A team of ESA and Airbus engineers tested a real mission concept for the rover prototypes to scout another planet dodging boulders, driving long distances, and fetching sample tubes – all of it without human intervention.
What are rovers, lightsabres and a piglet doing in a quarry?
The rovers
Codi. This four-wheeled rover, equipped with a robotic arm and a powerful computer vision system, was instructed to drive to targets with an accuracy of 10 cm. Codi uses can locate a sample tube, pick it up and store it autonomously.
Codi uses stereo cameras to build up a 180-degree map of the surroundings and plan its maneouvres. Once parked in front of the target sample, the camera on top of the mast detects the tube and estimates its position with respect to the rover. The robotic arm initiates a complex choreography to move closer to the sample, fetch it and store it.
Codi is also capable of traversing autonomously hundreds of metres across several obstacles – from flat and straight-line traverses to rocky, zig-zagging setups.
Charlie. The six-wheeled rover has a “triple bogie” suspension – just like the ExoMars Rosalind Franklin rover – and can navigate obstacles as tall as the diameter of its wheel without getting stuck or falling on its side. Engineers used Charlie to test a new navigation system that could speed up rover missions on the Moon and Mars.
This capability could lead to improved performance for ESA’s ExoMars Rosalind Franklin rover mission, which is expected to launch in 2028. Charlie’s success could also be useful for a Moon rover covering great distances on the lunar surface.
The lightsabres
This sample tube is a replica of the hermetically sealed samples inside which NASA’s Perseverance rover is collecting precious martian soil.
About the size and shape of a standard lab test tube, the titanium tubes are called RSTA, short for Returnable Sample Tube Assembly.
To most people on Earth, they resemble lightsabres.
The quarry
The field trials took place at a quarry near Leighton Buzzard, in the South of England.
The reddish terrain, although not fully representative of Mars in terms of soil composition, had plenty of slopes and rocks of different sizes, similar to what a rover might encounter on the martian surface.
Testing rovers outdoors is essential because it provides a unique and dynamic landscape that cannot be replicated indoors in any facility.
The quarry gave engineers the flexibility to present the robot with several challenges at varying speeds such as adding obstacles between waypoints, or altering the sequence of commands to see which course of action the rover decided to take.
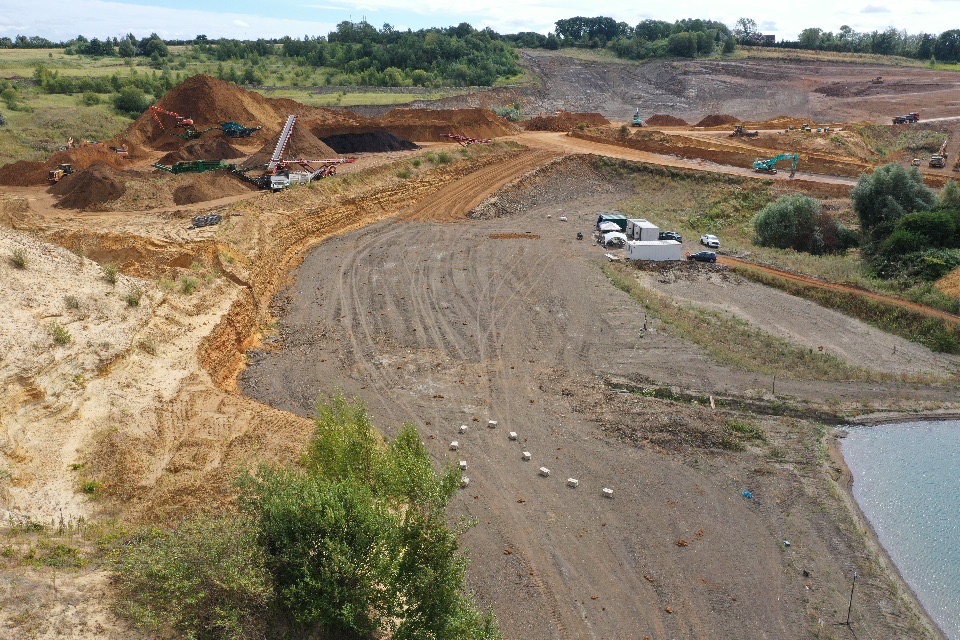
Drone view of the terrain where the tests took place at LB Silica Sands quarry in the UK. Credits: Airbus
Fun fact: This sand quarry was also the setting for one of the scenes of the film Mission: Impossible – Dead Reckoning.
The tests
Imagine driving blindfolded on another planet. For a rover with a robotic arm to be able to arrive somewhere within 10 to 15 centimetres of accuracy after having driven hundreds of metres, and then find and collect samples, is a real achievement.
These smart rovers proved that they could do it by themselves.
At the control room, engineers were busy following the moves of the rover on their screens using a 3D environment, mimicking real mission procedures.
Charlie was also trialling a sensor known as LiDAR, which can allow rovers to move in the dark without using cameras.This technology would be extremely useful for missions on the Moon, where lighting conditions are challenging with lunar nights lasting about 14 Earth days.
What’s new?
During this third rover campaign, the teams tested new operations and procedures:
- Wheels. Codi’s used special tires for the ride. NASA lent mesh wheels made with a memory shape alloy. Engineers tested their locomotive performance for martian exploration.
- Long and stressful drive. The rovers were faced with increasing challenges. New paths, longer drives, repositioning and sun orientation stressed the system.
- Depot. Automated transition to depot operations after long traverse.
- 3D vision. An upgraded 3D software ran in parallel to the field action, mimicking the real mission procedures.
Why are rovers back to the field?
ESA continues to fund research using the rovers to maintain and develop know-how and new capabilities in Europe.
Testing technologies creates competence and generates confidence towards success. The trials prepare the teams for the challenges to come and make them ready for future missions.
The demo brought together the technologies developed in several European countries mainly under ESA funding for planetary exploration. The list of technologies tested is long: autonomous navigation, localisation, robotic manipulation, computer vision, absolute heading estimation – the orientation of the rover – based on the position of the sun, and ground control software, to name a few.
The maturity of space robotic systems also has applications on Earth and is triggering partnerships on mobility solutions.
The piglet
Meet Kevin, the rover team mascot. This piglet has been present during the three weeks of testing.
Its story is one of cuteness and positivity. Knitted by hand by a team member’s partner in difficult times, it is now an integral part of the team and their lucky charm for the Moon, Mars and beyond.
Discussion: no comments