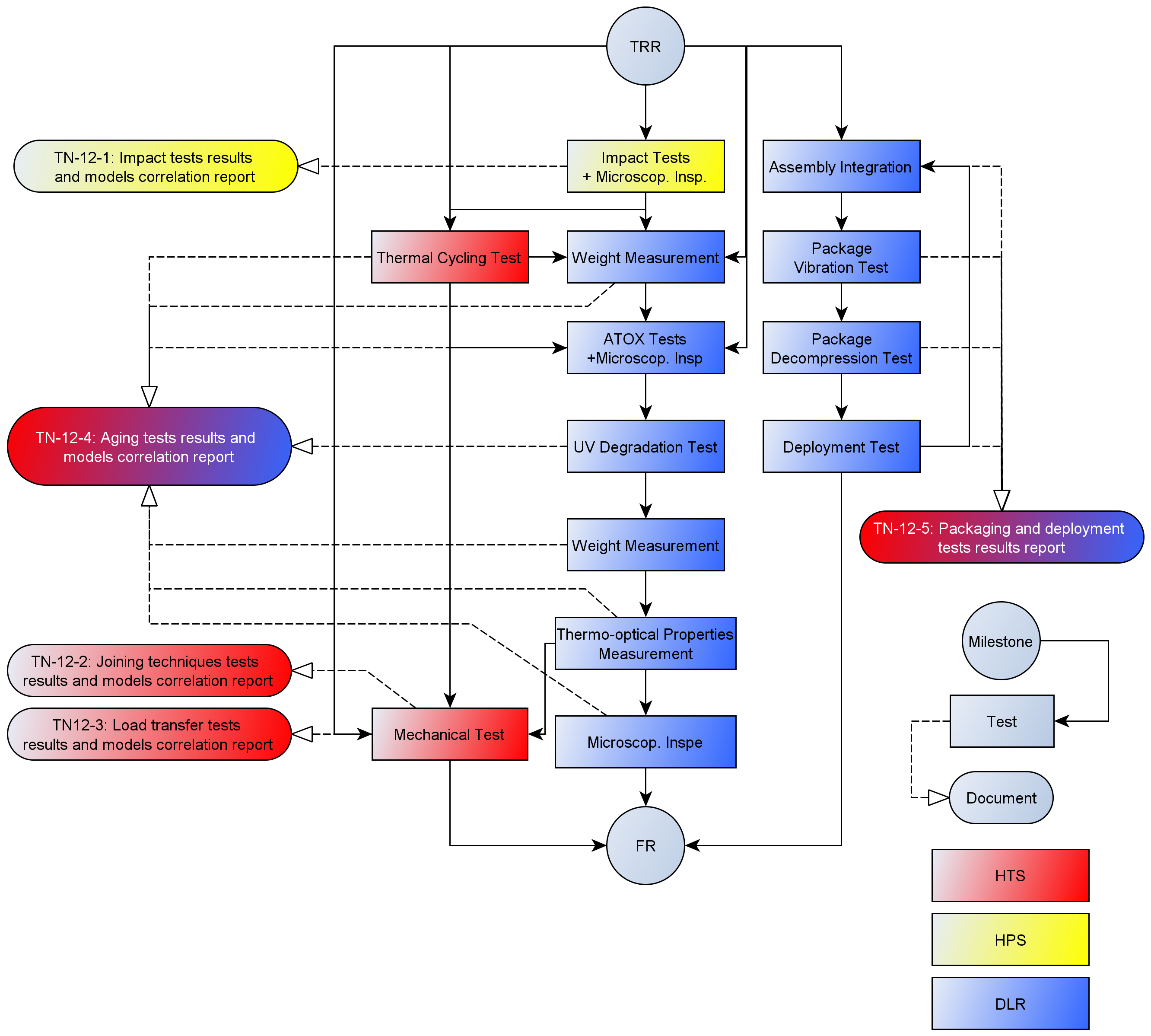
Test flow chart
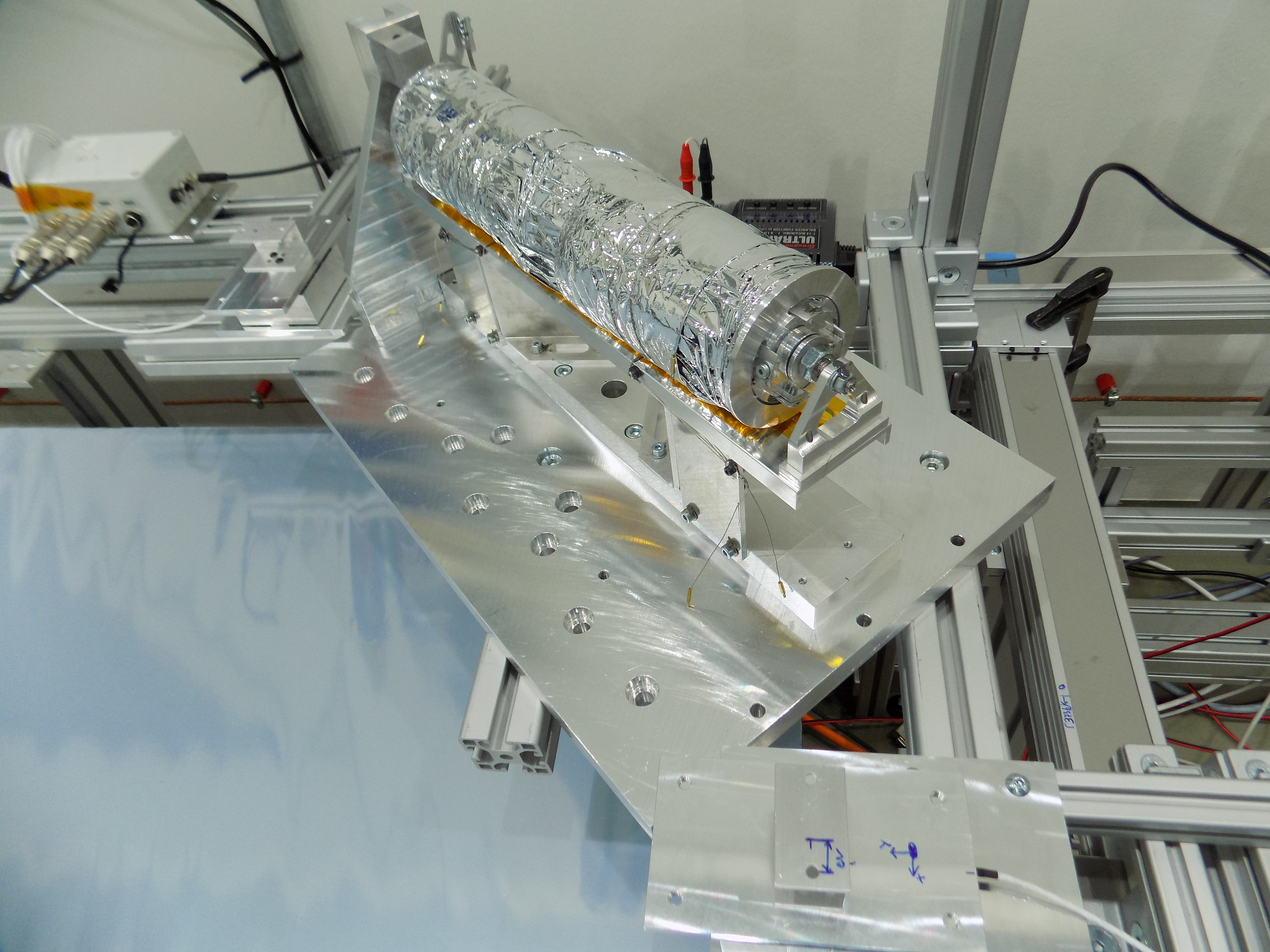
Deployment test 1
Credit HTS
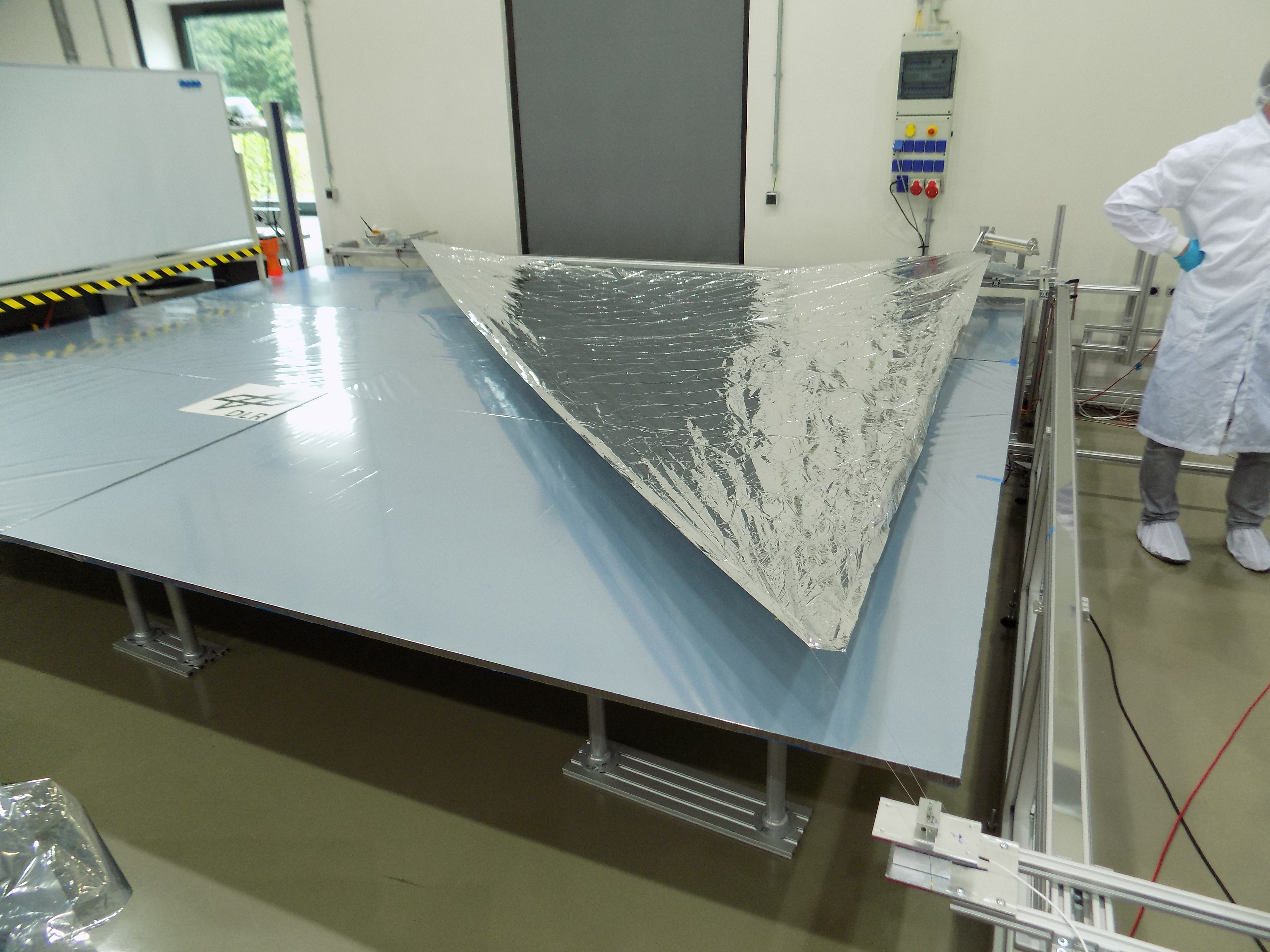
Deployment test 2 Credit HTS
The membrane has been designed taking into account the sail stresses, the interface forces, the slack and the crack yield parameters.
Finally the membrane was mounted on a spool and an ad-hoc designed test-rig to be tested according to the following logic:
For the membrane joints and manufacturing, the tests revealed that the AO-optimised double lap joints (DLJ) baselined for the demonstrator involve a very high manufacturing effort and a certain risk that quality decreases due to the small 4 mm fold that needs to be introduced manually above a 5 m length. The degradation tests did show that indeed there is a slight degradation at the cut edges; however this degradation does not increase in line with continuing atomic oxygen exposure.
It can therefore be concluded that an AO optimisation of the joints and cut edges is not necessary.
The results demonstrate that the conventional DLJ glued with 3M Transfer Tape 9460 is the preferred joint design for the deployable membrane.
The same is considered for the reinforced edges. The reinforced edge of the final membrane will be folded once and then glued by means of the 3M Transfer Tape 9460. A small material overlap of about 2 to 4 mm is considered sufficient to protect the adhesive layer from AO and UV degradation.
The membrane demonstrator has been equipped with crack stoppers, designed to stop crack growth in the high stress regions around the interface. Such cracks can grow as a result of space debris or micrometeorite impacts.
The next development stage should also take into account a potential upscaling of the deployable membrane, to allow for larger sails, so that the de-orbiting time can be effectively reduced. This is not only useful in order to reduce the risks of material degradation due to UV radiation, but also to reduce the risk of collisions with other debris and spacecraft and to effectively ‘clean up’ the orbit faster than the required 25 years.
In parallel to this activity, another Clean Space GSTP activity is running: “Architectural design and Testing of a passive de-orbiting sub-system”, with a twin team (HPS is prime and HTS, DLR Bremen and Etamax are subcontractors). The aim here is to develop the full subsystem, including the membrane, then test it. At the moment vibration tests are ongoing and this activity should be concluded at the beginning of 2017. The main achievements of this activity will be published as soon as it will be completed.
So stay tuned and de-orbit!!!
Discussion: no comments