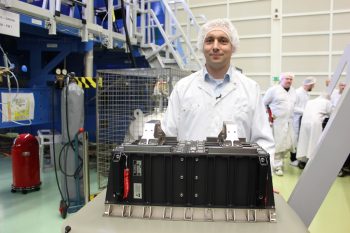
The Propulsion Drive Electronics or PDE box. Credit: Airbus DS
Airbus recently announced that it has delivered the Propulsion Drive Electronics, or PDE, to the Orion Service Module integration hall – this is the real thing that will fly on the first Exploration Mission-1 around the Moon.
The computers inside the black box will control the propulsion system to direct and propel the first Orion mission around the Moon. And they have a lot of work to do. Commands to move the spacecraft involve driving valves, thrusters, tanks, and gimbals – all while checking pressure and temperature sensors to ensure all elements work perfectly together.
The computers are so precise they manage accurate timing of the valves opening and closing, to ensure thruster firings with a precision down to the millisecond. The PDE drives thrusters that were designed and built decades apart; the main engine on Orion is a repurposed Shuttle engine from the 1980s; while the 24 attitude thrusters are of a more recent design and used on Europe’s Automated Transfer Vehicle. Each thruster type has different methods of control and the PDE is designed to instruct each as needed, adapting to the interface of three types of engines while calculating time of firing, the fuel required and the direction of the thruster.
Such an important element comes with a spare included – there is no easy maintenance when you are over 300 000 km from Earth – each PDE has a ‘redundant’ copy – if ever one should fail, the other will take over seamlessly.
These computers need to be put through their paces so extensive testing is running in parallel. A functional model of the PDE is being tested in Denver, Colorado, USA, to see how they work together with the other subsystems. Two more models are being tested at a facility in Les Mureaux, France, for more quality control. Lastly two PDE models are being tested together with real propulsion hardware and propellant on the Propulsion Qualification Model at NASA White Sands Test Facility, New Mexico, USA. Work on Orion is running across continents 24 hours a day.
Discussion: no comments