Next up in our look at national contributions to the European Service Modules for Artemis is Italy.
To start with the very beginning of a European Service Module, Thales Alenia Space (a joint venture between Thales 67% and Leonardo 33%) produces the structure for the module. The barebone unit acts like a chassis on a car providing the solid foundations for all other elements of the Orion spacecraft to be built upon and it also absorbs the forces that the spacecraft will endure during launch into Earth orbit and onto the Moon.
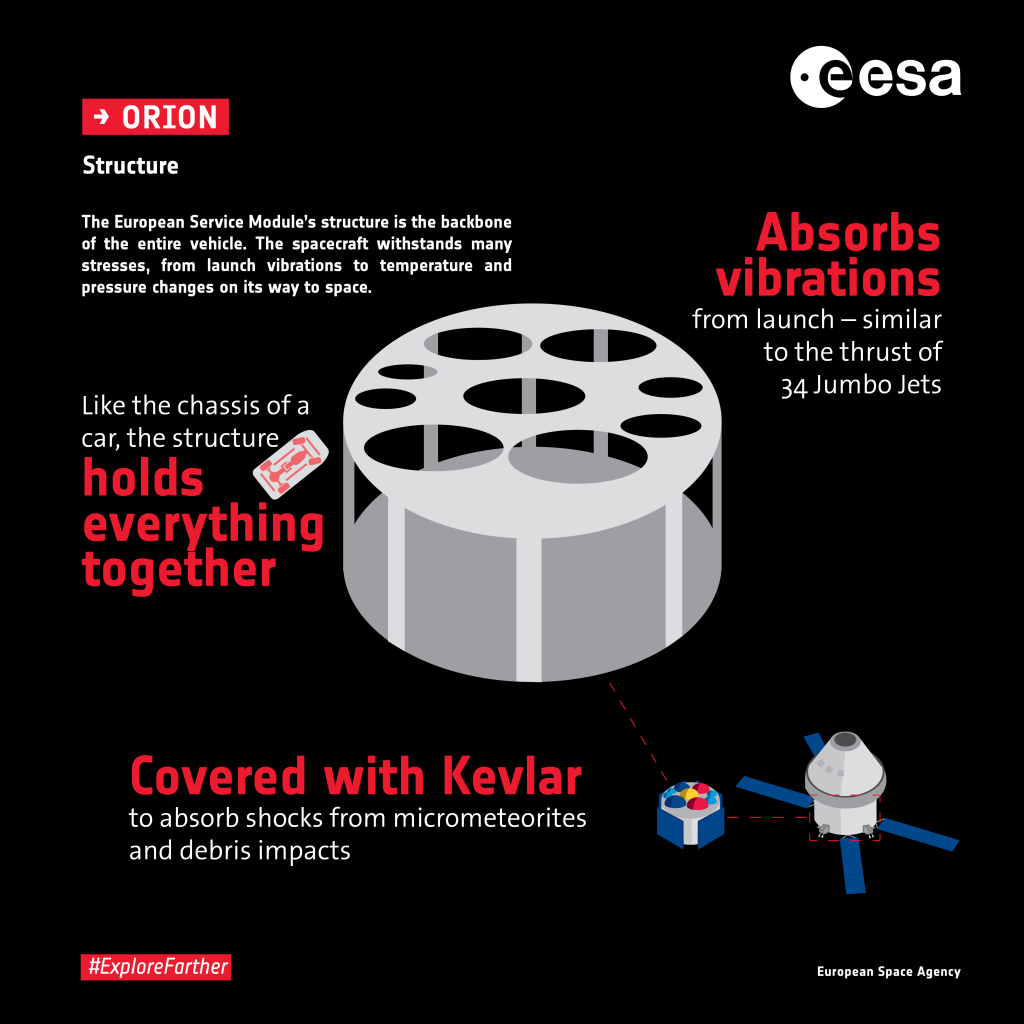
It all starts in Turin, Italy, where technicians assemble the primary structure that is made from a core of Composite Fibre Reinforced Polymer sandwich panels and aluminium alloy elements for the secondary structures. This technology keeps the European Service Module light enough to fly farther and longer but strong enough to keep its shape.
Before being put into production, a European Service Module test article was pushed and pulled by 72 jacks simulating almost one and half more stress that the real service modules will endure. Obviously the structure passed with flying colours and went into production. The engineers at Thales Alenia Space did not stop there though, and the third structure for Artemis III has been made even lighter while keeping its strength!

The structures are trucked from Turin to Bremen, Germany, where the rest of the hardware that makes a spacecraft can be installed. The 1200 km trip takes around a week in a specially designed container that keeps the structure safe and at the right humidity and temperature.
Keeping it cool
Whereas in your home, radiators use water to transfer heat, the European Service Module radiators use the liquid HydroFluoroEther. Thales Alenia Space supplies the radiators for this that consist of six elements forming two independent systems for each European Service Module. Another difference with your home radiators that keep your house warm, is that like a car’s radiator system the European Service Module radiators are designed to expel excess heat and keep the computers and other components from overheating.
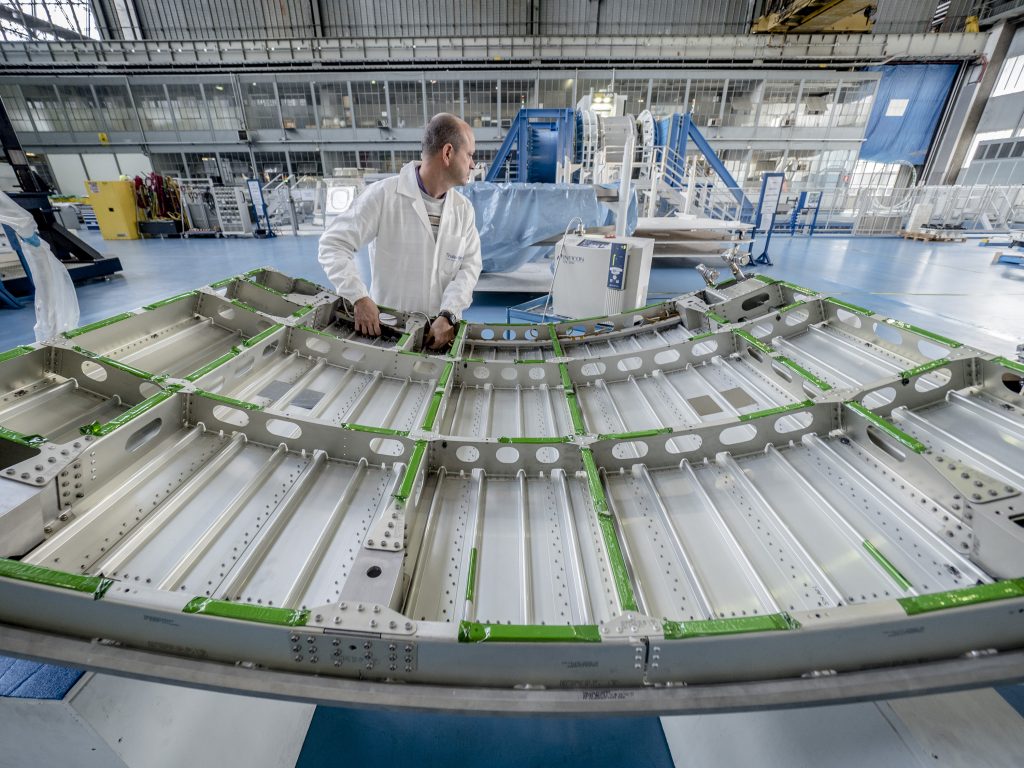
An integral part of the cooling system is the cold plates that allow heat to be removed efficiently without air and where space is a premium – both a factor in the tight-fit European Service Module. Cold plates use the excellent conducting properties of metals, and are often found in desktop computers too. The HydroFluoroEther liquids pass through a metal plate that conducts the heat away. Note that the cold plates discussed here are not to be confused with “antipasto freddo”, a different type of cold plate that Italy is also renowned for.
The cold plates are supplied by Italian company DTM Technologies based in Modena, a small company that has been supplying hardware for space for many decades. Specialising in heat transfer, DTM Technologies components have flown on the Space Shuttle and the International Space Station’s flagship dark-matter hunter experiment AMS-02. Their temperature analysis hardware was also included in the Matroshka spaceflight dummy that was bolted outside the International Space Station to monitor radiation. This experiment is a direct forerunner to the radiation-test passengers that will fly with Artemis I.
Valves for air
The next component from Italy might not be the most visible or largest, but it is extremely important: the valves that regulate the supply of oxygen and nitrogen to form breathable air for astronauts. CrioTec, based near Turin, is specialised in all types of cryogenic and vacuum components and supplies to another large organisation that requires utmost precision and reliability: CERN. Their product catalogue includes a filter for “Big Physics” which says all.
Valves might seem a small part to make at first, but anybody who has had a leaking water tap at home should realise how difficult it is to design and make a component that can let matter through, but also stop it on demand. Water molecules are much larger than nitrogen or oxygen and making anything airtight is not easy, now imagine doing it in space and being able to turn it off and on at will.
As experts in the domain of valves, vacuum and cooling, Thales Alenia Space tested the temperature control setup for Orion in a CrioTec facility to prove the concept back in 2016.
Hydration is important
The European Service Modules include four water tanks that hold around 80 l of water each for the astronauts on their voyage around the Moon. These are made near Turin at Sommariva del Bosco by Alfa Meccanica. They make the cylindrical structure of the water tank and the covers so the astronauts on the Artemis II and onwards mission can drink, hydrate their food and refresh themselves. With over 50 employees Alfa Meccanica specialises in high-precision machining and includes precision cleaning processes in its product line, to keep the water extra fresh. The drinking water itself will be sourced from a source closer to the launchpad in USA.
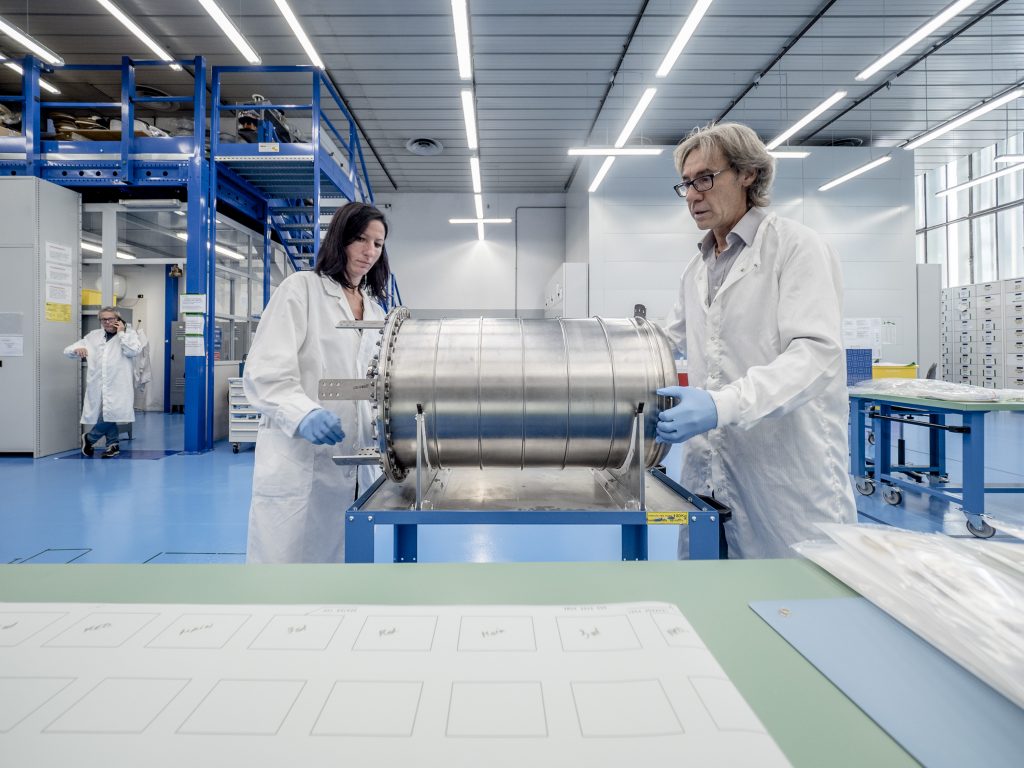
Space spider-net
Another Turin company, Aviotec, supplies the “spidernets” for the European Service Modules. A surprisingly cool name (and not an acronym for once), spider-nets are the belts that hold a layer of Kevlar-protection at the bottom part of the Orion spacecraft. Aviotec has supplied parts for many International Space Station modules and spacecraft including the Cupola, Node-3 as well as the supply truckers Automated Transfer Vehicles, and Northrop Grumman’s Cygnus spacecraft. Supplying the insulation blankets that have been protecting the outpost orbiting our planet for over two decades is proof that they are a good choice.
Solar power
All of the above with exception of the spider-nets wouldn’t do much without electricity, and this is where Leonardo S.p.a. and CBL electronics as subcontractor help out, supplying and testing the Power Conditioning and Distribution Units built in Milan for the European Service Modules. These units take the solar-generated power, regulate it to a nice even supply and distribute it to where it is needed – similar to a power supply in a desktop computer but without the fan and much more precise and dependable.
But first the electricity must be generated, here Leonardo is at the source, the company provides the photovoltaic panels for the solar array wings. On each ESM there are four “wings” comprised of three photovoltaic panels for a total length of seven meters each, capable of providing a total of about 11 kilowatts.
The individual panels that convert our Sun’s rays into electricity are again made in Milan by Leonardo and sent to The Netherlands for further processing – more on this in a future blog entry.
When on Earth the electricity needs to arrive at the power units via other means, see the entry on Denmark’s contributions to Artemis for details on the stand-in electricity generators.
Leonardo has a huge product portfolio and is involved in many ESA missions as well as international partners, from the James Webb Telescope to the International Space Station to asteroid and planet hunters OSIRIS-Rex and JUICE, their website lists the missions very well.
From Italy, via Germany and USA, to the Moon
This exhaustive list of some of Italian’s finest space products are just a few of the thousands of components that make up the European Service Modules. Transported by truck to the Airbus integration halls in Bremen, Germany, they are assembled into one European Service Module. Once complete the module is flown to NASA’s Kennedy Space Center in Florida, USA, and integrated with Orion, the SLS rocket and to the launchpad, forward to the Moon!
European Service Modules: made in Italy
Il successivo contributo nazionale agli European Service Module per Artemis è quello dell’Italia.
Per cominciare dalle basi, la struttura del modulo viene prodotta da Thales Alenia Space (joint venture costituita per il 67% da Thales e per il 33% da Leonardo). L’unità essenziale agisce come il telaio su un’automobile, fornendo la solida base per tutti gli altri elementi su cui costruire la navicella spaziale Orion, e, inoltre, assorbe le forze che il veicolo spaziale si trova ad affrontare durante il lancio nell’orbita terrestre e verso la Luna.
Tutto ha inizio a Torino, dove i tecnici assemblano la struttura di base, composta da un’anima di pannelli sandwich in materiali rinforzati con fibre a matrice polimerica, e le strutture secondarie, costituite da elementi in lega di alluminio. Questa tecnologia consente allo European Service Module (ESM, Modulo di Servizio Europeo) di mantenere un peso sufficientemente leggero per volare più lontano e per più tempo, ma anche una solidità sufficiente a conservare la forma.
Prima della messa in produzione, un modulo ESM di prova è stato spinto e tirato da 72 martinetti che hanno simulato quasi una volta e mezza lo stress a cui saranno sottoposti i moduli veri e propri. Come ci si aspettava, la struttura ha superato brillantemente il test passando alla fase di fabbricazione. Tuttavia, gli ingegneri di Thales Alenia Space non si sono fermati qui e hanno realizzato una terza struttura per Artemis III ancora più leggera, pur mantenendo invariata la forza.
Gli ingegneri di Thales Alenia Space davanti alla terza struttura di ESM. Crediti: Thales Alenia Space
Le strutture vengono poi spedite da Torino a Brema, in Germania, dove vengono installati i restanti componenti del veicolo spaziale. Il breve viaggio di 1.200 km dura circa una settimana e viene effettuato con l’impiego di un container appositamente progettato che tiene la struttura al sicuro mantenendone i giusti livelli di umidità e temperatura.
Raffreddamento
Se i radiatori domestici usano l’acqua per trasferire il calore, i radiatori dello European Service Module impiegano l’idrofluoroetero liquido. Thales Alenia Space fornisce i radiatori, composti da sei elementi che formano due sistemi indipendenti per ciascun modulo. I radiatori spaziali si distinguono da quelli casalinghi anche per l’espulsione del calore in eccesso che evita il surriscaldamento di computer e altri componenti, proprio come accade nelle automobili.
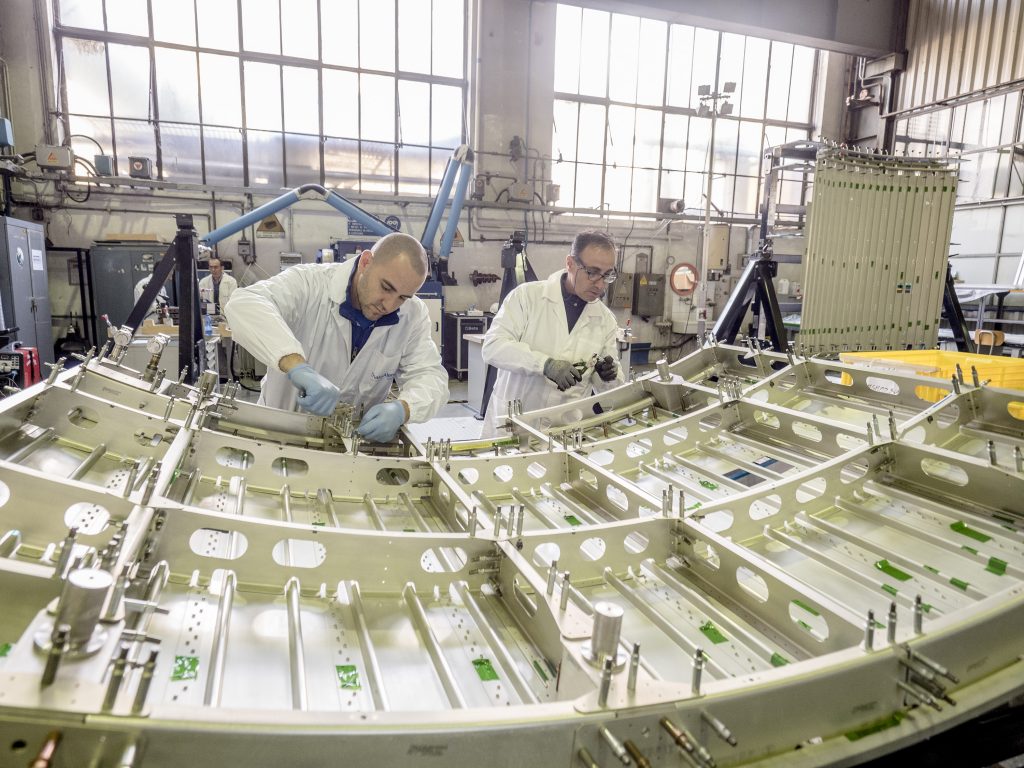
Parte integrante del sistema di raffreddamento sono le piastre fredde che consentono la rimozione efficace del calore in assenza di aria dove lo spazio non manca, fattore decisivo nel precisissimo European Service Module. Le piastre fredde usano le eccellenti proprietà conduttrici dei metalli, per questo vengono impiegate spesso anche per i computer desktop. Gli idrofluoroeteri liquidi passano in una piastra metallica che dissipa il calore. Da notare che le piastre o ‘piatti freddi’ qui citati non sono da confondere con un diverso tipo di piatto freddo per cui l’Italia è anche famosa, l’antipasto freddo.
Le piastre fredde vengono fornite dall’azienda DTM Technologies di Modena, una piccola realtà che produce componenti spaziali da molti decenni. Adibiti al trasferimento del calore, i componenti di DTM Technologies hanno volato sullo Space Shuttle e nell’esperimento sulla materia oscura della Stazione Spaziale Internazionale AMS-02. I componenti per l’analisi della temperatura di DTM sono stati anche usati nel manichino usato per il volo spaziale Matroshka che è stato installato all’esterno della Stazione Spaziale Internazionale per monitorare le radiazioni. Questo esperimento è un precedente diretto per i passeggeri soggetti a test delle radiazioni che voleranno con Artemis I.
Valvole per l’aria
Il successivo componente italiano non sarà quello più visibile data la modesta mole, ma è estremamente importante: le valvole che regolano la fornitura di ossigeno e azoto per creare aria respirabile per gli astronauti. CrioTec, con sede vicino a Torino, è specializzata in tutti i tipi di componenti che generano il freddo e il vuoto e rifornisce un’altra grande organizzazione che necessita di precisione e affidabilità assolute: il CERN. Il loro catalogo prodotti comprende un filtro per gli esperimenti fisici di grandi dimensioni.
Le valvole potranno anche sembrare un piccolo componente a prima vista, ma chiunque abbia sperimentato le perdite di un rubinetto sa bene quanto può essere difficile progettare e realizzare un componente che consente alla materia di fluire e al contempo ne interrompe il flusso quando è necessario. Le molecole di acqua sono molto più grandi di quelle dell’azoto e dell’ossigeno, quindi creare l’ermeticità non è affatto semplice, figurarsi nello spazio.
Grazie all’esperienza nel campo delle valvole, del vuoto e del freddo, Thales Alenia Space ha testato la configurazione di controllo della temperatura per Orion in uno stabilimento CrioTec per verificare l’idea già nel 2016.
L’importanza dell’idratazione
I Moduli di Servizio Europei ESM comprendono quattro serbatoi che contengono circa 80 litri d’acqua ciascuno, destinati agli astronauti e alle astronaute in viaggio verso la Luna. Anche questi elementi vengono realizzati nei pressi di Torino, precisamente a Sommariva del Bosco, dall’azienda Alfa Meccanica, che produce la struttura cilindrica del serbatoio d’acqua con le relative coperture, in modo che gli astronauti e le astronaute a bordo di Artemis II e delle successive missioni possano bere, reidratare il cibo e lavarsi. Forte di un personale costituito da oltre 50 unità, Alfa Meccanica è specializzata in lavorazioni di alta precisione e tra i propri prodotti vanta strumenti di pulizia idrica che mantengono l’acqua freschissima. L’acqua potabile proviene da una sorgente vicina alla rampa di lancio negli Stati Uniti d’America.
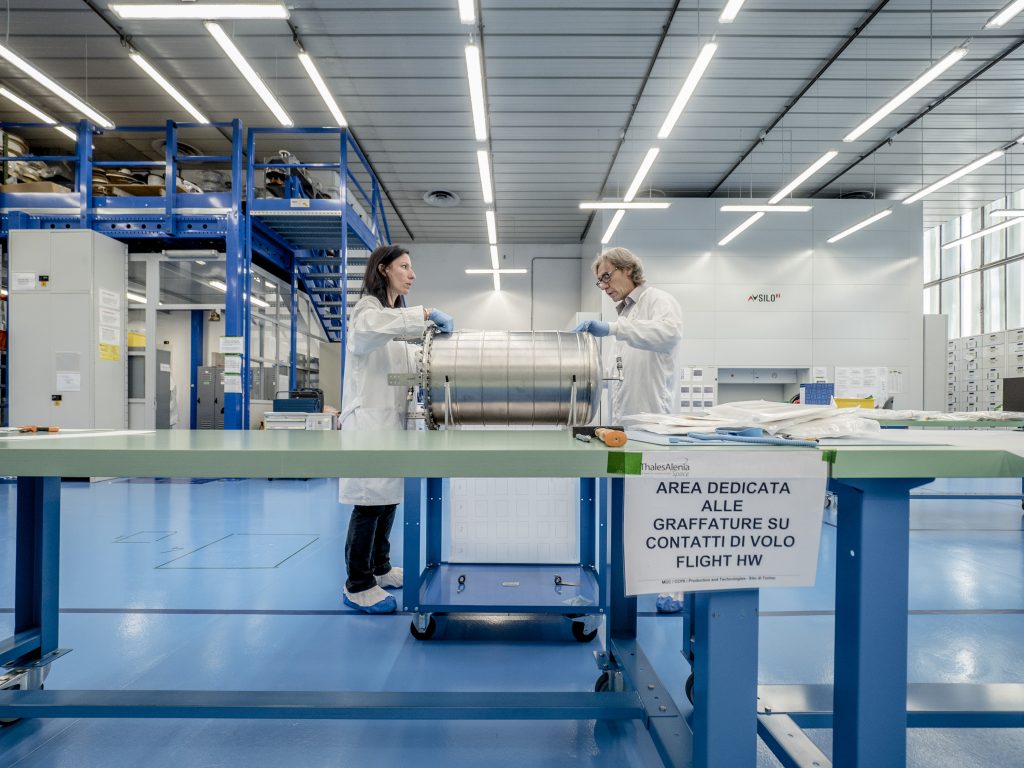
Al lavoro per i serbatoi d’acqua per ESM. Crediti: NASA–Radislav Sinyak
La ragnatela spaziale
Un’altra azienda torinese, Aviotec, fornisce le “ragnatele spaziali” per gli European Service Module. Un nome fantastico (una volta tanto non si tratta di un acronimo), visto che le ragnatele sono cinghie che fissano uno strato di protezione Kevlar in fondo al veicolo spaziale Orion. Aviotec ha fornito componenti per diversi moduli della Stazione Spaziale Internazionale, tra cui Cupola e Node-3, nonché i veicoli di trasferimento automatizzati ATV e il veicolo spaziale Cygnus di Northrop Grumman. Aver fornito le coperture isolanti che hanno protetto l’avamposto orbitante attorno al nostro pianeta per oltre due decenni è la prova della qualità dei prodotti di quest’azienda.
La potenza solare / Energia solare
Tutti i componenti di cui abbiamo parlato finora, fatta eccezione per le ragnatele, non funzionerebbero senza elettricità ed è per questo che Leonardo S.p.a. e la subappaltatrice CBL electronics forniscono e testano le unità di condizionamento e distribuzione dell’alimentazione fabbricate a Milano per gli European Service Module. Queste unità prendono l’energia solare, la uniformano e la distribuiscono dove serve, proprio come un gruppo di alimentazione in un computer desktop, ma senza ventola e in modo molto più preciso e affidabile.
Ma prima di essere distribuita, l’energia elettrica deve essere prodotta. E qui entra in gioco Leonardo, azienda che fornisce i pannelli fotovoltaici per le ali dei pannelli solari. Su ciascun ESM sono presenti quattro ‘ali’, composte da tre pannelli fotovoltaici per una lunghezza totale di 7 metri ciascuno, in grado di fornire un totale di circa 11 kW.
Anche i singoli pannelli che convertono i raggi solari in energia elettrica sono prodotti a Milano da Leonardo per poi essere trasferiti nei Paesi Bassi per ulteriori lavorazioni, di cui parleremo in futuri articoli del blog.
Sulla Terra, a scopo di test, l’elettricità deve arrivare all’unità di alimentazione tramite altri mezzi (leggi il contributo della Danimarca ad Artemis per maggiori dettagli sui generatori di elettricità sostitutivi).
Leonardo vanta una vastissima gamma di prodotti ed è coinvolta in numerose missioni dell’ESA e collaborazioni con altri partner internazionali, dal telescopio James Webb alla Stazione Spaziale Internazionale fino ai cercatori di asteroidi e pianeti OSIRIS-Rex e JUICE, come si può vedere dagli elenchi delle missioni pubblicate sul suo sito web.
Dall’Italia alla Luna passando per Germania e Stati Uniti
Questo elenco di raffinatissimi prodotti spaziali italiani è solo un esempio delle migliaia di componenti che costituiscono gli European Service Module. Trasportati su ruota agli hangar di integrazione Airbus a Brema, in Germania, vengono poi assemblati a formare un modulo European Service Module. Una volta assemblato, il modulo viene spedito al Kennedy Space Center della NASA in Florida e integrato con Orion, il razzo SLS, e sulla rampa di lancio alla volta della Luna.
Discussion: no comments