This hardware is known as the avionics verification model, currently being built at an Airbus facility in Toulouse, France.
The model is being assembled in a laboratory-like environment where the spacecraft’s electrical units are mounted on the model. The missing units – such as the large solar arrays as well as the mission environment – such as the Sun and other stars – are simulated using a computer.
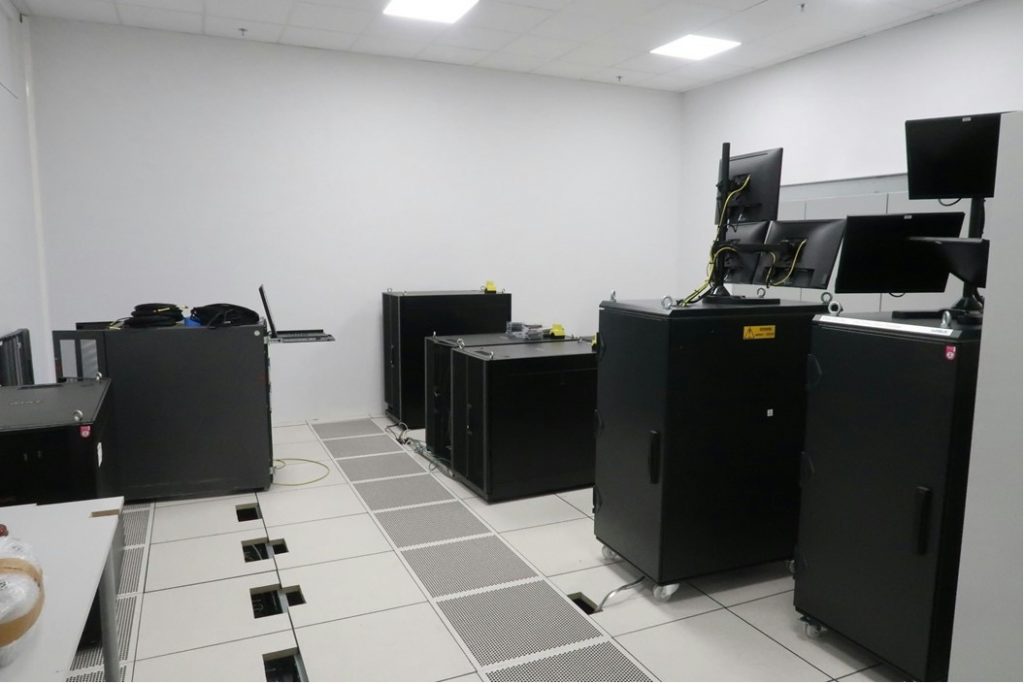
The flight software, crucial for commanding and controlling the units, is loaded onto the computer engineering model. Despite being referred to by different names, such as Avionics Verification Model, Avionics Test Bench or Flatsat (owing to the flat arrangement of units on a table), its primary purpose remains the same. It is used to rigorously test the electrical units in preparation for the assembly, integration, and testing phase of the spacecraft’s flight model and flight operations.
In the years ahead, the avionics verification model will play a crucial role in rehearsing procedures and validating hardware and software integration. Engineers from Airbus and Thales Alenia Space will use this model for an array of functional tests across all subsystems.
SYSTEM | FUNCTION |
Command and Data Handling | The spacecraft’s “brain” responsible for managing information. |
Guidance, Navigation and Control | Ensures accurate positioning and trajectory. |
Power | Manages solar array power collection and distribution. |
Communications | Maintains contact with Earth. |
Thermal Control | Monitors sensors and controls heaters. |
Propulsion | Controls engines. |
Payload Management | Coordinates with NASA’s payloads for sample return and communication with other Mars spacecraft. |
The first electrical units are integrated and are now being tested.
Conducting full functional tests on all subsystems helps verify their performance. These tests ensure communication between subsystems, accurate data storage and transmission, and control by the onboard computer.
Once all spacecraft avionics units and subsystems are assembled, it is time to run system-level tests. Performance tests validate the model’s adherence to operational requirements, while mission tests simulate all types of mission scenarios. These tests simulate critical mission phases, such as launch and Mars orbit insertion, and include failure.
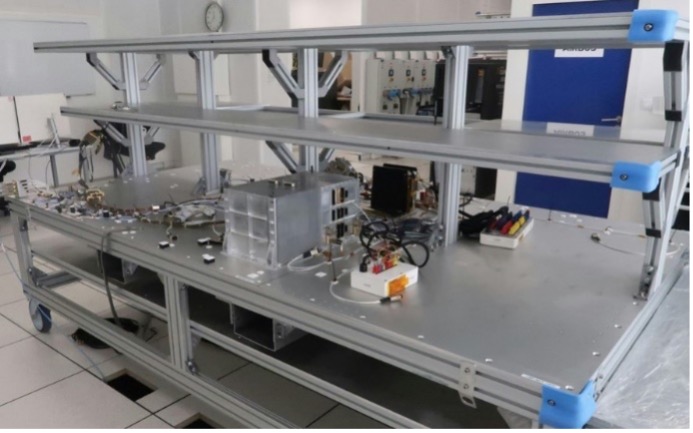
Airbus will use the Avionics Verification Model for several years to support avionics and software development. As more engineering models are integrated and software upgrades are implemented, this model will progressively evolve into an accurate replica of ERO.
After the launch and near-Earth commissioning of the orbiter, the model will move to ESA’s mission operations centre at ESOC in Darmstadt, Germany. It will remain there throughout the mission and will support testing until Mars samples return to Earth.
With a lifecycle spanning from the spacecraft’s developmental phase to the return of Mars samples, the model serves as a robust platform to ensure mission success.
By Stéphane Langlois, ESA coordinator of the Assembly, Integration, and Test phases for the Earth Return Orbiter
Discussion: no comments