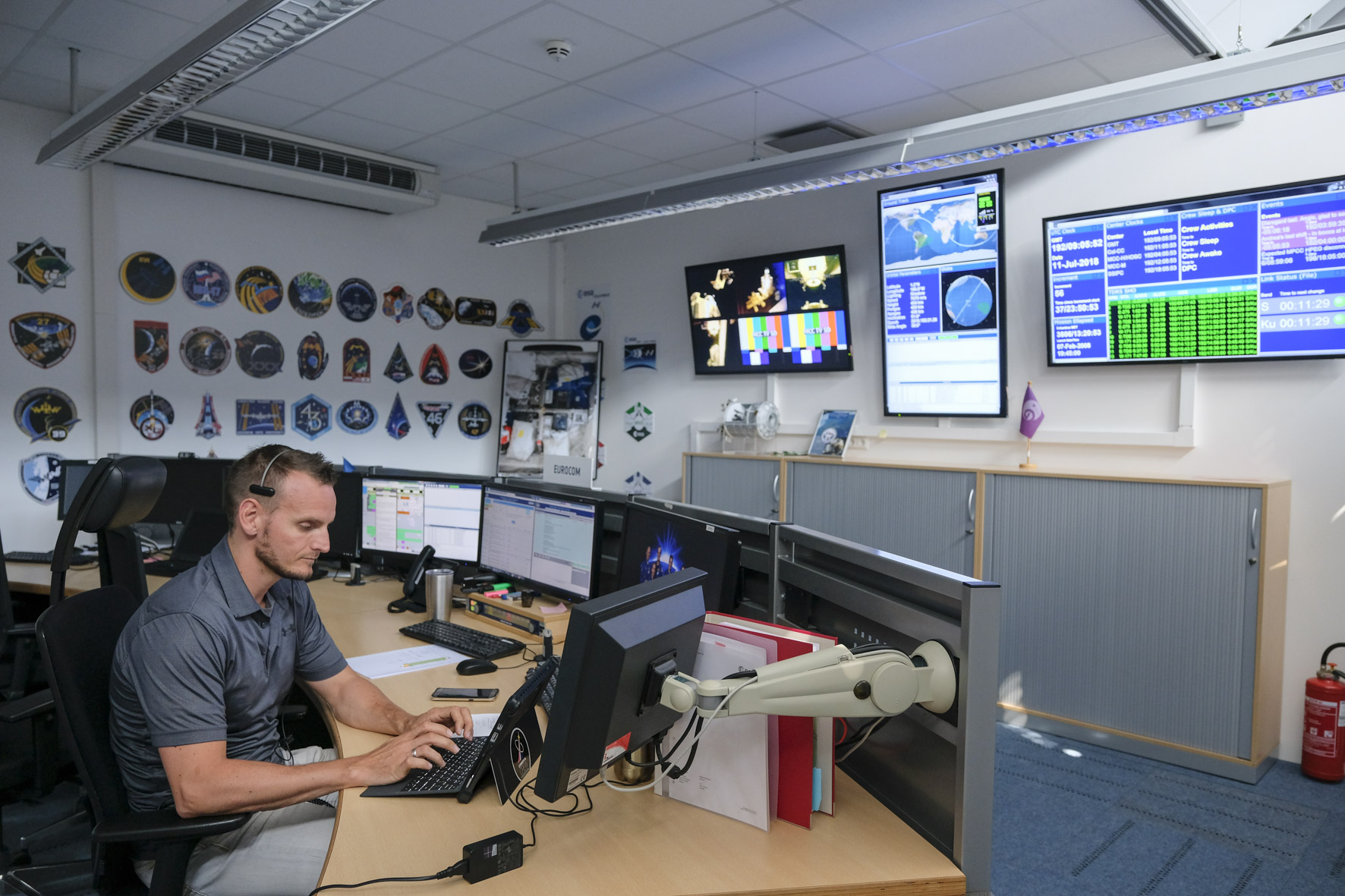
Operations
(English) A backbone network for a robotic arm
(English) The robotic arm gently transfers the astronaut to the far end of the International Space Station to install a radiator on the Russian side. A mix of commands and data flows between the robot and the human in outer space, and between the crew inside the station and the teams on Earth.
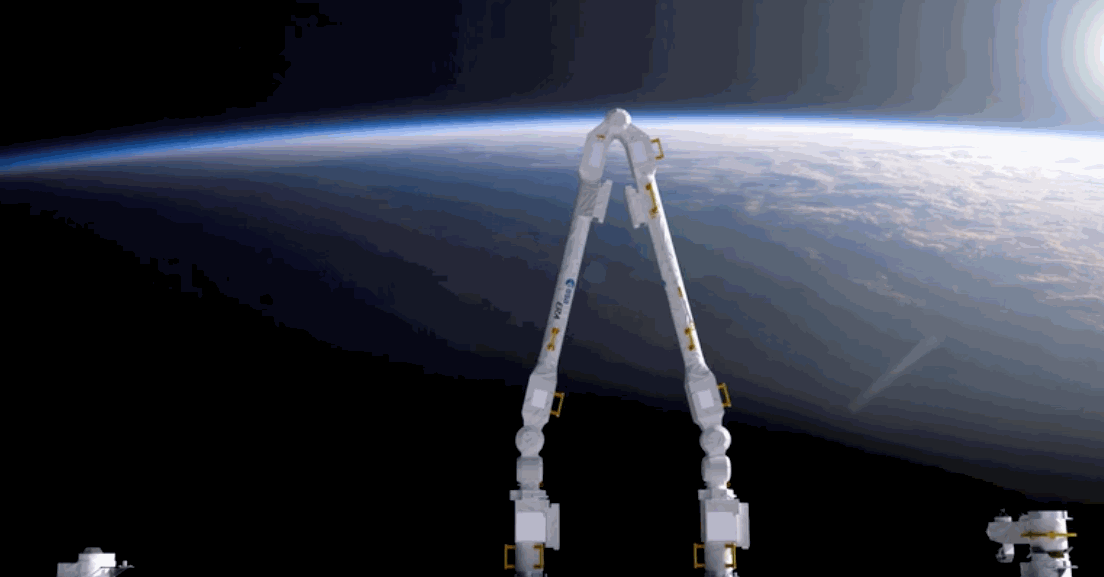